The importance of metal melting temperature lies in its direct influence on the properties and performance of metals during manufacturing and application. Melting and re-cooling metals involve intricate crystallization processes that can significantly alter their mechanical, thermal, and electrical properties. Additionally, in processes like Plasma-Enhanced Chemical Vapor Deposition (PECVD), understanding and controlling the melting temperature of materials, such as electrodes, is crucial for optimizing process efficiency and achieving high-quality crystal structures in deposited films. This knowledge ensures that metals are processed under conditions that enhance their desired characteristics, making melting temperature a critical parameter in material science and engineering.
Key Points Explained:
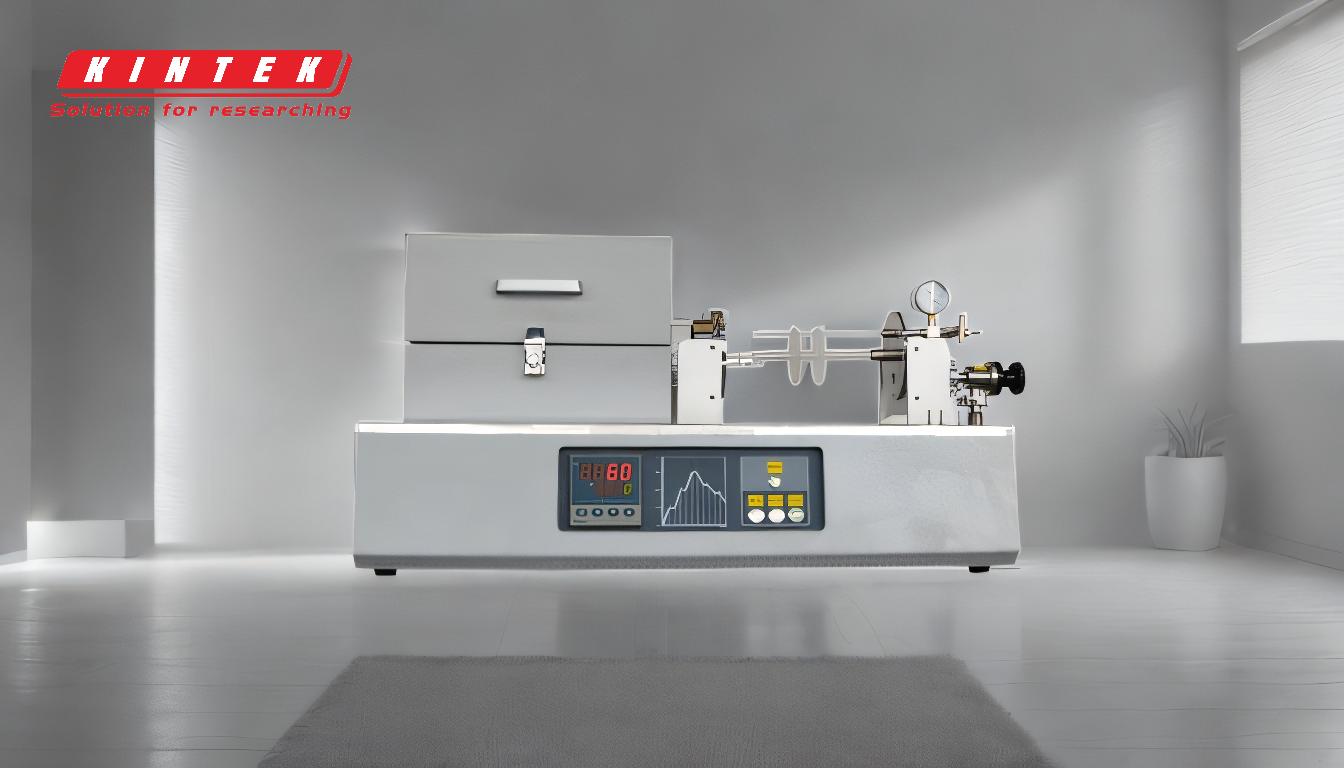
-
Impact on Metal Properties During Melting and Re-cooling:
- When metals are melted and then re-cooled, they undergo complex crystallization processes. These processes can significantly alter the metal's microstructure, which in turn affects its mechanical properties such as strength, ductility, and hardness.
- For example, rapid cooling can lead to the formation of fine-grained structures, which generally enhance strength and toughness. Conversely, slow cooling might result in larger grains, potentially reducing strength but improving ductility.
- Understanding the melting temperature is essential for controlling these crystallization processes to achieve the desired material properties.
-
Role in Manufacturing Processes:
- In manufacturing, the melting temperature of metals determines the energy requirements and the type of equipment needed for processes like casting, welding, and heat treatment.
- For instance, metals with higher melting points require more energy to melt, which can increase production costs. Therefore, selecting metals with appropriate melting temperatures is crucial for economic and efficient manufacturing.
- Additionally, precise control over the melting temperature ensures that the metal does not degrade or lose essential properties during processing.
-
Importance in PECVD Processes:
- In Plasma-Enhanced Chemical Vapor Deposition (PECVD), the melting temperature of materials, particularly electrodes, plays a vital role in the quality of the deposited films.
- Using electrodes that can operate at high temperatures allows for the use of lower plasma powers, which can reduce energy consumption and minimize damage to the substrate.
- Achieving thermal equilibrium on the surface of the electrode is crucial for creating high-quality crystal structures in the deposited films. This equilibrium is directly influenced by the melting temperature of the electrode material.
-
Thermal Management and Material Selection:
- The melting temperature is a key factor in thermal management strategies, especially in high-temperature applications. Materials with high melting points are often selected for components that must withstand extreme heat without losing structural integrity.
- For example, in aerospace and automotive industries, components exposed to high temperatures, such as turbine blades or engine parts, are made from superalloys with high melting points to ensure durability and performance.
- Understanding the melting temperature helps in selecting the right materials for specific applications, ensuring safety, reliability, and longevity.
-
Influence on Electrical and Thermal Conductivity:
- The melting temperature can also affect the electrical and thermal conductivity of metals. Metals with higher melting points often have better thermal stability, which can be advantageous in applications requiring consistent performance at elevated temperatures.
- For instance, in electronic devices, materials with high melting points are used for components like heat sinks and conductive traces to ensure efficient heat dissipation and reliable electrical performance.
In conclusion, the melting temperature of metals is a fundamental property that influences their processing, performance, and application across various industries. By understanding and controlling this parameter, engineers and scientists can optimize material properties, enhance manufacturing efficiency, and ensure the reliability of high-temperature applications.
Summary Table:
Aspect | Importance |
---|---|
Impact on Metal Properties | Alters mechanical, thermal, and electrical properties during crystallization. |
Manufacturing Processes | Determines energy requirements and equipment for casting, welding, and more. |
PECVD Processes | Ensures high-quality crystal structures and process efficiency. |
Thermal Management | Critical for selecting materials in high-temperature applications. |
Conductivity | Influences electrical and thermal stability in electronic components. |
Learn how understanding metal melting temperature can optimize your processes—contact our experts today!