Introduction
Table of Contents
- Introduction
- Key Features of the Laboratory Press
- Automatic Press Control
- PLC controller with Touch Screen Display
- Free definition of the moulding cycle
- Storage capacity for three moulding cycles
- Cooling system
- Key features & benefits of Process Controller:
- KinTek Press Logger
- Standard Calibration service for Laboratory Press
- Automatic Hydraulic Press
- Hydraulic Mini Press
- Process Control
- CNC Automation
- Plastic Deformation
- Hydraulic Press
- Cooling System
- Closure Force Control
- Moulds
- KinTek Press Logger
- Standard Calibration Service for Laboratory Press
- Conclusion
In the world of laboratory research and testing, having a reliable and efficient laboratory press is crucial. Whether you're working with materials testing, sample preparation, or quality control, a laboratory press can greatly enhance your workflow. But what exactly is a laboratory press and what key features should you look for? In this comprehensive analysis, we will delve into the world of laboratory presses, exploring their mechanical structures, hydraulic systems, platen surfaces, safety features, and more. So, let's get started and discover the essential components that make a laboratory press a valuable asset in any laboratory setting.
Key Features of the Laboratory Press
Laboratory presses are essential tools in various industries like pharmaceuticals, laminating, rubber and plastic molding, and R&D work. They offer precision and durability, making them ideal for meeting rigorous demands and providing consistent results.
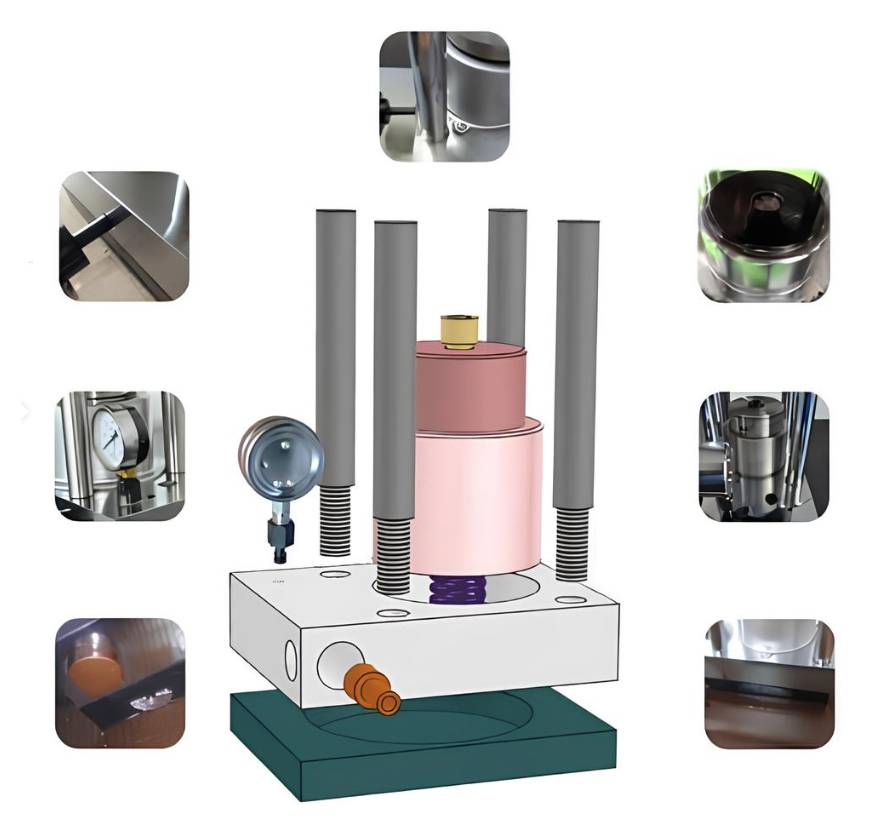
Mechanical structure with 4 columns and sliding platen
The laboratory press is built with a mechanical structure that consists of four columns and a sliding platen. This design ensures stability and allows for easy handling of different sample types and materials.
Hydraulic system with 25 tons closure force
Equipped with a hydraulic system, the laboratory press delivers a closure force of 25 tons. This force is crucial for testing and compacting materials such as rubber, plastic, and laminate materials.
250x250 mm chrome plated steel platens
The laboratory press features chrome plated steel platens with dimensions of 250x250 mm. These platens provide a sturdy and reliable surface for pressing and ensure consistent results.
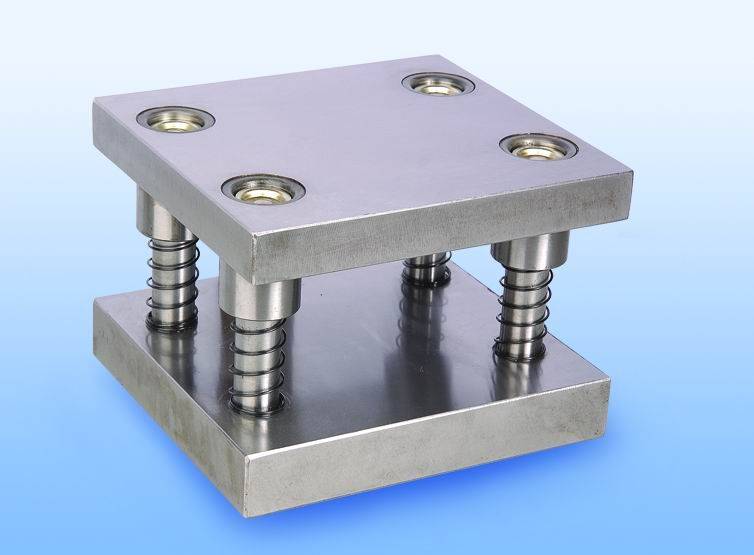
Uniform temperature distribution over the platen surface
To ensure accurate and reliable results, the laboratory press is designed with specifically designed flat heating elements that ensure uniform temperature distribution over the platen surface. This feature is crucial for materials like thermoplastic resins, composites, and ceramics.
Protection doors with safety lock
Safety is a top priority in laboratory environments, and the laboratory press addresses this with protection doors equipped with a safety lock. This ensures the safety of the operator and prevents any accidents during the pressing process.
CE Labelling
The laboratory press is CE labelled, indicating that it meets the essential health, safety, and environmental protection requirements of the European Union. This certification ensures that the press meets high standards of quality and safety.
Laboratory presses are versatile tools that find applications in various industries and research settings. They provide precise and reliable results, making them indispensable in material science labs, R&D work, testing, and production runs. With their key features, laboratory presses offer the necessary precision and durability for demanding industrial inquiries.
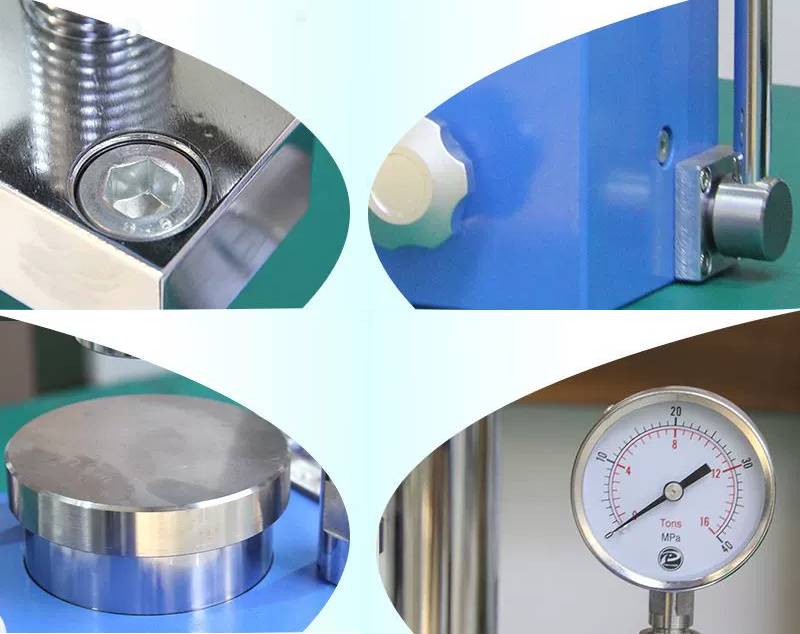
Automatic Press Control
PLC controller with Touch Screen Display
An operator interface is provided through an LCD touch-screen mounted in a control panel. An extensive range of standard displays is available. Often the operator will program and monitor furnace operation from the unit while the operation is supervised from a remote location during the cycle.
Each load has its own unique and often preprogrammed recipe to control such process variables as ramp rates (heating & cooling), preheat temperatures and times, final process temperature and time, ultimate vacuum level, partial pressure setpoints and quench gas pressure to name a few.
Free definition of the moulding cycle
The PLC controller for the press is provided with a user-friendly Touch Screen Display and permits the free definition of the moulding cycle by setting:
- The displacements of the moving platen of the press
- The thermal cycle (different temperatures of the platens and thermal gradients can be set within a moulding cycle)
- The pressure cycle (with the force control option installed).
Storage capacity for three moulding cycles
Three Moulding cycles can be stored. Each cycle includes 24 moulding steps (including displacements, temperatures setups, and pressure setups)
Cooling system
The cooling of the press platens during the molding cycle is necessary for the molding of thermoplastic materials because the material must be cooled to the solidification temperature before opening the mold.
Automatic hydraulic presses are often used for industrial XRF applications and other laboratory sample manipulation activities. However, their versatility makes them suitable for small and large-scale manufacturing practices, too – including hot embossing, laminating, and melting polymers for thin films.
Key features & benefits of Process Controller:
- Mechanical structure with 4 columns (with 60 mm diameter) and sliding platen driven by self-lubricating bushings
- Hydraulic system with 25 tons closure force
- 250x250 mm chrome plated steel platens with 40 mm thickness
- Specifically designed flat heating elements to ensure uniform temperature distribution over the platen surface
- Closed moulding area for easy fume aspiration
- Protection doors with safety lock
- CE Labelling
KinTek Press Logger
The Automatic Press Control device is fitted with a USB port which permits the connection to a Pc. The Gibitre Press Logger program permits the continuous recording of the press conditions (temperature, pressure, moving platen position, cycle step). Both graphical and numerical recording is provided with automatic generation of daily storage files. The program is compatible with Windows 10 and 11.
Standard Calibration service for Laboratory Press
Maintenance and Calibration service for your Laboratory Press.
The service includes:
- Ordinary maintenance of the instrument
- Calibration of the temperature of the platens. The temperature is measured, with the plates closed, in 9 different points of the platens and at 3 different temperatures (140°C, 170°C, 200°C).
- Calibration of the closure Force (50, 100, 150, 250 kN)
Automatic Hydraulic Press
An automatic hydraulic press works by using a pump to elevate a piston, which holds air or liquid pressure. This allows for incredibly precise application of force when the piston’s pressure is released and directed into whatever is below it.
Unlike a manual press, the piston is controlled by a switch or automated controller. This means they can be controlled to a high accuracy and repeatability; the pressure will be the same every time.
Automatic hydraulic presses, such as the APEX 400, improve the workflow in busy laboratories, as – once the press is programmed – it can operate autonomously, allowing the technician to get to work on other tasks. Not only are they far less laborious to operate than a manual counterpart, but they’re more accurate and consistent, due to the lack of variable factors during use.
Hydraulic Mini Press
A hydraulic mini press is a small, portable press that uses hydraulic power to produce force.
It works by using pressure generated by a pump to move an oil-filled plunger, which in turn compresses fluids or gases to exert force on an object. Pressure is regulated by the system’s valves, which can be adjusted according to the requirements of the task at hand.
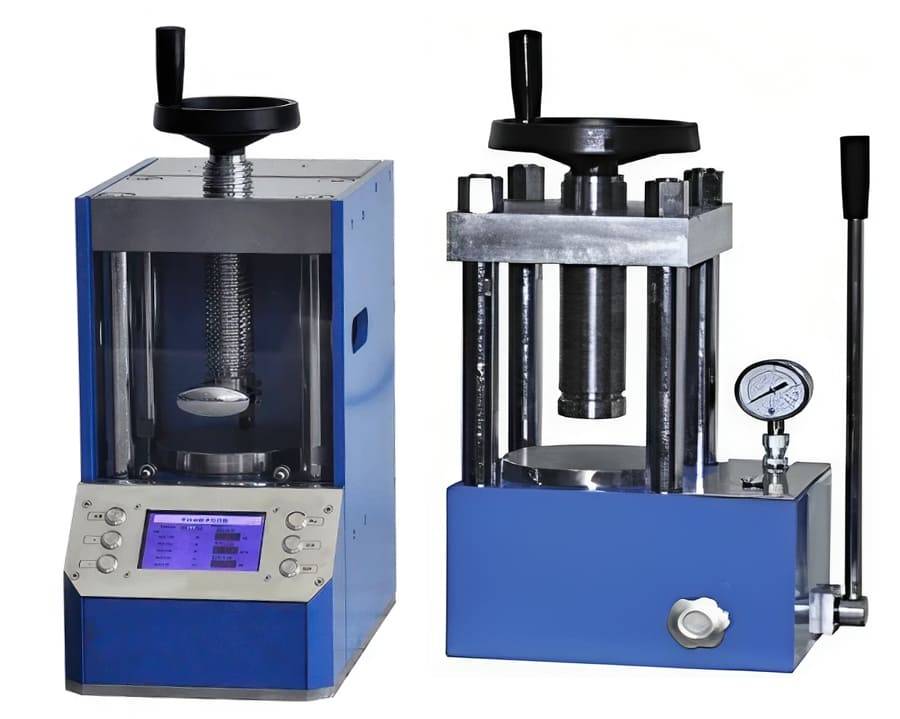
Process Control
The speed, travel distance, and pressure of a press forging die are automatically controlled for accuracy and efficiency.
CNC Automation
The forging press process has the same options as any other manufacturing method and can use CNC programming to enter designs, which can include blank feeding and forged piece removal.
Plastic Deformation
Plastic deformation goes deep into the workpiece, creating a uniform deformation throughout the metal.
Hydraulic Press
Operators
As with any form of manufacturing and production, safety is an initial concern. The positive side of press forging is that it does not require any form of special training for the operator except for concerns for safety.
Cooling System
Importance of cooling during the molding cycle
During the molding cycle, cooling plays a crucial role in achieving high-quality products. Cooling allows the product inside the furnace to solidify and stabilize, ensuring proper shape and dimensional accuracy. There are several methods of cooling that can be employed in the molding process.
One common cooling method is the use of cooling tubes, which are tube-shaped heat exchangers. These tubes circulate water as a coolant, effectively dissipating heat from the product. A small circulating fan helps in circulating the atmosphere inside the furnace around the cooling tubes and the product. Another method is to introduce a high-pressure atmosphere into the furnace, rapidly cooling the product. This method can also have additional effects as the heated product interacts with the atmosphere, making it a form of quenching.
Quenching is the rapid cooling of a product to produce a desired property. It can be achieved by placing the product into water or oil, both of which rapidly cool it. Alternatively, introducing a high-pressure atmosphere can also achieve rapid cooling.
Option of equipping with a cooling device
To enhance productivity and optimize the cooling process, equipping the molding system with a cooling device is an excellent option. By using a cooling device, the workpiece can be fully cooled to achieve the desired properties. After the workpiece is put into oil for cooling, it should be allowed to drain the oil in an air-cooled room, especially for workpieces with holes. The oil cooling chamber should also be vacuumed to remove any oil mist. Once the pressure is averaged, the furnace door can be opened to discharge the workpiece.
Modern laboratory equipment requires environmentally friendly cooling solutions that save cost, size, and noise. Liquid cooling systems, equipped with variable speed compressors and condenser fans, offer reduced noise impact and improved energy efficiency. These systems operate in a standby state when cooling low operating loads for extended periods, but can quickly cool at full capacity when required. The variable speed compressors and condenser fans adjust their speed to match cooling requirements, resulting in reduced noise and energy consumption.
In some applications, the cooling system cools various components, including short nets, pressure rings, protective sleeves, furnace shells, fume hoods, and chimneys, that work under high-temperature conditions. This is achieved by passing cooling water through a water separator.
Overall, the cooling system in the molding process is essential for achieving high-quality products, optimizing productivity, and ensuring efficient and environmentally friendly operations.
Closure Force Control
Digital pressure regulation system
The closure force control system in hydraulic presses plays a crucial role in ensuring the accuracy and efficiency of the pressing process. One of the latest advancements in this field is the digital pressure regulation system. This system is specifically designed for applications that require precise control of closure force.
The digital pressure regulation system incorporates a two-stage hydraulic circuit, equipped with proportional regulation valves and a continuous fine regulation pumping system. This combination allows for accurate pressure control throughout the pressing cycle. The system enables the operator to set the closure force within a range of 10 kN to 250 kN, with 10 N set force regulation steps. It ensures smooth and consistent force control, with regulation oscillations lower than 1000 N.
To utilize the digital pressure regulation system, it is necessary to install the Automatic Press Control device in conjunction with the Closure Force Control option. The Automatic Press Control device allows for setting multiple pressure regulation steps within the molding cycle, providing enhanced control and flexibility.
Accurate control of closure force
Accurate control of closure force is essential in various industrial applications, including XRF sample preparation, hot embossing, laminating, and melting polymers for thin films. The closure force determines the pressure exerted on the material being pressed, impacting the quality and consistency of the final product.
The digital pressure regulation system ensures precise control of closure force, enabling manufacturers to meet strict quality standards. With the ability to set the desired force within a specific range, it allows for tailored and optimized pressing conditions for different materials and applications.
Accurate control of closure force also minimizes the risk of product defects, such as uneven thickness, air pockets, or incomplete filling. It improves the overall efficiency of the pressing process, reducing waste and increasing productivity.
Use of Automatic Press Control for force regulation
The Automatic Press Control device is a powerful tool that enhances the functionality of hydraulic presses equipped with the digital pressure regulation system. It features a user-friendly touch screen display, allowing operators to define the molding cycle parameters with ease.
With the Automatic Press Control, operators can set the displacements of the moving platen, define the thermal cycle with different temperatures for the platens, and establish the pressure cycle with force control options. The device supports the storage of up to three molding cycles, each consisting of 24 steps.
The integration of the Automatic Press Control with the Closure Force Control option enables precise force regulation throughout the entire molding cycle. This combination empowers manufacturers to achieve consistent and reliable results, ensuring the highest quality of pressed products.
In summary, the closure force control system, particularly the digital pressure regulation system with the Automatic Press Control, revolutionizes the pressing process. It offers accurate control of closure force, optimizing the quality and efficiency of various industrial applications. Manufacturers can rely on this advanced technology to achieve consistent and precise results in their pressing operations.
Moulds
Availability of Moulds for Different Samples
When it comes to creating samples for various applications, having the right mould is crucial. Different types of moulds are available to accommodate different sample sizes and shapes. For example, KINTEK offers a selection of dies in various sizes for creating pellets, which is especially beneficial for XRF or IR spectroscopy. Additionally, models with heated platens are available for processing that involves heat, such as laminating and molding. These options ensure that you can find the perfect mould for your specific needs.
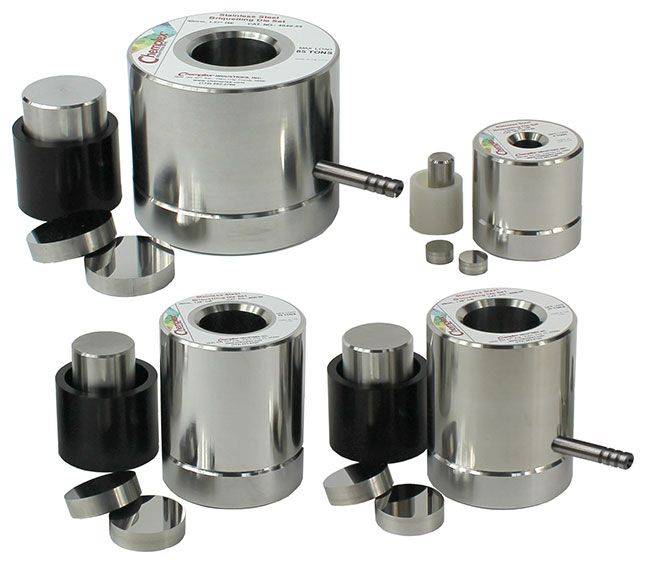
Fixing Rails with Sliding System for Easy Handling
One important feature of moulds is the ability to handle them easily. KINTEK's moulds are designed with fixing rails and a sliding system, allowing for convenient handling and movement. The mechanical structure of the moulds includes columns with self-lubricating bushings, ensuring smooth and effortless sliding of the platen. This feature makes it easy to load and unload samples, saving you time and effort.
Customization of Moulds as per Customer Requirements
Every application is unique, and sometimes standard moulds may not meet your specific requirements. That's why KINTEK offers customization options for moulds. Whether you need a specific size, shape, or material, KINTEK can tailor the mould to meet your exact needs. This level of customization ensures that you can achieve the desired results and produce high-quality samples.
In summary, having the right mould is essential for creating accurate and high-quality samples. KINTEK offers a range of mould options, including different sizes, convenient handling features, and customization capabilities. With KINTEK's moulds, you can confidently produce samples that meet your exact specifications.
KinTek Press Logger
The KinTek Press Logger is a valuable tool for monitoring and recording press conditions during manufacturing processes. With a USB port for PC connection, it allows for convenient data transfer and analysis. Here are some key features of the KinTek Press Logger:
USB Port for PC Connection
The USB port on the KinTek Press Logger enables easy connection to a computer for data transfer and analysis. This allows for convenient monitoring and recording of press conditions, such as temperature, pressure, moving platen position, and cycle step. The USB port provides a seamless interface between the press and the PC, making it easy to retrieve and analyze data.
Continuous Recording of Press Conditions
The KinTek Press Logger offers continuous recording of press conditions, providing a comprehensive view of the manufacturing process. This allows for accurate analysis and troubleshooting, ensuring that press conditions are optimized for efficiency and quality. The continuous recording feature captures real-time data, allowing for better process control and optimization.
Compatibility with Windows 10 and 11
The KinTek Press Logger is compatible with Windows 10 and 11, ensuring seamless integration with modern operating systems. This compatibility allows for easy installation and operation on the latest PCs, ensuring that manufacturers can take full advantage of the press logging capabilities. Compatibility with Windows 10 and 11 also ensures future-proofing, as manufacturers can continue to use the KinTek Press Logger with confidence as technology evolves.
The KinTek Press Logger is a valuable tool for manufacturers who want to optimize their press conditions and improve overall productivity. By providing continuous recording of press conditions and compatibility with modern operating systems, it offers a convenient and efficient solution for monitoring and analyzing press performance. With the USB port for PC connection, manufacturers can easily transfer data and make informed decisions based on accurate and real-time information.
Standard Calibration Service for Laboratory Press
Maintenance and Calibration service
Regular maintenance and calibration of your laboratory press is essential to ensure accurate and reliable results. KinTek provides a standard calibration service for laboratory presses, which includes:
- Ordinary maintenance of the instrument.
- Calibration of the temperature of the platens. The temperature is measured, with the plates closed, in 9 different points of the platens and at 3 different temperatures (140°C, 170°C, 200°C).
- Calibration of the closure force (50, 100, 150, 250 kN).
By availing our calibration service, you can be confident in the performance and accuracy of your laboratory press.
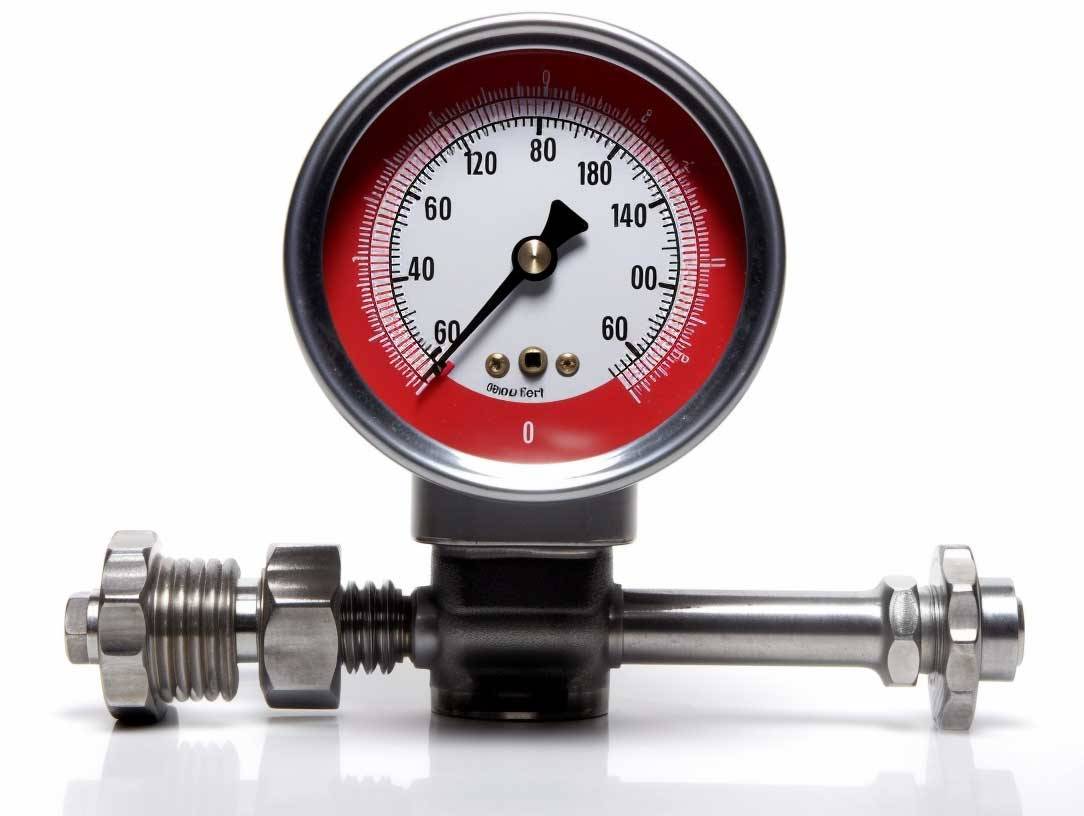
Calibration of temperature of the platens
The calibration of the temperature of the platens is a crucial aspect of ensuring accurate and consistent results in your laboratory press. KinTek's calibration service measures the temperature in 9 different points of the platens with the plates closed. This measurement is done at 3 different temperatures (140°C, 170°C, 200°C). By calibrating the temperature, you can be sure that your press is operating within the desired temperature range for your specific applications.
Calibration of the closure force
The closure force of the laboratory press is another important parameter that needs to be calibrated. KinTek's calibration service includes the calibration of the closure force at different levels (50, 100, 150, 250 kN). Accurate closure force calibration is crucial for achieving consistent and reproducible results in your press applications. With our calibration service, you can ensure that the closure force of your laboratory press is calibrated to the desired specifications.
Maintaining and calibrating your laboratory press is essential for obtaining accurate and reliable results. KinTek offers a standard calibration service that includes maintenance, calibration of the temperature of the platens, and calibration of the closure force. By availing our calibration service, you can optimize the performance of your laboratory press and ensure the accuracy of your test results.
Conclusion
In conclusion, the laboratory press is a versatile and efficient tool for various molding applications. With its mechanical structure, hydraulic system, and chrome-plated steel platens, it ensures uniform temperature distribution and safety during the molding process. The automatic press control feature, along with the option of equipping a cooling device, provides precise control over the molding cycle. The availability of different molds and customization options allows for flexibility in testing various samples. Additionally, the KinTek Press Logger offers convenient data recording and compatibility with modern operating systems. With the added benefit of standard calibration services, the laboratory press ensures accurate and reliable results for any research or testing needs.
If you are interested in this product you can browse our company website:https://kindle-tech.com/product-categories/heated-lab-press, we always insist on the principle of quality first. During the production process, we strictly control every step of the process, using high quality materials and advanced production technology to ensure the stability and durability of our products. to ensure that their performance meets the highest standards. We believe that only by providing customers with excellent quality can we win their trust and long-term cooperation.
CONTACT US FOR A FREE CONSULTATION
KINTEK LAB SOLUTION's products and services have been recognized by customers around the world. Our staff will be happy to assist with any inquiry you might have. Contact us for a free consultation and talk to a product specialist to find the most suitable solution for your application needs!