The final sintering temperature is critical because it directly influences the microstructure, mechanical properties, and overall quality of the sintered material. It determines the extent of densification, grain growth, and phase transformations, which are essential for achieving the desired material properties such as strength, durability, and performance. Precise control of the final sintering temperature ensures optimal sintering kinetics, minimizes defects, and aligns the final product with its intended application requirements.
Key Points Explained:
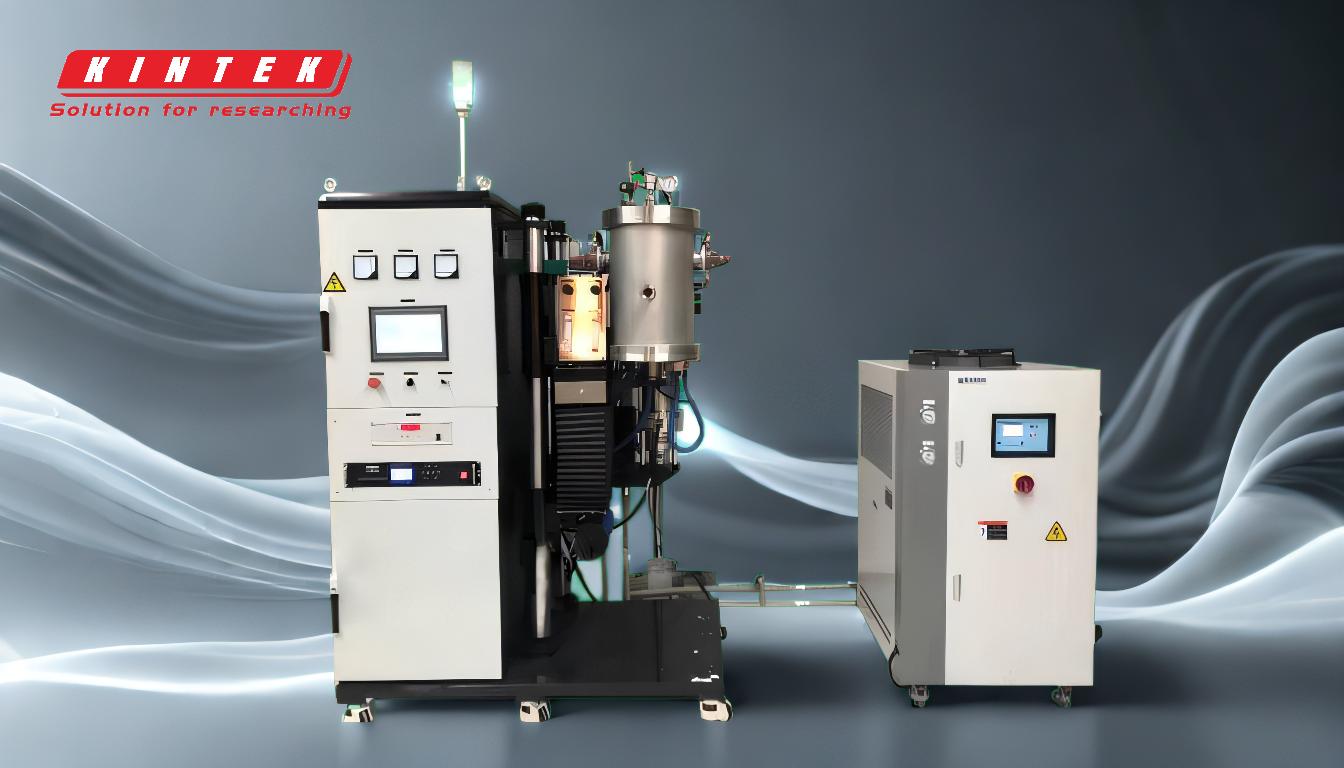
-
Impact on Densification and Microstructure:
- The final sintering temperature governs the degree of densification, which is the process of reducing porosity and increasing material density. Higher temperatures enhance particle bonding and diffusion mechanisms, leading to a more compact and homogeneous microstructure.
- Grain growth is also influenced by temperature. Excessive temperatures can lead to uncontrolled grain growth, which may degrade mechanical properties, while insufficient temperatures may result in incomplete sintering and residual porosity.
-
Mechanical Properties:
- High-temperature sintering improves key mechanical properties such as tensile strength, bending fatigue strength, and impact energy. These properties are critical for materials used in demanding applications, such as aerospace, automotive, and medical devices.
- The final temperature ensures that the material achieves the desired hardness, toughness, and wear resistance, which are essential for long-term performance.
-
Phase Transformations and Material Composition:
- The final sintering temperature can trigger phase transformations, such as the formation of new crystalline phases or the stabilization of specific microstructures. These transformations significantly influence the material's thermal, electrical, and mechanical properties.
- For materials with complex compositions, the final temperature must be carefully selected to ensure uniform distribution of phases and prevent undesirable reactions or segregation.
-
Sintering Kinetics and Diffusion Mechanisms:
- Temperature is a primary driver of sintering kinetics, affecting processes like grain boundary diffusion and bulk diffusion. These mechanisms are responsible for particle bonding and densification.
- Higher temperatures accelerate diffusion, enabling faster sintering and better particle rearrangement. However, the heating rate and cooling rate must also be controlled to avoid thermal stresses or uneven sintering.
-
Control of Porosity and Defects:
- The final sintering temperature plays a crucial role in minimizing porosity and eliminating defects. Proper temperature control ensures that the material reaches its theoretical density without introducing cracks or voids.
- Incomplete sintering due to insufficient temperature can leave residual porosity, which weakens the material and reduces its performance in critical applications.
-
Influence of Sintering Environment:
- The sintering atmosphere (e.g., air, vacuum, or inert gases) interacts with the final temperature to affect the material's properties. For example, a vacuum environment can prevent oxidation and enhance densification at high temperatures.
- The choice of sintering furnace and its temperature uniformity are also critical to achieving consistent results across the entire material.
-
Application-Specific Requirements:
- The final sintering temperature must align with the intended application of the material. For instance, materials used in high-temperature environments may require sintering at elevated temperatures to ensure stability and performance under operating conditions.
- The temperature is often tailored to achieve specific properties, such as thermal conductivity, electrical resistivity, or corrosion resistance, depending on the application.
-
Process Optimization and Consistency:
- Precise control of the final sintering temperature ensures process repeatability and consistency, which are essential for industrial production. Variations in temperature can lead to batch-to-batch inconsistencies, affecting product quality and reliability.
- Advanced sintering techniques, such as spark plasma sintering or hot isostatic pressing, rely on accurate temperature control to achieve superior material properties.
In summary, the final sintering temperature is a critical parameter that directly impacts the material's microstructure, mechanical properties, and overall performance. It must be carefully selected and controlled to meet the specific requirements of the material and its intended application, ensuring optimal results and consistent quality.
Summary Table:
Aspect | Impact of Final Sintering Temperature |
---|---|
Densification & Microstructure | Governs porosity reduction, particle bonding, and grain growth. Higher temperatures enhance homogeneity. |
Mechanical Properties | Improves tensile strength, hardness, toughness, and wear resistance for demanding applications. |
Phase Transformations | Triggers formation of new phases, influencing thermal, electrical, and mechanical properties. |
Sintering Kinetics | Accelerates diffusion mechanisms for faster sintering and better particle rearrangement. |
Porosity & Defects | Minimizes porosity and defects, ensuring material reaches theoretical density. |
Sintering Environment | Interacts with atmosphere (e.g., vacuum) to enhance densification and prevent oxidation. |
Application Requirements | Aligns temperature with material's intended use, ensuring stability and performance. |
Process Consistency | Ensures repeatability and consistency in industrial production, avoiding batch-to-batch variations. |
Need help optimizing your sintering process? Contact our experts today for tailored solutions!