Overview of Cold Isostatic Pressing
Table of Contents
- Overview of Cold Isostatic Pressing
- Cold Isostatic Pressing in Tool Manufacturing
- Cold Isostatic Pressing in Rare Metal Powders Production
- Cold Isostatic Pressing and Extrusion
- Commercial usage of CIP and extrusion to produce extruded AlBeMet rod and bar
- Process of encapsulating, degassing, and preheating the billet
- Extrusion process using a taper die
- Post-extrusion processes including chemical etching and removal of copper skin
- Annealing process of extruded aluminum-beryllium alloys
Cold Isostatic Pressing (CIP) is a powerful technique used in materials processing to enhance material properties. It involves subjecting a material to uniform pressure from all sides by immersing it in a high-pressure fluid medium and applying hydraulic pressure. CIP is particularly effective for shaping and consolidating powdered materials, creating intricate shapes, and achieving high green density.
Definition and commonality of cold isostatic pressing (CIP)
Cold Isostatic Pressing, also known as cold isostatic compaction, is a compaction process for powders confined in an elastomer mold. The mold is placed in a pressure chamber, and a liquid medium is pumped in, subjecting the mold to high pressure from all sides. CIP is utilized with various materials such as powdered metallurgy, cemented carbides, refractory materials, graphite, ceramics, plastics, and more.
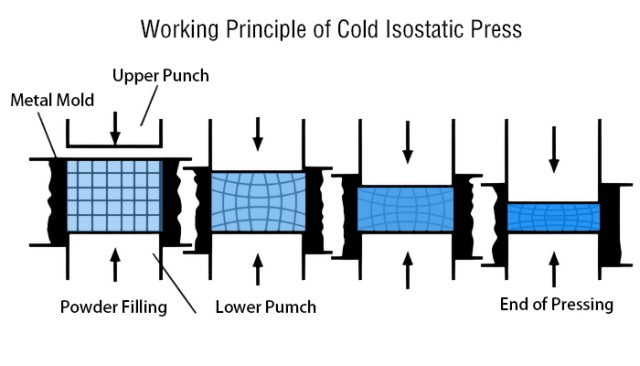
Usage of wetbag and drybag techniques for CIP
There are two common techniques used in CIP: wetbag and drybag. In the wetbag process, the powder material is enclosed in a flexible mold bag, which is submerged into a high-pressure liquid in a pressure vessel. Isostatic pressure is then applied to compress the powder into a desired shape. This process is ideal for multi-shape production, small to large quantity production, and the pressing of large products.
On the other hand, drybag pressing is used for simple shapes. The powder-filled mold is sealed, and the compression occurs between the mold and the pressure vessel. This technique is suitable for producing components with less complexity.
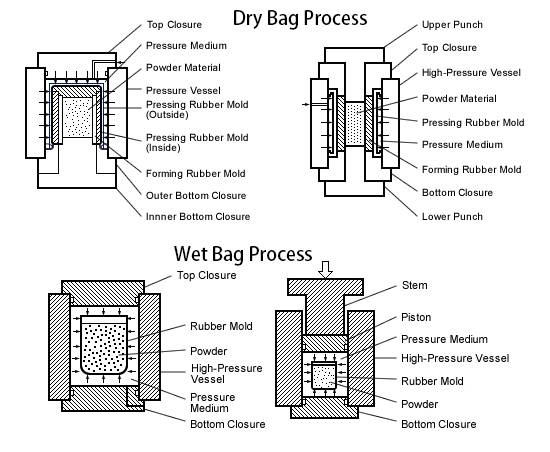
Production of complex components and tungsten ingots using CIP
CIP is widely used in the production of complex components and tungsten ingots. With the wetbag technique, it is possible to press tungsten ingots weighing up to 1 ton. Additionally, CIP allows for the compaction of more complex components, thanks to its ability to create intricate shapes and achieve high green density.
In summary, Cold Isostatic Pressing (CIP) is a versatile technique for shaping and consolidating powdered materials. It offers advantages such as the ability to produce complex components, create intricate shapes, and achieve high green density. The choice between wetbag and drybag techniques depends on the specific requirements of the project.
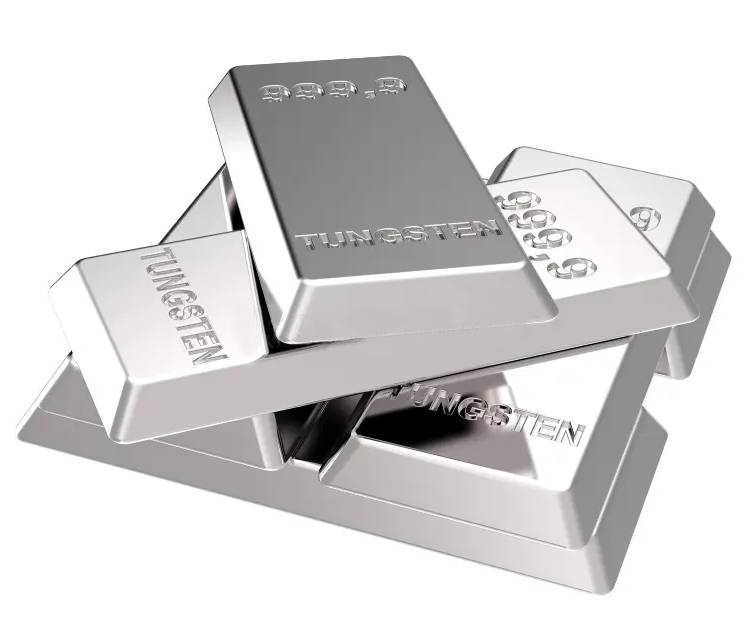
Cold Isostatic Pressing in Tool Manufacturing
Cold isostatic pressing (CIP) is a method used in tool manufacturing to compact powdered materials into a solid homogeneous mass before machining or sintering. It is commonly used for producing wear and metal forming tools. CIP involves subjecting the powder to equal pressure from all directions, resulting in high-integrity billets or preforms with little distortion or cracking when fired.
Application of CIP for producing wear and metal forming tools
CIP is widely used in the production of wear and metal forming tools. It is particularly suitable for parts that are too large to be pressed in uniaxial presses and do not require high precision in the sintered state. CIP can produce high-integrity billets or preforms with minimal distortion or cracking.
Use of dry-bag and wet-bag CIP presses
There are two types of CIP processes: dry-bag and wet-bag. In the dry-bag process, the powder is placed in an impervious moldable bag inside a pressure chamber. The bag is then subjected to an isostatic pressure using a water-based liquid medium at ambient temperature. This process is automated and allows for high-volume production of relatively simple shapes.
On the other hand, the wet-bag process involves submerging the powder material in a flex mold bag into a high-pressure liquid in a pressure vessel. Isostatic pressure is then applied to compress the powder into the desired shape. This process is ideal for multi-shape and small to large quantity production, including the pressing of large products.
Process of CIP involving water-based liquid medium at ambient temperature
In CIP, the powder material is placed in an impervious moldable bag inside a pressure chamber. The bag is filled with a water-based liquid medium, and the entire mold is uniformly subjected to high pressure from all sides. The pressure is applied using a water-based liquid medium at ambient temperature. This process allows for the compaction of the powder material into a solid homogeneous mass.
Usage of shaped bags with cores and powders with no or low wax
To obtain near-net shapes, shaped bags with cores are used in the CIP process. These shaped bags help in achieving the desired shape and dimensional tolerances of the final product. Additionally, powders with no or low wax content are used in cold isostatic pressing. This ensures that the powder material can be easily compacted into a solid mass without the need for excessive heat or pressure.
Dimensional tolerances of parts produced by CIP
The dimensional tolerances of parts produced by CIP are relatively large compared to uniaxial pressing. This means that size and shape control are not as critical in the CIP process. However, parts produced by CIP still require machining in the green, or presintered, state, followed by sintering to achieve the final dimensions and properties.
Overall, cold isostatic pressing is a versatile method used in tool manufacturing for producing wear and metal forming tools. It offers advantages such as high-integrity billets or preforms, minimal distortion or cracking, and the ability to produce near-net shapes. CIP is a cost-effective and efficient process that can be used for high-volume production of complex shapes in various industries.
Cold Isostatic Pressing in Rare Metal Powders Production
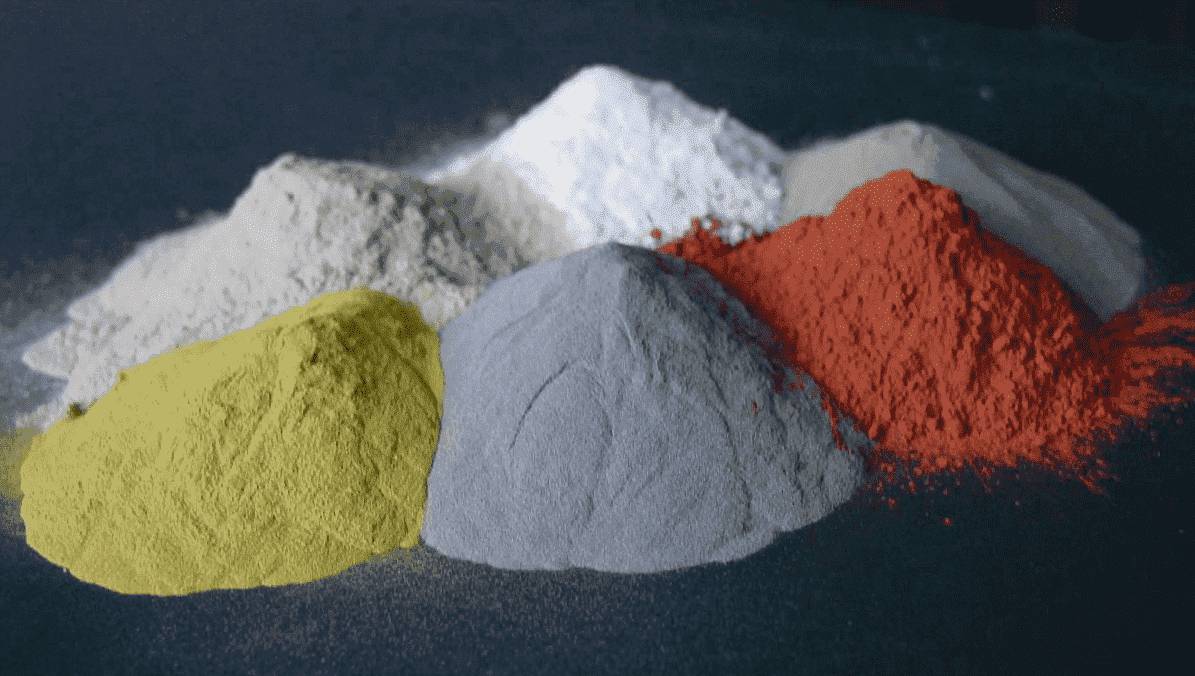
Cold isostatic pressing is a technique used in the production of rare metal powders. It involves applying pressure to the powder at room temperature or slightly higher, typically below 93°C. The pressure applied ranges from 100-600 MPa.
The purpose of cold isostatic pressing is to obtain a "raw" part with sufficient strength for handling, processing, and eventual sintering to achieve final strength. This technique utilizes a liquid medium, such as water, oil, or a glycol mixture.
When it comes to metals, cold isostatic pressing can achieve a theoretical density of about 100%. For ceramic powders, the density achieved is approximately 95%. Cold isostatic pressing is particularly useful in forming powdered materials at room temperature using rubber or plastic as the encasing mold material and liquid as the pressure medium.
One of the advantages of cold isostatic pressing is that it eliminates the need for expensive pressing dies, making it a cost-effective option. It is especially beneficial when producing large or complex compacts where the high initial cost of pressing dies cannot be justified.
This technique can be employed on a commercial scale for various types of powders, including metals, ceramics, plastics, and composites. The required pressures for compacting range from less than 5,000 psi to over 100,000 psi (34.5 to 690 MPa).
Powders are compacted in elastomeric molds using either a wet or dry bag process. Cold isostatic pressing provides a means of producing high-quality parts that can undergo further sintering or hot isostatic pressing processes.
Cold Isostatic Pressing and Extrusion
Commercial usage of CIP and extrusion to produce extruded AlBeMet rod and bar
Cold isostatic pressing (CIP) is widely used in commercial applications to produce extruded AlBeMet rod and bar. This process involves the preliminary densification of unsintered or green dye-compacted metal powder components before further processing such as rolling, machining, or sintering. CIP systems are used in various industries, including aerospace, military, industrial, and medical, to create flawless components with sufficient green strength for handling and sintering.
Process of encapsulating, degassing, and preheating the billet
The process of cold isostatic pressing begins with encapsulating the metal powder in an elastomeric mold made of materials such as urethane, rubber, or polyvinyl chloride. The encapsulated powder is then subjected to fluid pressure, typically using oil or water, ranging from 60,000 lbs/in2 to 150,000 lbs/in2. This pressure helps in compacting the powder uniformly, resulting in a green compact with low geometric accuracy but high density. The green compact is then preheated to prepare it for further processing.
Extrusion process using a taper die
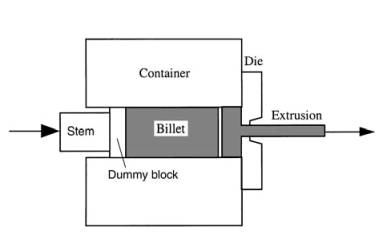
After the billet is preheated, it undergoes the extrusion process using a taper die. The taper die helps in shaping the extruded AlBeMet rod or bar according to the desired dimensions. The extrusion process involves applying high pressure to force the billet through the taper die, resulting in the formation of a continuous extruded product. This process ensures the uniformity and consistency of the extruded AlBeMet rod or bar.
Post-extrusion processes including chemical etching and removal of copper skin
Once the extrusion process is complete, post-extrusion processes are carried out to refine the extruded product. These processes include chemical etching and the removal of the copper skin. Chemical etching helps in removing any surface impurities or defects, ensuring the quality of the extruded AlBeMet rod or bar. The removal of the copper skin is necessary as it is typically present on the surface of the extruded product due to the use of copper alloys in the extrusion process.
Annealing process of extruded aluminum-beryllium alloys
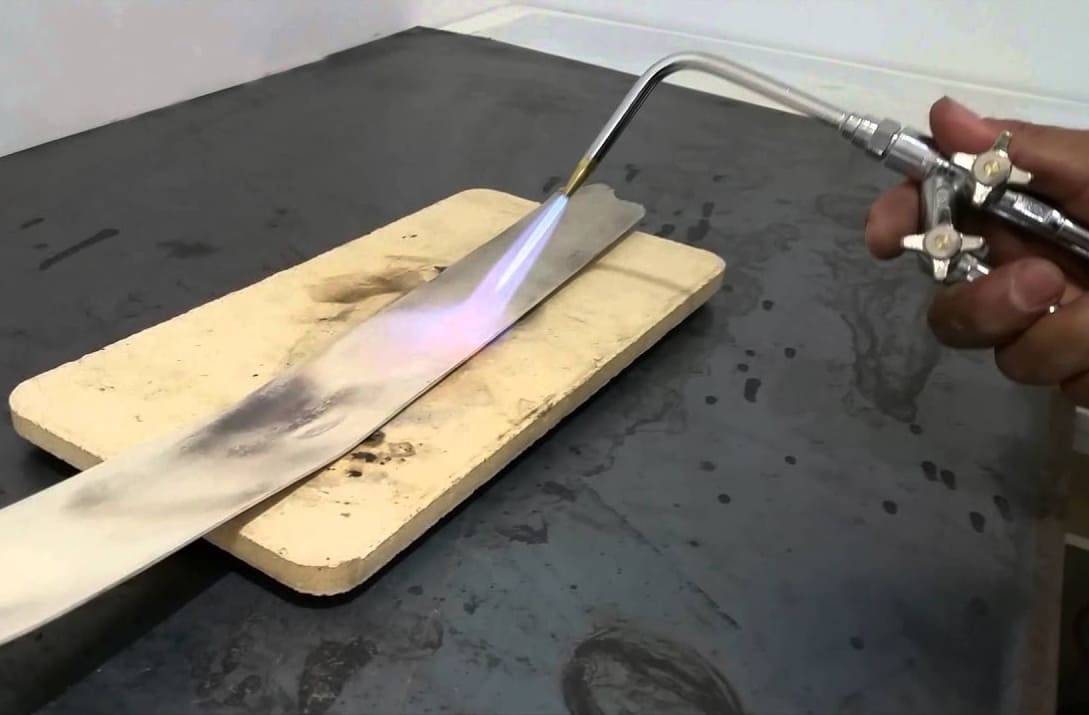
After the post-extrusion processes, the extruded aluminum-beryllium (AlBeMet) alloys undergo an annealing process. Annealing involves heating the extruded product to a specific temperature and then slowly cooling it to relieve internal stresses and improve its mechanical properties. This process helps in enhancing the strength, ductility, and stability of the extruded AlBeMet rod or bar.
Overall, cold isostatic pressing and extrusion play a crucial role in the commercial production of extruded AlBeMet rod and bar. The combination of these processes ensures the production of high-quality components with precise dimensions and excellent mechanical properties.
CONTACT US FOR A FREE CONSULTATION
KINTEK LAB SOLUTION's products and services have been recognized by customers around the world. Our staff will be happy to assist with any inquiry you might have. Contact us for a free consultation and talk to a product specialist to find the most suitable solution for your application needs!