Understanding Cold Isostatic Pressing Services
Table of Contents
- Understanding Cold Isostatic Pressing Services
- Variety and Specializations in Cold Isostatic Pressing Services
- Design and fabrication capabilities: molds, mandrels, bags, tooling, and fixtures
- Specializations in decanning or chemical milling operations
- Utilization of cold isostatic pressing for densification or porosity removal
- Production of graded compositions and transition joints
- Net or near-net shape fabrication
- Additional Services Offered by Cold Isostatic Pressing Service Providers
- Material Capabilities in Cold Isostatic Pressing Services
The application of high pressures in cold isostatic pressing services
Cold isostatic pressing (CIP) services utilize extremely high pressures to sterilize products or cold compact powders. This technology is widely used in industries such as aerospace, automotive, electronics, and more. CIP is particularly effective in producing complex shapes and increasing the final density of materials. It can be used with a variety of materials and components, including aluminum and magnesium alloys, carbides and cutting tools, carbon and graphite, ceramics, composites, coatings, thermal spray deposits, copper alloys, diamond-like materials, electronic or electrical materials, explosives or pyrotechnics, and specialty and proprietary materials.
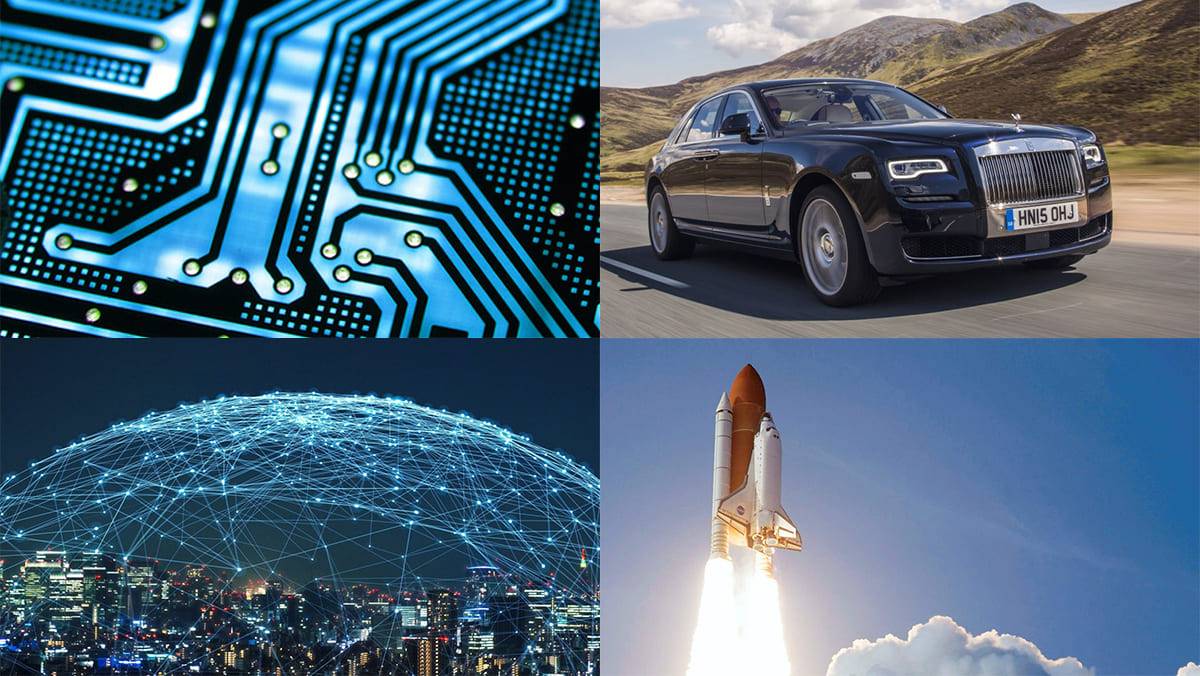
Supplier specifications: service capabilities, materials processed, regions served
When selecting a cold isostatic pressing service, it is crucial to consider the supplier's specifications. These specifications include the service capabilities, materials processed, and regions served. Some suppliers specialize in specific materials or components, while others offer a broader range of services. It is important to choose a supplier that aligns with your specific requirements to ensure the best results.
Importance of pressure range and capacity
Pressure range and capacity are vital parameters to consider when specifying cold isostatic pressing services. The maximum operating pressure required to achieve the desired density during part production varies depending on the material and part geometry. The capacity or chamber size of the cold isostatic pressing equipment is determined by the chamber's internal diameter and length. The chamber's dimensions determine the maximum diameter and width of the parts that can be produced.
The role of maximum operating pressure and chamber size in part production
The maximum operating pressure and chamber size play a crucial role in the production of parts using cold isostatic pressing. The high pressures applied during the process ensure the desired density and structural integrity of the parts. The chamber size determines the dimensions of the parts that can be produced, allowing for customization and flexibility in manufacturing.
In conclusion, cold isostatic pressing services offer a wide range of capabilities and applications. By understanding the importance of pressure range, capacity, and supplier specifications, businesses can make informed decisions when selecting a cold isostatic pressing service provider. This technology provides an efficient and effective solution for various industries, ensuring high-quality and reliable products.
Variety and Specializations in Cold Isostatic Pressing Services
Design and fabrication capabilities: molds, mandrels, bags, tooling, and fixtures
Cold isostatic pressing services offer a range of design and fabrication capabilities. These services can design and fabricate various components such as molds, mandrels, bags, tooling, and fixtures. This allows for the production of complex shapes and structures using cold isostatic pressing technology.
Specializations in decanning or chemical milling operations
Some cold isostatic pressing services specialize in decanning or chemical milling operations. Decanning refers to the removal of a can or mold from a part after cold isostatic pressing. Chemical milling operations involve the use of chemicals to selectively remove material from a part. These specialized services provide additional options for shaping and refining parts produced through cold isostatic pressing.
Utilization of cold isostatic pressing for densification or porosity removal
Cold isostatic pressing services use this technology for various purposes, including densification or porosity removal. Cold isostatic pressing can be used to densify or close porosity within a powder body, sinter part, joint, or casting. This process ensures the production of high-quality, dense parts with minimal porosity.
Production of graded compositions and transition joints
Another specialization in cold isostatic pressing services is the production of graded compositions and transition joints. By varying the alloy composition as a can or mold is filled with powders, these services can create parts with graded compositions. Transition joints, which connect different materials or components, can also be produced using cold isostatic pressing.
Net or near-net shape fabrication
Cold isostatic pressing services also offer net or near-net shape fabrication. Near-net shaping requires less material for part shaping compared to machining from stock forms. This results in cost savings and reduced material waste. Cold isostatic pressing services can produce parts that closely resemble the final desired shape, minimizing the need for additional machining.
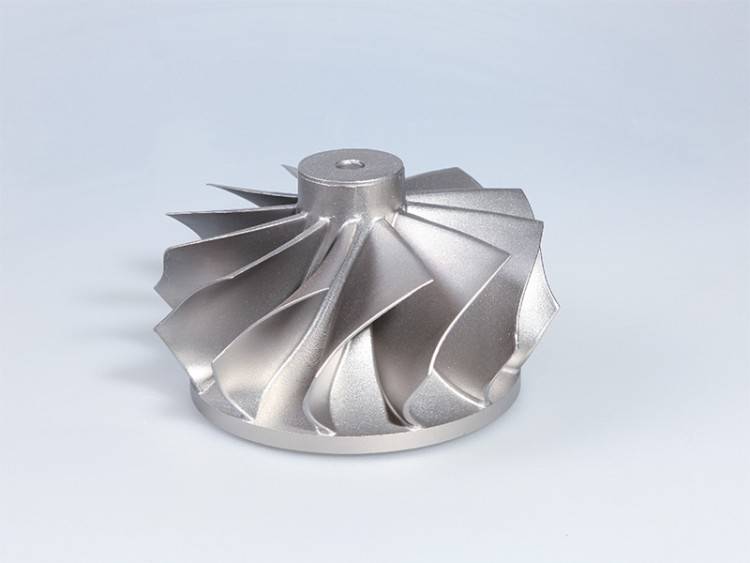
In summary, cold isostatic pressing services provide a variety of capabilities and specializations. These services offer design and fabrication capabilities, specialize in decanning or chemical milling operations, utilize cold isostatic pressing for densification or porosity removal, produce graded compositions and transition joints, and offer net or near-net shape fabrication. By leveraging these services, businesses can benefit from the efficiency, precision, and versatility of cold isostatic pressing technology.
Additional Services Offered by Cold Isostatic Pressing Service Providers
Cold isostatic pressing services provide a range of additional services to meet the diverse needs of their customers. These services include:
Powder consolidation, preparation or blending services
Cold isostatic presses can be used to consolidate powders and increase their final density. This process is especially useful for producing complex shapes or achieving higher density levels. Additionally, these presses can blend and prepare powders for further processing, ensuring optimal powder characteristics for desired outcomes.
Laboratory or developmental services
Some cold isostatic pressing service providers offer laboratory or developmental services. These services may include conducting process parameter studies or producing powder samples for testing and analysis. This allows businesses to refine their processes and optimize their products before moving to full-scale production.
Production processing services
Cold isostatic pressing service providers also offer production processing services. These facilities are equipped to handle large-scale production runs, ensuring efficient and precise manufacturing of parts and components. With their expertise and specialized equipment, these providers can meet the production demands of various industries.
Piggybacking services for small batch processing
In addition to their primary production runs, some cold isostatic pressing service providers offer piggybacking services. This means they utilize the excess space within their current production runs to process small batches. This allows businesses with smaller production needs to take advantage of the cost-effective benefits of cold isostatic pressing without needing to meet large minimum order quantities.
These additional services offered by cold isostatic pressing service providers expand the capabilities and flexibility of businesses in various industries. Whether it's powder consolidation, laboratory testing, large-scale production, or accommodating small batch processing, these services cater to the specific needs of each customer.
Material Capabilities in Cold Isostatic Pressing Services
Cold isostatic pressing services offer a range of material capabilities to meet various manufacturing needs. These capabilities include the use of different materials and components, as well as specialization in specific materials or applications.
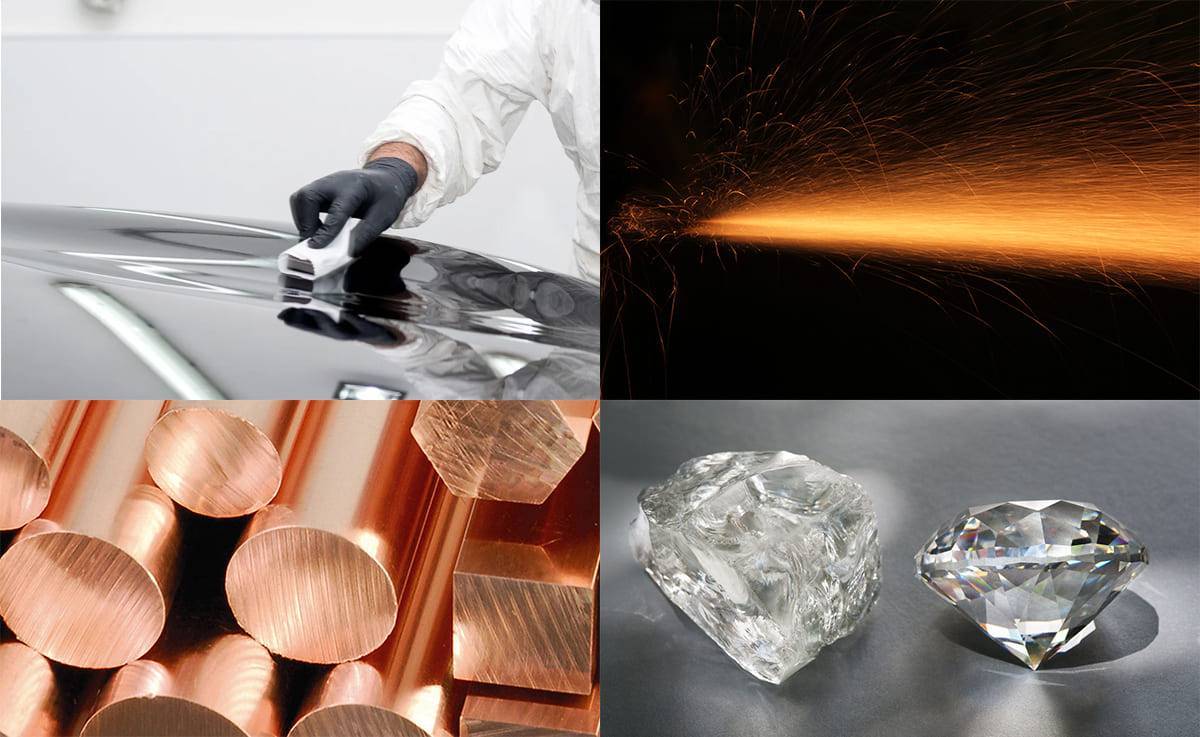
Use of Various Materials
Cold isostatic pressing services can work with a wide range of materials and components. Some of the common materials used in this process include:
-
Aluminum and magnesium alloys: These materials are widely used in industries such as automotive and aerospace due to their lightweight and high strength properties.
-
Carbides and cutting tools: Cold isostatic pressing can be used to produce carbide tools, which are known for their hardness and wear resistance.
-
Carbon and graphite: Cold isostatic pressing is often used to consolidate graphite powders, which are commonly used in applications such as electrodes and crucibles.
-
Ceramics: Cold isostatic pressing is an effective method for consolidating ceramic powders, allowing for the production of advanced ceramic components used in various industries.
-
Composites: Cold isostatic pressing can be used to produce composite materials by consolidating different types of powders or fibers.
Specialization in Specific Materials or Applications
Some cold isostatic pressing services specialize in specific materials or applications. For example:
-
Coatings and thermal spray deposits: Some services have expertise in applying coatings and thermal spray deposits using cold isostatic pressing. This is useful in industries such as aerospace and automotive, where coatings are applied to improve wear resistance and performance.
-
Copper alloys: Cold isostatic pressing can be used to produce components made from copper alloys, which are known for their excellent electrical conductivity.
-
Diamond and diamond-like materials: Cold isostatic pressing can be used to produce components made from diamond or diamond-like materials, which have exceptional hardness and wear resistance.
-
Electronic or electrical materials: Some services have experience working with electronic or electrical materials, which require special handling and processing.
-
Explosives or pyrotechnics: Cold isostatic pressing can be used in the production of components for explosive or pyrotechnic applications.
-
Specialty and proprietary materials: Cold isostatic pressing services may also have expertise in working with specialty and proprietary materials, which may have unique properties or requirements.
In conclusion, when selecting cold isostatic pressing services, it is important to consider the material capabilities offered by the service provider. Whether it is working with specific materials or specializing in certain applications, the material capabilities of the service provider can greatly impact the success of your manufacturing project.
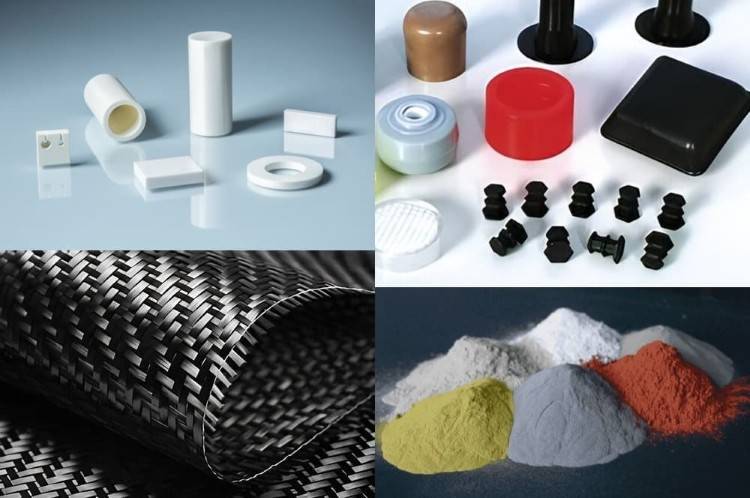
If you are interested in this product you can browse our company website:https://kindle-tech.com/thematics/lab-hydraulic-press, we always insist on the principle of quality first. During the production process, we strictly control every step of the process, using high quality materials and advanced production technology to ensure the stability and durability of our products. to ensure that their performance meets the highest standards. We believe that only by providing customers with excellent quality can we win their trust and long-term cooperation.
CONTACT US FOR A FREE CONSULTATION
KINTEK LAB SOLUTION's products and services have been recognized by customers around the world. Our staff will be happy to assist with any inquiry you might have. Contact us for a free consultation and talk to a product specialist to find the most suitable solution for your application needs!