PVD (Physical Vapor Deposition) coatings are known for their durability and resistance to fading. The fading of PVD coatings depends on several factors, including the type of coating material, the application process, environmental conditions, and maintenance. When applied correctly, PVD coatings are highly resistant to fading and discoloration, ensuring that the finish remains bright and vibrant for many years. The lifespan of PVD coatings can range from 10 years to hundreds of years, depending on factors such as substrate type, coating thickness, and exposure to wear and environmental conditions.
Key Points Explained:
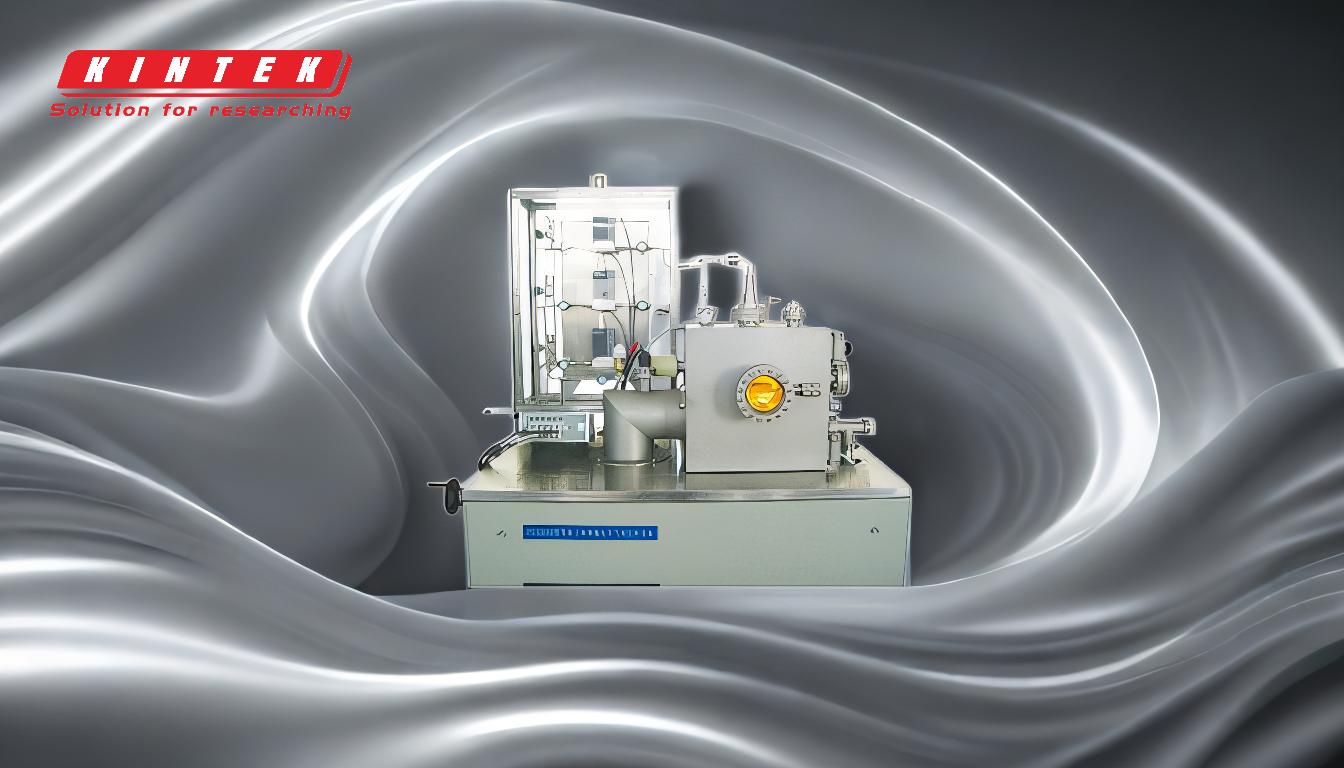
-
Resistance to Fading
- PVD coatings are specifically designed to resist fading and discoloration. This is due to their hardness and chemical stability, which make them less susceptible to environmental factors such as UV exposure, moisture, and oxidation.
- The reference states: "PVD coatings are resistant to fading and discoloration, so the finish will remain bright and vibrant for years to come." This highlights the inherent properties of PVD coatings that prevent fading over time.
-
Durability and Hardness
- PVD coatings are extremely hard, often four times harder than chrome, which contributes to their resistance to scratching and wear. This hardness also plays a role in preventing fading, as a harder surface is less likely to degrade or lose its finish.
- The reference mentions: "PVD coatings are four times harder than chrome, making them extremely hard and resistant to scratching." This hardness ensures that the coating remains intact and retains its appearance over time.
-
Factors Influencing Fading
- The longevity and resistance to fading of PVD coatings depend on several factors:
- Coating Material: Different materials used in PVD coatings (e.g., titanium nitride, zirconium nitride) have varying levels of resistance to fading.
- Coating Thickness: Thicker coatings generally provide better protection against fading.
- Adhesion to Substrate: Strong adhesion between the coating and the substrate ensures that the coating remains intact and less prone to degradation.
- Environmental Conditions: Exposure to harsh environments, such as high temperatures, UV light, or corrosive substances, can affect the coating's resistance to fading.
- The reference states: "The ability of a PVD coating to remain functional and retain its cosmetic appearance depends on several factors: coating material, coating thickness, adhesion between coating and substrate, type and hardness of the substrate, environment, and application."
- The longevity and resistance to fading of PVD coatings depend on several factors:
-
Application and Maintenance
- Proper application and maintenance are critical to ensuring that PVD coatings do not fade. For example, in the jewelry industry, PVD coatings can last up to 10 years if applied correctly and maintained properly.
- The reference highlights: "In the jewelry industry, PVD coatings can last up to 10 years if applied correctly and maintained properly. The coating enhances durability and protects against corrosion and wear." This emphasizes the importance of professional application and regular care to maintain the coating's appearance.
-
Lifespan of PVD Coatings
- The lifespan of PVD coatings varies widely, from 10 years to hundreds of years, depending on the substrate, coating thickness, and application conditions.
- The reference mentions: "PVD coating can last anywhere from 10 years to hundreds of years, depending on factors such as the substrate, coating thickness, and application conditions." This indicates that, under optimal conditions, PVD coatings can remain fade-resistant for an exceptionally long time.
-
Process and Quality Control
- The quality of the PVD coating process, including surface pretreatment, cleanliness, and operator skill, plays a significant role in determining the coating's resistance to fading.
- The reference notes: "Surface cleanliness is vital as even small particles can affect the result; and tightly sealed tapped holes should be avoided to prevent trapped air from affecting the coating quality." This underscores the importance of meticulous preparation and execution in the PVD coating process.
-
Environmental and Application-Specific Considerations
- PVD coatings are used in a variety of applications, from industrial tools to decorative finishes. The specific application and environment in which the coating is used will influence its resistance to fading. For example, coatings used in outdoor environments with high UV exposure may require additional protective measures to maintain their appearance.
- The reference states: "The properties of PVD coatings are influenced by the type of coating and the process used to create it. Even if coatings are made from the same material or look similar, the method of deposition strongly impacts their performance and properties in specific applications." This highlights the need to tailor PVD coatings to their intended use to maximize their fade resistance.
In conclusion, PVD coatings are highly resistant to fading when applied correctly and maintained properly. Their durability, hardness, and resistance to environmental factors make them an excellent choice for applications where long-lasting appearance and performance are essential. By considering factors such as coating material, thickness, adhesion, and environmental conditions, users can ensure that PVD coatings remain vibrant and functional for many years.
Summary Table:
Key Factors | Description |
---|---|
Resistance to Fading | PVD coatings resist fading due to hardness and chemical stability. |
Durability | 4x harder than chrome, ensuring scratch and wear resistance. |
Lifespan | 10 years to hundreds, depending on substrate, thickness, and conditions. |
Application | Proper application and maintenance are critical for long-lasting performance. |
Environmental Factors | UV exposure, moisture, and corrosive substances can impact fade resistance. |
Ensure your PVD coatings stay vibrant for years—contact our experts today for tailored solutions!