Refractory metals are essential in the construction of furnaces due to their unique properties, which make them ideal for high-temperature environments. These metals, such as molybdenum, tungsten, and tantalum, have high melting points, excellent wear and corrosion resistance, and low oxidation rates. These characteristics ensure that furnaces can operate efficiently and reliably at extreme temperatures without degrading or failing. Molybdenum, in particular, is widely used in vacuum furnaces due to its cost-effectiveness and superior performance. The use of refractory metals in furnace construction ensures durability, stability, and longevity, making them indispensable in industrial and high-temperature applications.
Key Points Explained:
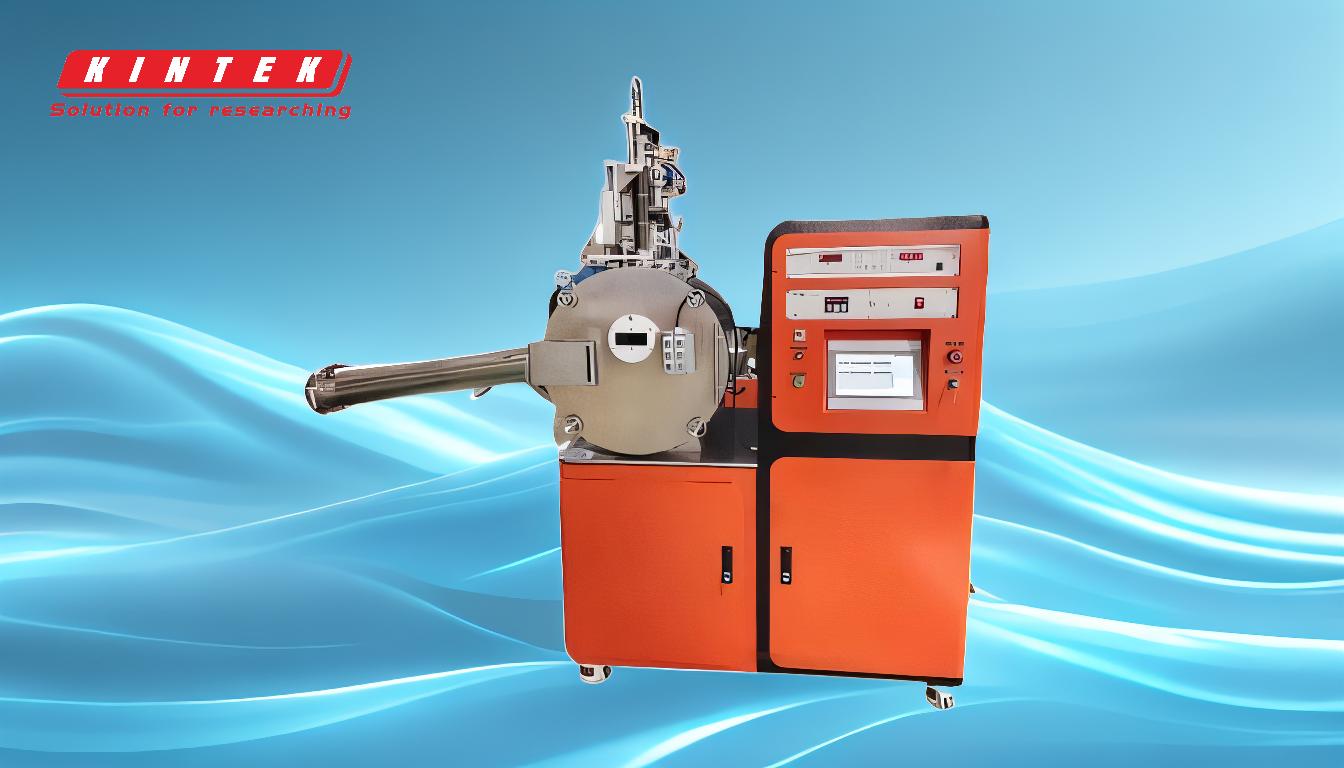
-
High Melting Point:
- Refractory metals like molybdenum, tungsten, and tantalum have exceptionally high melting points, often exceeding 2000°C. This property is crucial for furnace construction because furnaces operate at extremely high temperatures, and the materials used must withstand these conditions without melting or deforming.
- For example, tungsten has the highest melting point of all metals at 3422°C, making it ideal for the hottest parts of a furnace.
-
Wear Resistance:
- These metals exhibit high wear resistance, meaning they can endure mechanical stress and friction without significant degradation. This is particularly important in furnaces where components are subject to constant movement or contact with other materials.
- Wear resistance ensures that furnace components maintain their structural integrity over time, reducing the need for frequent replacements and maintenance.
-
Corrosion Resistance:
- Refractory metals are highly resistant to corrosion, which is vital in furnace environments where exposure to corrosive gases, chemicals, or molten materials is common. This resistance helps prevent material degradation and extends the lifespan of furnace components.
- For instance, tantalum is known for its exceptional resistance to corrosion by acids, making it suitable for furnaces used in chemical processing.
-
Slow Diffusion Rate:
- The slow diffusion rate of refractory metals means that they are less likely to react with other materials at high temperatures. This property is essential in preventing contamination of the materials being processed in the furnace and maintaining the purity of the final product.
- A slow diffusion rate also contributes to the overall stability and reliability of the furnace, as it reduces the risk of material breakdown or unwanted chemical reactions.
-
Low Oxidation Resistance:
- While refractory metals generally have low oxidation resistance, this can be mitigated through the use of protective coatings or operating the furnace in a vacuum or inert atmosphere. In such environments, the metals can perform exceptionally well without significant oxidation.
- Molybdenum, for example, is often used in vacuum furnaces where the absence of oxygen prevents oxidation, allowing it to maintain its properties at high temperatures.
-
Cost-Effectiveness of Molybdenum:
- Among refractory metals, molybdenum is particularly favored for furnace construction due to its balance of properties and cost-effectiveness. It offers a high melting point, good wear and corrosion resistance, and is more affordable than metals like tungsten or tantalum.
- The cost advantage of molybdenum makes it a practical choice for large-scale industrial furnaces, where the expense of materials can significantly impact the overall project budget.
-
Examples of Refractory Metals in Furnace Applications:
- Molybdenum (Mo): Widely used in vacuum furnaces and high-temperature heating elements due to its high melting point and cost-effectiveness.
- Tungsten (W): Employed in the hottest parts of furnaces, such as heating elements and crucibles, where extreme temperatures are required.
- Tantalum (Ta): Used in furnaces for chemical processing due to its excellent corrosion resistance.
- Niobium (Nb): Often used in specialized high-temperature applications where its unique properties are beneficial.
In conclusion, refractory metals are indispensable in furnace construction due to their ability to withstand extreme temperatures, resist wear and corrosion, and maintain stability over time. Their unique properties ensure that furnaces can operate efficiently and reliably, making them a critical component in various industrial processes.
Summary Table:
Property | Refractory Metals | Benefits for Furnaces |
---|---|---|
High Melting Point | Molybdenum, Tungsten, Tantalum | Withstand extreme temperatures (e.g., tungsten melts at 3422°C). |
Wear Resistance | All refractory metals | Maintain structural integrity under mechanical stress and friction. |
Corrosion Resistance | Tantalum, Molybdenum | Resist corrosive gases, chemicals, and molten materials. |
Slow Diffusion Rate | All refractory metals | Prevent contamination and maintain material purity in high-temperature environments. |
Low Oxidation Resistance | Molybdenum (in vacuum) | Perform well in vacuum or inert atmospheres with protective coatings. |
Cost-Effectiveness | Molybdenum | Affordable yet durable, ideal for large-scale industrial furnaces. |
Need refractory metals for your furnace project? Contact our experts today for tailored solutions!