In Physical Vapor Deposition (PVD), a vacuum environment is essential to ensure the proper functioning of the deposition process. The vacuum reduces the density of atoms in the chamber, allowing vaporized material to travel unimpeded to the substrate, forming high-quality thin films. It also minimizes contamination from undesirable gases, ensuring the purity and integrity of the deposited material. Additionally, the vacuum environment enables a high thermal evaporation rate and provides a controlled, repeatable process, which is critical for achieving consistent and reliable results in PVD applications.
Key Points Explained:
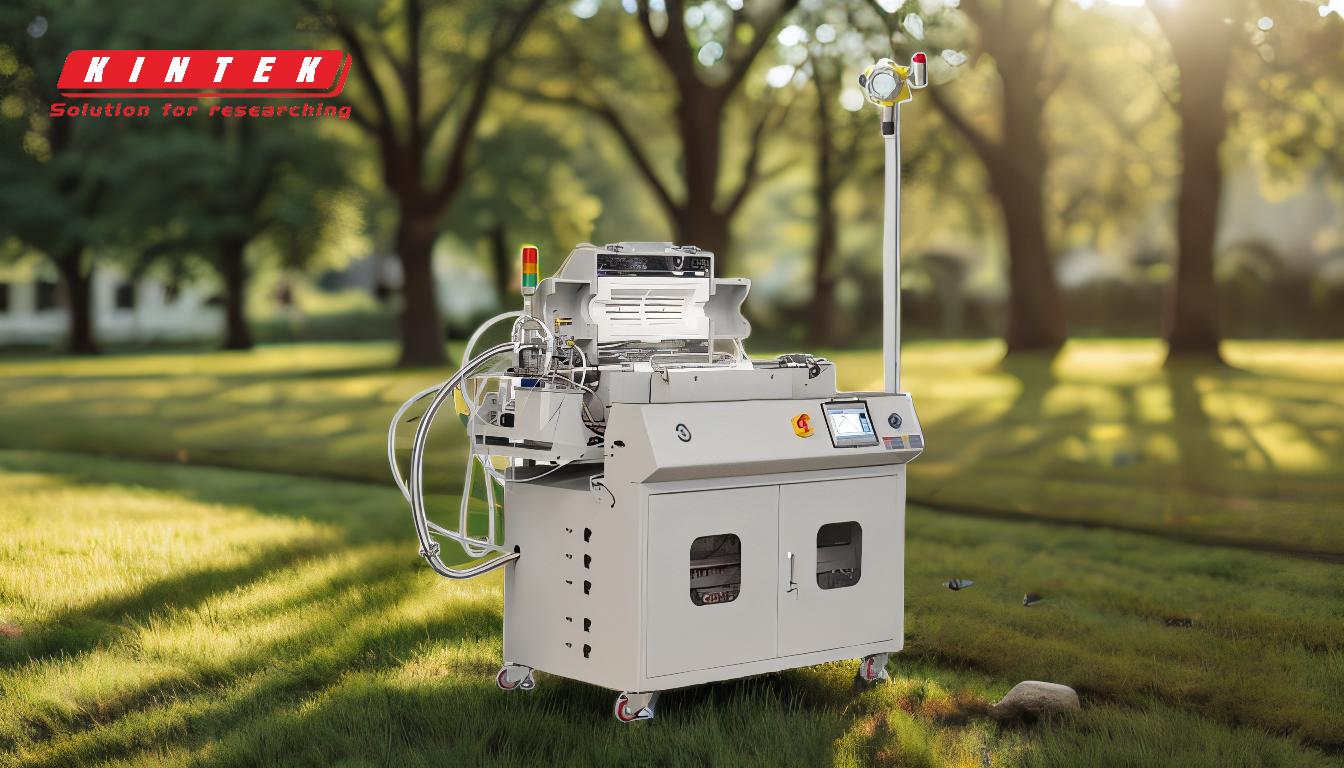
-
Lengthening the Mean Free Path of Atoms:
- In a vacuum, the density of atoms within the chamber is significantly reduced. This reduction decreases the likelihood of collisions between vaporized atoms and other particles, allowing the atoms to travel longer distances without interference. This longer mean free path ensures that the vaporized material can reach the substrate surface efficiently and uniformly, which is critical for forming high-quality thin films.
-
Minimizing Contamination:
- A vacuum environment reduces the presence of undesirable gases and particles that could contaminate the deposited material. Contaminants can adversely affect the properties of the thin film, such as its electrical conductivity, optical transparency, or mechanical strength. By maintaining a low-pressure environment (typically less than 10^-5 torr), PVD processes ensure that the deposited films are pure and free from impurities.
-
High Thermal Evaporation Rate:
- The vacuum environment facilitates a high thermal evaporation rate, which is necessary for vaporizing the target material. In the absence of air or other gases, the material can be heated to the required temperatures without oxidation or other chemical reactions that might occur in a non-vacuum environment. This allows for efficient and controlled vaporization of the target material.
-
Unimpeded Transfer of Material:
- In a vacuum, vaporized atoms can move freely toward the substrate without being slowed down by air or other fluids. This unimpeded transfer ensures that the material reaches the substrate with sufficient energy to adhere firmly, resulting in strong and durable coatings. The lack of interference from external gases also allows for precise control over the deposition process.
-
Controlled and Repeatable Process:
- A vacuum environment provides a stable and controlled atmosphere for the PVD process. This stability is crucial for achieving consistent and repeatable results, which are essential for industrial applications. By minimizing variations in pressure and contamination, the vacuum ensures that each deposition cycle produces high-quality thin films with the desired properties.
-
Preventing Nucleation in the Vapor:
- The vacuum environment prevents vaporized atoms from nucleating and forming soot or other undesirable particles in the vapor phase. By maintaining a low gas pressure, the atoms remain in their vapor state until they reach the substrate, where they can condense and form a uniform thin film. This is particularly important for achieving smooth and defect-free coatings.
-
Enhancing Adhesion and Film Quality:
- The vacuum ensures that the vaporized material reaches the substrate with sufficient energy to adhere firmly. This strong adhesion is critical for the durability and performance of the deposited film. Additionally, the controlled environment allows for the formation of films with precise thickness, composition, and microstructure, which are essential for meeting specific application requirements.
By addressing these key points, the vacuum environment in PVD processes plays a vital role in ensuring the efficiency, quality, and consistency of the deposited thin films or coatings.
Summary Table:
Key Benefits of Vacuum in PVD | Explanation |
---|---|
Lengthening Mean Free Path | Reduces atom collisions, ensuring efficient material transfer. |
Minimizing Contamination | Low-pressure environment prevents impurities, ensuring film purity. |
High Thermal Evaporation Rate | Enables efficient vaporization without oxidation or reactions. |
Unimpeded Material Transfer | Allows vaporized atoms to reach the substrate with high energy. |
Controlled and Repeatable Process | Ensures consistent and reliable deposition results. |
Preventing Nucleation in Vapor | Maintains vapor state for smooth, defect-free coatings. |
Enhancing Adhesion and Film Quality | Improves durability and precision of deposited films. |
Optimize your PVD process with a vacuum environment—contact our experts today for tailored solutions!