Annealing is a critical heat treatment process used to enhance the properties of metals, making them more suitable for various applications. By heating the metal to a specific temperature, maintaining it, and then cooling it in a controlled manner, annealing softens the metal, increases its ductility, and relieves internal stresses. This process improves the metal's workability, machinability, and mechanical or electrical properties, making it less prone to cracking under pressure and easier to shape. Annealing is particularly beneficial for cold working processes, as it reduces the crystal structure dislocations in the metal, thereby reducing the risk of fracturing under stress.
Key Points Explained:
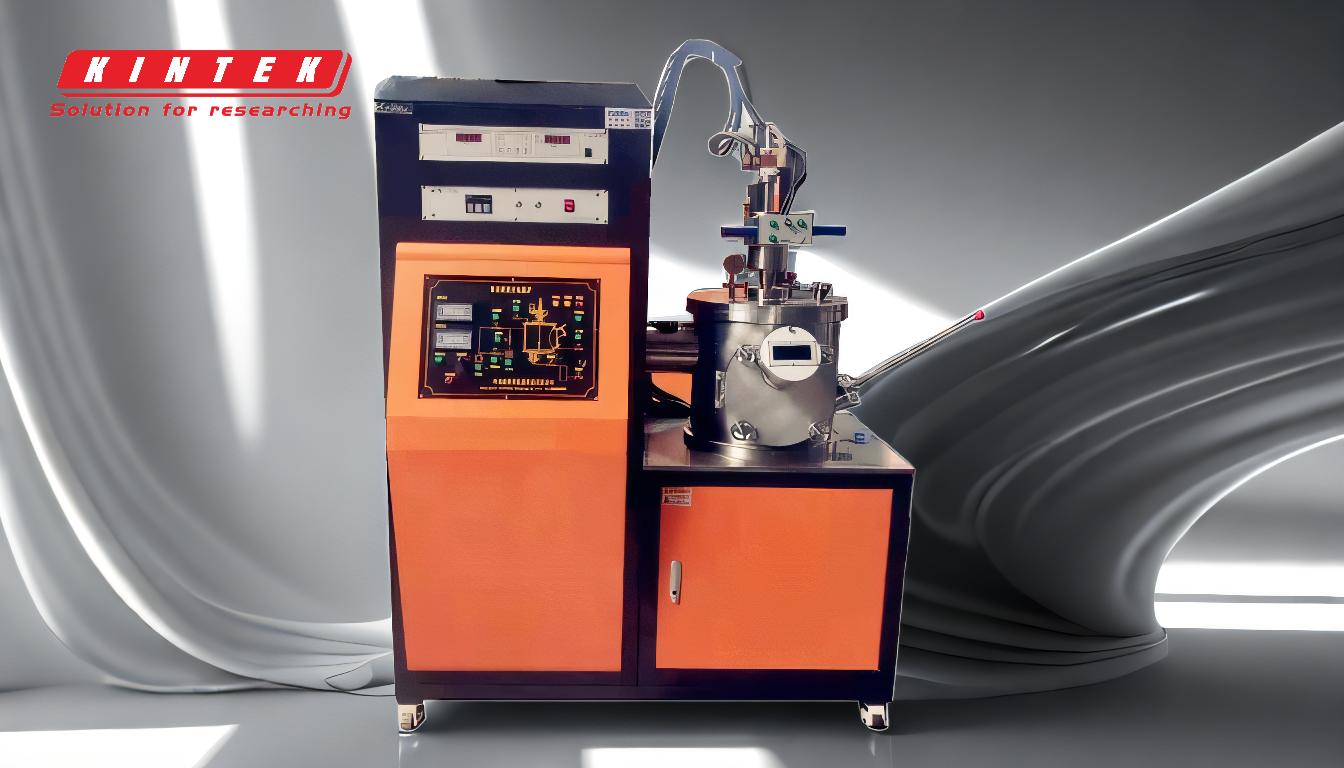
-
Softening the Metal:
- Annealing reduces the hardness of the metal, making it softer and more malleable.
- This is achieved by heating the metal to its recrystallization temperature, which allows the internal crystal structure to rearrange and reduce dislocations.
- Softer metals are easier to shape and work with, especially in processes like cold working.
-
Increasing Ductility:
- Ductility refers to the ability of a metal to deform under tensile stress without breaking.
- Annealing increases the ductility of the metal, making it more flexible and less likely to crack or fracture when subjected to mechanical stress.
- This is particularly important in manufacturing processes where the metal needs to be bent, stretched, or otherwise deformed.
-
Relieving Internal Stresses:
- Metals can develop internal stresses during manufacturing processes such as casting, welding, or machining.
- These stresses can lead to warping, cracking, or failure of the metal component.
- Annealing relieves these internal stresses by allowing the metal to relax and redistribute its internal energy, resulting in a more stable and durable material.
-
Improving Machinability:
- Machinability refers to how easily a metal can be cut, shaped, or otherwise machined.
- Annealing improves machinability by softening the metal and reducing its hardness, making it easier to cut and shape with tools.
- This is particularly beneficial in precision machining operations where tight tolerances are required.
-
Enhancing Mechanical and Electrical Properties:
- Annealing can improve the mechanical properties of a metal, such as its tensile strength, toughness, and fatigue resistance.
- It can also enhance electrical properties, such as conductivity, by reducing the number of crystal defects that can impede the flow of electrons.
- These improvements make the metal more suitable for applications where both mechanical strength and electrical performance are critical.
-
Facilitating Cold Working:
- Cold working refers to the process of shaping metal at room temperature, which can increase its strength but also make it more brittle.
- Annealing makes the metal more ductile and less brittle, allowing it to be cold worked without the risk of cracking or breaking.
- This is particularly important in industries where cold working is a common practice, such as in the production of wires, sheets, and tubes.
-
Reducing Crystal Structure Dislocations:
- Crystal dislocations are defects in the atomic structure of a metal that can lead to increased hardness and brittleness.
- Annealing reduces these dislocations, leading to a more uniform and stable crystal structure.
- This not only improves the metal's mechanical properties but also makes it more resistant to fracturing under stress.
In summary, annealing is a versatile and essential process in metalworking that enhances the properties of metals, making them more suitable for a wide range of applications. By softening the metal, increasing its ductility, relieving internal stresses, and improving its machinability and mechanical properties, annealing ensures that the metal can be effectively shaped, worked, and used in demanding environments.
Summary Table:
Key Benefits of Annealing | Description |
---|---|
Softens Metal | Reduces hardness, making it easier to shape and work with. |
Increases Ductility | Enhances flexibility, reducing the risk of cracking under stress. |
Relieves Internal Stresses | Prevents warping and cracking by redistributing internal energy. |
Improves Machinability | Makes metals easier to cut and shape, ideal for precision operations. |
Enhances Mechanical Properties | Boosts tensile strength, toughness, and fatigue resistance. |
Facilitates Cold Working | Reduces brittleness, allowing metals to be shaped at room temperature. |
Reduces Crystal Dislocations | Creates a more stable crystal structure, improving durability and performance. |
Learn how annealing can optimize your metalworking processes—contact our experts today for tailored solutions!