Introduction to Hot Isostatic Pressing (HIP) Technology
Definition and Basic Principles
Hot isostatic pressing (HIP) is a sophisticated technology that employs inert gases such as nitrogen and argon as the medium for pressure transmission. This method subjects a product to uniform pressure from all directions under conditions of high temperature and pressure. The process involves pressing and sintering the product, leading to significant improvements in density, uniformity, and overall performance.
The fundamental principle behind HIP lies in its ability to apply isotropic pressure, ensuring that the material undergoes consistent deformation and densification. This uniformity is crucial for enhancing the mechanical properties and microstructural integrity of the material. The inert gases used in the process not only facilitate the transmission of pressure but also prevent any chemical reactions that could compromise the material's integrity.
The HIP process can be broken down into several key stages:
- Particle Approach and Rearrangement: Initially, the particles within the material approach each other and rearrange to fill voids and gaps.
- Plastic Deformation: As the pressure increases, the particles undergo plastic deformation, further reducing the volume of voids.
- Diffusion Creep: Finally, diffusion mechanisms come into play, allowing the particles to bond at an atomic level, resulting in a fully densified and sintered product.
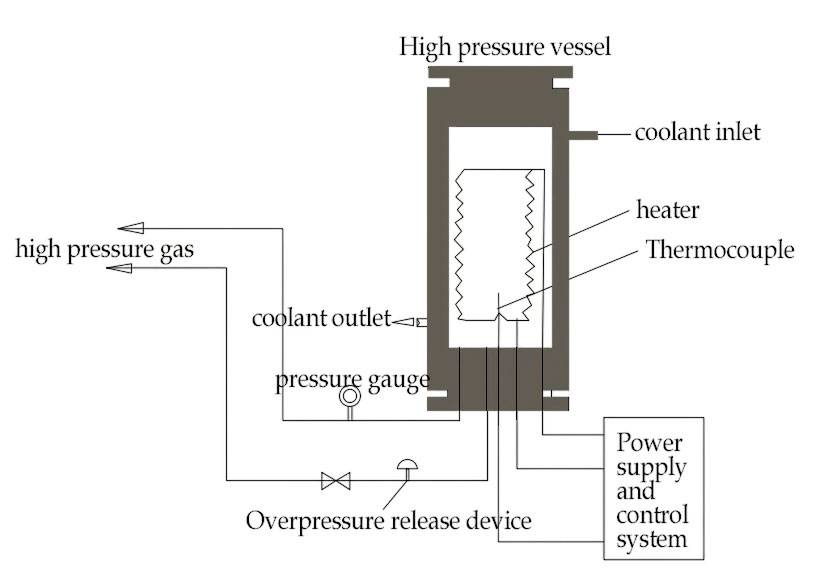
This multi-stage process ensures that the final product not only meets but often exceeds the performance standards set by traditional manufacturing methods. The combination of high temperature and uniform pressure creates a synergistic effect that enhances the material's properties, making HIP an indispensable technology in various high-performance applications.
Historical Development and Current Applications
Hot Isostatic Pressing (HIP) technology has seen extensive adoption across multiple sectors, significantly contributing to the production of high-quality products and the development of new materials. Initially, its application was primarily concentrated in the aerospace and aviation industries, where the need for materials with superior mechanical properties and high reliability was paramount. Over time, HIP technology has expanded its footprint into the energy, transportation, electrical engineering, electronics, chemical industry, and metallurgy sectors.
In the aerospace industry, HIP is utilized to produce components with complex geometries that require high strength and low weight, such as turbine blades and structural parts. The energy sector benefits from HIP through the creation of components for nuclear reactors and gas turbines, which demand exceptional durability and resistance to high temperatures and pressures. Transportation applications include the manufacturing of components for automotive and railway systems, enhancing both performance and safety.
Electrical engineering and electronics have also leveraged HIP technology to develop high-performance materials for electronic devices and power systems. In the chemical industry, HIP is employed to produce corrosion-resistant components and catalysts, while in metallurgy, it aids in the production of high-strength alloys and the repair of metal parts.
The versatility of HIP technology is further demonstrated by its emerging applications in new fields. For instance, it is being explored for use in porous materials, surface treatments, high-purity material preparation, and even in the food industry for sterilization purposes. These diverse applications underscore the broad impact and potential of HIP technology in modern industrial processes.
Components and Working Principles of HIP Equipment
Key Components of HIP Equipment
The equipment essential for Hot Isostatic Pressing (HIP) technology encompasses several critical components, each playing a vital role in the process. These components include a high-pressure vessel, a heating furnace, a compressor, a vacuum pump, a gas storage tank, a cooling system, and a computer control system.
- High-Pressure Vessel: This is the core component of the HIP system. It is designed to withstand extreme pressures and temperatures, ensuring the safe containment of the materials undergoing treatment.
- Heating Furnace: Responsible for heating the materials to the required temperature, the furnace is crucial for initiating the sintering process.
- Compressor: This component generates the necessary pressure to compact the materials, ensuring uniformity and density.
- Vacuum Pump: Prior to the application of pressure, the vacuum pump removes air and other gases from the system, creating a controlled environment for the HIP process.
- Gas Storage Tank: Stores the inert gas used as the pressure medium, ensuring a consistent supply during the pressing process.
- Cooling System: After the pressing and sintering, the cooling system rapidly cools the materials to prevent any unwanted reactions and to stabilize the final product.
- Computer Control System: Manages and monitors all aspects of the HIP process, from temperature and pressure control to data collection and analysis, ensuring precision and efficiency.
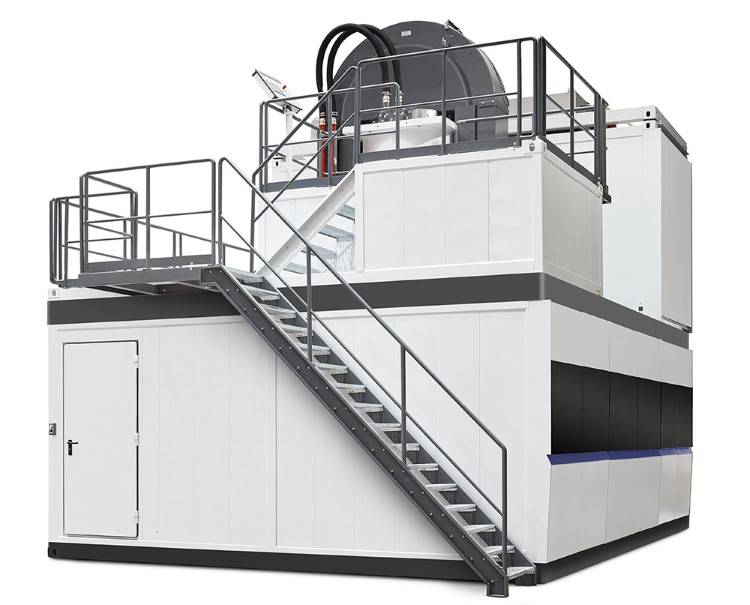
Each of these components is meticulously engineered to work in harmony, enabling the HIP technology to deliver high-quality, dense, and uniform products across various industries.
Process Flow and Densification Mechanisms
The Hot Isostatic Pressing (HIP) process is a meticulously orchestrated sequence of stages that collectively contribute to the densification of powder materials. This process can be broken down into three primary stages: particle approach and rearrangement, plastic deformation, and diffusion creep. Each of these stages plays a crucial role in achieving the desired level of densification, and they often operate in tandem rather than sequentially.
In the initial stage, particle approach and rearrangement, the powder particles are brought into closer proximity and reorganized to optimize their packing density. This stage is critical for setting the foundation for subsequent densification processes. The particles move and align in a manner that minimizes voids and maximizes contact points, creating a more cohesive structure.
The second stage, plastic deformation, involves the application of mechanical stress that causes the powder particles to deform plastically. This deformation is facilitated by the high pressure and temperature conditions maintained during the HIP process. As the particles deform, they fill in the gaps left by the rearrangement stage, further reducing the overall porosity of the material.
The final stage, diffusion creep, is where the densification process reaches its zenith. Under the sustained high temperature and pressure, atomic diffusion becomes significant. This diffusion allows for the elimination of residual voids and micro-cracks, leading to a material that is nearly fully dense and free of significant internal defects. The simultaneous operation of these stages ensures that the powder is transformed into a high-density, homogeneous, and mechanically robust final product.
Stage | Description |
---|---|
Particle Approach & Rearrangement | Powder particles are brought closer and reorganized to optimize packing. |
Plastic Deformation | Particles deform plastically under high pressure and temperature. |
Diffusion Creep | Atomic diffusion eliminates voids and micro-cracks, achieving full densification. |
This multi-stage process not only enhances the mechanical properties of the material but also ensures uniformity across the entire product, making it suitable for demanding applications in industries such as aerospace, automotive, and energy.
Applications of HIP Technology
Densification Treatment of Castings
Hot Isostatic Pressing (HIP) technology is instrumental in both the densification of new castings and the repair of used ones, effectively restoring their performance to pristine levels. By eliminating internal defects such as microporosity and microcracks, HIP ensures that the castings meet the highest standards of material performance. This process is particularly crucial for materials like aluminum, titanium, and high-temperature alloys, where the cooling rates during the forming process can lead to uneven internal structures.
For instance, in the case of titanium alloys, despite significant advancements in precision casting techniques, HIP remains an indispensable step in the post-processing phase. The application of gas pressure at elevated temperatures induces plastic deformation and diffusion bonding, thereby eradicating internal microporosity and enhancing the overall mechanical properties of the castings.
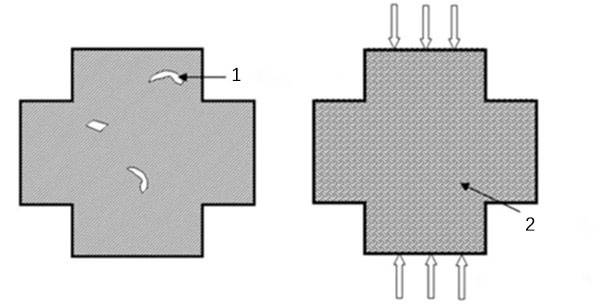
The benefits of HIP in casting densification are manifold. It not only improves product consistency by reducing variations in mechanical properties but also significantly enhances key performance metrics. For example, tensile and proof strengths typically increase by around 5%, while ductility can improve by up to 50%. Moreover, the fatigue properties of HIP-treated castings can improve up to tenfold, achieving fatigue life comparable to wrought alloys. This improvement extends to other critical properties such as impact strength, toughness, and machined surface finish.
In summary, HIP's role in casting densification is pivotal, offering a pathway to optimize casting performance and expand their applicability to new and more demanding applications.
Cladding and Composite Diffusion Bonding
Hot Isostatic Pressing (HIP) technology offers advanced methods for enhancing material performance through processes like cladding and composite diffusion bonding. These techniques are particularly valuable for bonding dissimilar materials, which can significantly improve the overall strength and durability of components.
Diffusion Bonding: A Versatile Process
Diffusion bonding, a key aspect of HIP technology, allows for the seamless joining of both similar and dissimilar materials, whether in powder or solid form. This process eliminates the need for traditional welding methods, reducing the number of welds and associated inspections. The result is a more reliable and cost-effective manufacturing process.
Cladding: Optimizing Material Usage
Cladding through HIP enables the formation of components with premium or expensive materials only in critical regions. This strategic use of materials not only reduces overall costs but also ensures that the most demanding areas of the component receive the highest quality materials. For instance, in aerospace applications, this can mean using lightweight alloys in non-critical areas and high-strength alloys in areas subjected to extreme stress.
Benefits of HIP Cladding and Diffusion Bonding
Benefit | Description |
---|---|
Reduction in Welds | Eliminates or reduces the number of welds, minimizing potential failure points. |
Cost Efficiency | Optimizes material usage, reducing the need for expensive alloys throughout. |
Improved Performance | Enhances overall component strength and durability through seamless bonding. |
Versatility | Suitable for a wide range of materials, including refractory and high-strength alloys. |
In summary, HIP cladding and composite diffusion bonding are transformative processes that not only improve material performance but also offer significant economic and operational advantages. Whether applied to bond two parts or to create layered structures, these techniques are essential for advancing the capabilities of modern engineering and manufacturing.
Powder Consolidation in Various Materials
Hot Isostatic Pressing (HIP) is a versatile technique employed for consolidating a wide array of materials, including high-temperature alloys, cemented carbide, high-speed steel, ceramic materials, and titanium alloys. This process significantly enhances the performance of these materials and reduces manufacturing costs, making it an attractive alternative to traditional casting or deformation processing methods.
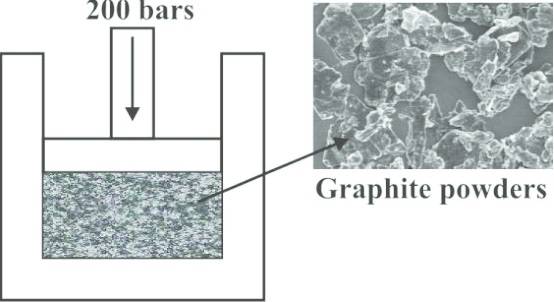
Key Materials Benefiting from HIP
Material Type | Application Areas | Performance Improvements |
---|---|---|
High-Temperature Alloys | Aerospace, Energy, Transportation | Increased strength and durability |
Cemented Carbide | Cutting Tools, Mining Equipment | Enhanced hardness and wear resistance |
High-Speed Steel | Machine Tools, Cutting Instruments | Improved cutting efficiency |
Ceramic Materials | Electronics, Automotive, Medical Devices | Better thermal and electrical properties |
Titanium Alloys | Aerospace, Medical Implants | Reduced weight and improved biocompatibility |
Process Stages in HIP Consolidation
- Preparation: The powder is mixed with a fugitive binder and molded into the required shape using pressure at ambient temperature. A controlled atmosphere with protective gases is essential for this stage.
- Heating and Consolidation: The material is heated to just below its melting point, activating the formation of martensitic crystalline microstructures.
- Particle Merging: The particles become denser and eventually merge together, a process that can be accelerated using liquid phase sintering (LPS).
- Solidification: The material cools and solidifies, creating a single, unified mass with improved properties.
By consolidating these materials through HIP, industries can achieve higher quality components with superior performance, making HIP an indispensable technology in modern manufacturing.
Emerging Applications in New Fields
Hot Isostatic Pressing (HIP) technology is not confined to traditional industrial applications; it is also being actively explored in emerging fields, broadening its scope and utility. One of the most promising areas is the use of HIP in the treatment of porous materials. By applying uniform pressure and high temperatures, HIP can effectively close pores and microcracks, enhancing the structural integrity and performance of these materials.
In surface treatments, HIP offers a unique solution for improving the durability and functionality of surfaces. This technology can be employed to create hard, wear-resistant coatings on components, significantly extending their service life in harsh environments. Moreover, HIP is being utilized in the preparation of high-purity materials, where its ability to achieve uniform densification is crucial for producing materials with exceptional purity and homogeneity.
Another intriguing application of HIP is in the food industry, where it is being investigated for sterilization purposes. The high-pressure and high-temperature conditions provided by HIP can effectively kill microorganisms, making it a potential alternative to traditional sterilization methods. This application not only highlights the versatility of HIP technology but also opens up new avenues for its use in ensuring food safety and quality.
Application Field | Specific Use of HIP |
---|---|
Porous Materials | Closing pores and microcracks, enhancing structural integrity |
Surface Treatments | Creating hard, wear-resistant coatings, extending service life |
High-Purity Material Prep. | Achieving uniform densification, producing high-purity materials |
Food Industry | Sterilization, ensuring food safety and quality |
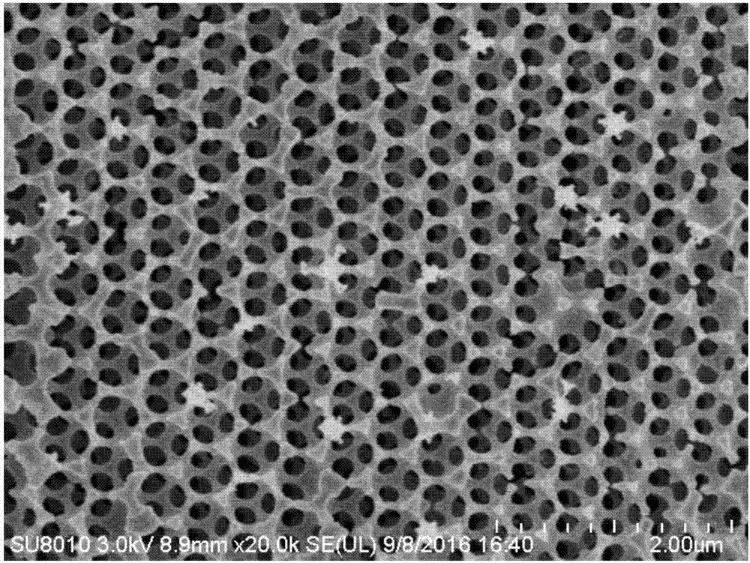
These emerging applications demonstrate the adaptability and innovation potential of HIP technology, suggesting that its influence will continue to expand across various industries.
Conclusion and Future Prospects
Impact on Modern Production Technology
Hot Isostatic Pressing (HIP) technology has significantly impacted modern production, fostering the creation of innovative materials and broadening its influence across numerous technical domains. This technology, which employs inert gases like nitrogen and argon to apply uniform pressure under high temperatures, has revolutionized material densification processes. The resulting materials exhibit exceptional density, uniformity, and performance, which are crucial for advanced applications in sectors such as aerospace, energy, and electronics.
One of the key contributions of HIP technology is its ability to consolidate powders into fully dense materials without the need for additional binders or sintering aids. This capability is particularly valuable in the production of high-temperature alloys, cemented carbides, and ceramic materials, where achieving high density and strength is essential. The process involves three primary stages—particle approach and rearrangement, plastic deformation, and diffusion creep—all of which operate concurrently to achieve optimal densification.
Moreover, HIP technology has found new applications in emerging fields, such as the treatment of porous materials and the preparation of high-purity materials. For instance, it is being explored for use in sterilizing food products, demonstrating its versatility and potential beyond traditional industrial applications. The ability of HIP to repair and densify used castings, restoring them to near-new performance levels, further underscores its value in modern manufacturing.
In summary, HIP technology's role in modern production is multifaceted, driving advancements in material science and expanding its utility across a diverse array of industries. Its continuous evolution and adaptability promise to unlock even more innovative applications in the future.
CONTACT US FOR A FREE CONSULTATION
KINTEK LAB SOLUTION's products and services have been recognized by customers around the world. Our staff will be happy to assist with any inquiry you might have. Contact us for a free consultation and talk to a product specialist to find the most suitable solution for your application needs!