Introduction to Isostatic Pressing
Isostatic pressing is a manufacturing process used to produce high-density materials with improved mechanical properties. It operates by applying uniform pressure to the material from all directions to eliminate voids, cracks, and porosity. The process is divided into two categories: hot isostatic pressing (HIP) and cold isostatic pressing (CIP). HIP uses high temperature and pressure to densify materials, while CIP operates at room temperature and lower pressure. Both methods are used in various industries, including aerospace, biomedical, and power generation, to produce complex shapes and parts with high strength and durability.
Table of Contents
Overview of Hot Isostatic Pressing (HIP)
Hot Isostatic Pressing (HIP) is a widely used process in the manufacturing of various materials, including high-performance alloys, ceramics, and composites. It involves the application of heat and pressure to a material within a sealed container to improve its mechanical properties, such as strength, ductility, and toughness. During the HIP process, the material is heated to a high temperature, typically above 1000°C, and pressurized with an inert gas, such as argon, to up to 200 MPa.
How Does HIP Work?
The HIP process helps to remove any internal defects, such as pores and cracks, by consolidating the material and shrinking it uniformly. The process can be used to produce complex shapes and intricate parts, including turbine blades, rocket nozzles, and medical implants. HIP also has the advantage of being able to repair and restore damaged components, such as turbine blades, by removing any cracks and restoring their original properties.
Comparison with Hot Pressing
Compared to hot pressing, HIP can provide material shapes not much different from the initial one after pressure. A material even after changing its shape can keep its initial shape, and will be relatively less restricted by processing of products. By making full use of these features, HIP has been applied in various fields.
HIP Application
HIP is applied in a wide range of fields such as pressure sintering of powder, diffusion bonding of different types of materials, removal of residual pores in sintered items, removal of inner defects of castings, rejuvenation of parts damaged by fatigue or creep, high-pressure impregnated carbonization method, etc.
Pressure Medium
Argon gas at 1000°C and under pressure of 98MPa is likely to cause intense convection due to low density and coefficients of viscosity and high coefficients of thermal expansion. Therefore, heat transfer coefficients of HIP equipment become higher than that of an ordinary electronic furnace.
HIP Treatment
Materials need various treatments depending on the situations. The most typical methods include 'Capsule Method' and 'Capsule Free Method.' Isostatic pressing is a powder metallurgy (PM) forming process that applies equal pressure in all directions on a powder compact, thus achieving maximum uniformity of density and microstructure without the geometrical limitations of uniaxial pressing.
Advantages of HIP
Hot Isostatic Pressing is a well-established process for the improvement of a wide variety of materials such as titanium, steel, aluminum, and superalloys. It can reduce scrap, improve yield, replace wrought components with castings, reduce quality assurance inspection requirements by improving material properties and reducing property scatter, optimize material properties, minimize subsequent heat treatment requirements, enhance reliability and extension of service life, reduce the total production costs of a product, etc.
In summary, Hot Isostatic Pressing is a highly effective method for improving the mechanical properties of materials and producing complex parts with high precision and accuracy.
Advantages of HIP
Hot Isostatic Pressing (HIP) is a superior manufacturing process for laboratory equipment due to its ability to produce fully consolidated, high-density parts with superior mechanical properties. Here are some of the advantages of HIP:
Fully Consolidated Parts
HIP produces fully consolidated parts with high-density, which means that the material is free from porosity. This results in improved mechanical properties, such as high strength, toughness, and ductility, making it ideal for applications that require high-performance materials.
Complex Shapes and High Dimensional Accuracy
HIP can be used to produce complex shapes and parts with high dimensional accuracy, as it eliminates shrinkage and distortion during the process. This is achieved through the simultaneous application of high temperature and pressure in all directions, which results in uniformity of the material's density.
Versatility
HIP can be used to process a wide range of materials, including metals, ceramics, and composites, making it a versatile process for manufacturing laboratory equipment. It also allows simultaneous densification and bonding of powders or porous bodies.
Cost-Effective
HIP is a cost-effective process, as it eliminates the need for additional processing steps, such as sintering, which reduces material waste and energy consumption. It also allows for the processing of larger parts, which can save on production costs.
Enhanced Properties
HIP improves the mechanical properties of the parts that it processes. It achieves this by eliminating internal porosity, achieving a fine-grain structure which promotes part uniformity, and enabling diffusion bonding of similar and dissimilar materials, either in powder or solid form. This results in improved impact resistance, ductility, and fatigue strength, among other properties.
In conclusion, Hot Isostatic Pressing is an essential technology for the production of advanced laboratory equipment that requires high-performance materials. Its ability to produce fully consolidated, high-density parts with excellent mechanical properties makes it a versatile and cost-effective process that can be used to produce complex shapes from a wide range of materials.
Disadvantages of HIP
High Cost of Equipment and Maintenance
HIP requires specialized equipment that can withstand high pressure and temperature, which can be expensive to purchase and maintain. Additionally, the process requires a significant amount of energy to maintain the high temperatures, which can increase the overall cost of production.
Limited Range of Materials that can be Processed
HIP is typically used for metals and ceramics, but it may not be suitable for processing polymers or other materials that are sensitive to high temperatures and pressures. This limits the versatility of the process and may require additional processing methods to achieve the desired material properties.
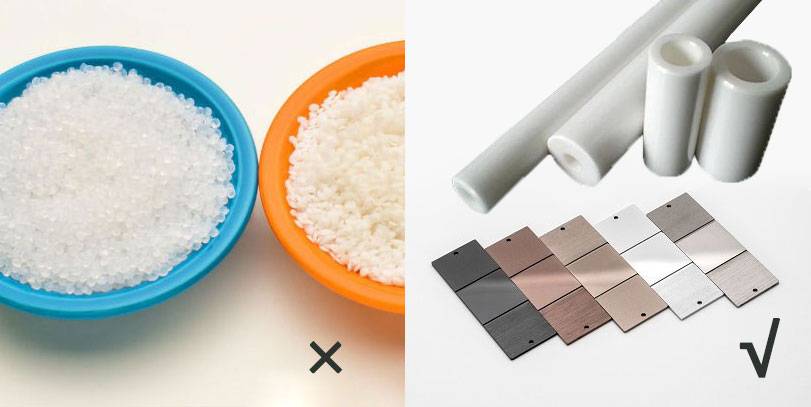
Residual Stresses in the Material
HIP can also lead to the formation of residual stresses in the material, which can cause cracking or deformation. These stresses can arise from non-uniform heating or cooling during the process or from uneven application of pressure. To mitigate this issue, post-processing methods may be required to relieve the residual stresses and ensure the material meets the desired specifications.
In conclusion, while HIP offers several advantages for densifying materials, it also has some disadvantages that need to be considered. These include the high cost of equipment and maintenance, limited range of materials that can be processed, and the potential for residual stresses in the material. By understanding these limitations, engineers and researchers can make informed decisions about when to use HIP and how to optimize the process for their specific applications.
Overview of Cold Isostatic Pressing (CIP)
Cold Isostatic Pressing (CIP) is a method of shaping and compacting powders into components of varying sizes and shapes. The process is performed at room temperature and at lower pressures, unlike Hot Isostatic Pressing (HIP), which is performed at elevated temperatures.
How does CIP work?
CIP involves immersing the material into a bath of pressurized fluid, typically water, and applying pressure from all directions using an isostatic pressure vessel. The applied pressure helps to compress the material and remove any porosity or voids present in the material. The process utilizes a flexible rubber mold that applies uniform pressure to the material. The mold is placed into a hydraulic fluid in a pressure vessel, and high pressure is applied to the fluid, usually between 10,000 and 60,000 psi, which is evenly distributed across the material.
Advantages of CIP
CIP is a favored technique because it can produce parts with a high level of uniformity, strength, and density, making them ideal for use in critical applications such as aerospace, medical, and defense. Additionally, CIP can be used to produce complex shapes that may be difficult to achieve using other techniques.
Comparison with Uniaxial Pressing
Both uniaxial pressing and CIP are methods for compacting powder samples. In uniaxial pressing, a force is applied along one axis, while in CIP, the sample is put into a flexible bag or mold and placed into a hydraulic fluid in a chamber. High pressure is applied to the liquid medium, which in turn applies uniform pressure to the sample in all directions. This allows for a much higher degree of compaction than uniaxial pressing and thus can be used to produce large samples.
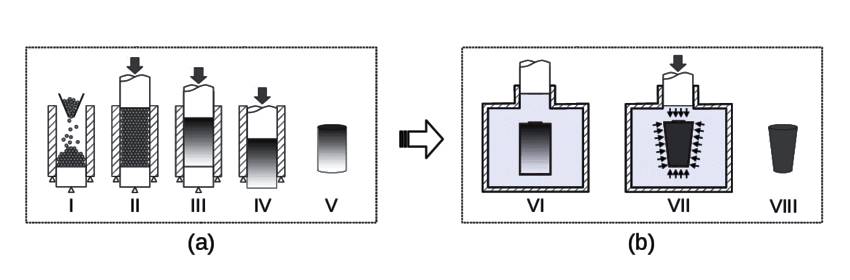
Types of CIP
There are two types of CIP currently recognized worldwide, wet bag technology, and dry bag technology. Wet bag technology involves filling the powder into a mold and sealing it tightly outside the pressure vessel. After filling the mold with powder, the mold is submerged in the pressure fluid within the pressure vessel. Dry bag technology, on the other hand, involves fixing the mold in the pressure vessel. The powder is filled in the mold while it is still in the pressure vessel.
Advantages of CIP over Uniaxial Pressing
CIP offers more uniform product properties, greater homogeneity, and more precise control of the finished product dimensions. It offers greater flexibility in the shape and size of the finished product, and longer aspect ratios are possible. The improved compaction of the powder leads to improved densification, and CIP can process materials with different characteristics and shapes. Lastly, CIP can reduce cycle times and improve productivity.
In conclusion, CIP is a powerful technique used to shape and compact powders into components of varying sizes and shapes. It offers several advantages over uniaxial pressing and is a favored technique for producing high-quality materials for critical applications.
Advantages of CIP
Cold Isostatic Pressing (CIP) offers several advantages over other similar processes. Some of the significant benefits of CIP are as follows:
Uniform Strength
CIP applies pressure equally in all directions, resulting in materials with uniform strength. This uniform strength makes materials more efficient and effective.
Versatility
CIP can produce complex shapes that are difficult to create using other manufacturing methods. It can also produce large-sized materials without compromising their quality.
Corrosion Resistance
CIP improves the corrosion resistance of materials, leading to a longer lifespan than most other materials.
Improved Mechanical Properties
CIP improves the mechanical properties of materials, including ductility and strength.
Suitable for Powder Metallurgy
CIP is used for the compacting step of powder metallurgy that comes just before the sintering step. It is often used to produce complex shapes and dimensions.
Production of Refractory Metals
CIP is used to produce refractory metals such as tungsten, molybdenum, and tantalum. These metals have a high melting point and are resistant to wear and tear.
Production of Sputtering Targets
CIP can press indium tin oxide (ITO) powder into large ceramic preforms, which are then sintered under certain conditions. This method can theoretically produce ceramic targets with a density of 95%.
Used in Automobiles
CIP is used in the manufacturing of automobile components such as bearings and oil pump gears.
Faster Sintering
Cold isostatic pressed products have a high green strength that allows them to be sintered faster than other materials.
In summary, CIP is becoming increasingly popular due to its many advantages over similar manufacturing processes. Its versatility, ability to produce complex shapes, and improved mechanical properties make it an excellent choice for manufacturing companies looking for high-quality, complex parts for their products.
Disadvantages of CIP
Cold Isostatic Pressing (CIP) is an effective method for compacting powdered materials into a solid homogeneous mass before machining or sintering. However, there are some disadvantages of CIP which must be taken into consideration before selecting this method for a given application.
Not Suitable for High-Temperature Materials
One of the major disadvantages of CIP is that it is not suitable for materials that require high temperatures to achieve optimal properties. This is because CIP relies on the application of pressure to the material at room temperature, which limits the extent to which the material can be compressed. As a result, CIP is not a suitable method for materials that require high-temperature processing, such as metals, alloys, or ceramics.
Introduction of Unwanted Porosity
CIP can result in the introduction of unwanted porosity in the material, which can negatively affect its mechanical properties. This is because the pressure applied during the CIP process may result in the formation of voids or gaps within the material, which can reduce its strength and durability. The extent of porosity introduced in the material depends on several factors, including the quality of the powder, the design of the tooling, and the pressure applied during the CIP process.
Limitations on the Complexity of Shapes
CIP is not suitable for all shapes of components. It is limited to producing components with simple shapes, such as thin tiles. This is because the pressure applied during the CIP process may result in non-uniform particle packing due to pressure gradients, which can cause distortions and cracking in complex-shaped components.
Limited Pressure Range
Another disadvantage of CIP is that it has a limited pressure range. CIP is typically limited to a pressure range of about 200 MPa to 400 MPa. This is because higher pressures require more specialized equipment and may result in deformation or failure of the tooling used in the CIP process.
In summary, while CIP is a useful technique for some applications, it has several disadvantages that must be taken into consideration before selecting this method for a given application.
Comparison between HIP and CIP
Hot Isostatic Pressing (HIP) and Cold Isostatic Pressing (CIP) are two commonly used methods of creating high-density materials. The difference between the two lies in the temperature at which they are performed. Here are some of the key differences between HIP and CIP:
Temperature and Pressure
HIP is carried out at high temperature and pressure, while CIP is performed at room temperature. In HIP, the material is first placed in a mold and then subjected to high heat and pressure, which cause it to become denser and more uniform in composition. The high temperature also allows for the removal of any residual porosity or defects in the material. CIP, on the other hand, involves placing the material in a flexible container and subjecting it to high pressure from all sides.
Density and Uniformity
HIP produces materials that are denser and more uniform in composition compared to CIP. The high temperature and pressure in HIP result in the removal of any residual porosity or defects in the material, resulting in a more uniform density and a reduction in defects. CIP produces materials that are less dense compared to HIP, but the materials produced are still uniform in density and have a low level of defects.
Applications
HIP is often used in the aerospace industry for producing high-performance alloys and ceramics, while CIP is commonly used in the production of ceramic components, such as those used in the electronics industry. This is because HIP produces materials that are stronger and more resistant to high temperatures and pressure, making them suitable for aerospace applications. CIP, on the other hand, produces materials that are less dense but still uniform in density, making them suitable for electronic applications.
Cost and Time
HIP is a more expensive and time-consuming process compared to CIP. This is because it requires high temperatures and pressures, which can be costly to maintain. CIP, on the other hand, is a less expensive and faster process compared to HIP because it is carried out at room temperature and does not require high temperatures and pressures.
In summary, both HIP and CIP have their own advantages and disadvantages, and the choice between the two will depend on the specific requirements of the application. HIP produces materials that are stronger and more resistant to high temperatures and pressure, making them suitable for aerospace applications. CIP produces materials that are less dense but still uniform in density, making them suitable for electronic applications. However, CIP is a less expensive and faster process compared to HIP.
Conclusion
Both hot isostatic pressing (HIP) and cold isostatic pressing (CIP) have their own advantages and disadvantages. While HIP is a more expensive process, it provides higher-quality products with better mechanical properties. On the other hand, CIP is a more cost-effective solution that can be used for large-scale production of complex shapes. Ultimately, the choice between HIP and CIP will depend on the specific requirements of the application. HIP is commonly used in aerospace, medical, and nuclear industries, while CIP is preferred in the automotive and electronics industries.
CONTACT US FOR A FREE CONSULTATION
KINTEK LAB SOLUTION's products and services have been recognized by customers around the world. Our staff will be happy to assist with any inquiry you might have. Contact us for a free consultation and talk to a product specialist to find the most suitable solution for your application needs!