Introduction to Warm Isostatic Press
Warm Isostatic Press (WIP) is a type of isostatic press that uses a combination of heat and pressure to create high-quality parts. The WIP process involves placing a part inside a flexible mold, which is then filled with a gas or liquid media. The mold is then subjected to high pressures and temperatures, which causes the media to flow evenly around the part, exerting uniform pressure on all sides. WIP is commonly used in the production of ceramics, composites, and other high-performance materials that require precise molding and high-density. Compared to cold isostatic press (CIP) and hot isostatic press (HIP), WIP offers a more cost-effective and time-saving solution for producing parts with complex shapes and optimal material properties.
Table of Contents
- Introduction to Warm Isostatic Press
- Differences between Cold, Warm, and Hot Isostatic Press
- Benefits of Warm Isostatic Press
- Warm Isostatic Laminator for High-Quality Monolithic Multilayer Ceramics
- How Warm Isostatic Press Works
- Operating Temperature Range of Warm Isostatic Press
- Importance of Proper Temperature Control for Molding Quality
- Tips for Ensuring Molding Quality and Efficiency
- Conclusion
Differences between Cold, Warm, and Hot Isostatic Press
Isostatic pressing is a popular technique used in manufacturing various materials such as ceramics, metals, and composites. This method improves the density, structure, and properties of materials by applying a uniform pressure to the material through a closed vessel. There are three types of isostatic pressing: cold, warm, and hot. The main differences between them are the temperatures at which they operate during forming and consolidation.
Cold Isostatic Press (CIP)
Cold isostatic presses are used in room temperature environments and are suitable for temperature-sensitive materials such as ceramics, metal powders, etc. This method is based on applying a uniform pressure to the material through a closed vessel at room temperature. CIP has the advantage of producing uniform strength in all directions, uniform density, and shape flexibility.
Warm Isostatic Press (WIP)
Warm isostatic pressing (WIP) is a variant of cold isostatic pressing (CIP) that includes a heating element. This method uses warm water or a similar medium to apply uniform pressure to powdered products from all directions. WIP is an excellent compromise between CIP and Hot Isostatic Press (HIP). It can accommodate a wider range of materials and has a lower energy requirement than HIP, yet it offers better mechanical properties and a higher density than CIP. WIP is commonly used for powders, binders, and other materials that have special temperature requirements or cannot be molded at room temperature.
Hot Isostatic Press (HIP)
Hot isostatic presses operate at high temperatures and are suitable for materials with high-temperature requirements, such as metals and alloys. This method is based on applying a uniform pressure to the material through a closed vessel at high temperatures. HIP has the advantage of eliminating internal porosity, improving mechanical properties such as impact resistance, ductility, and fatigue strength, and providing homogeneous microstructures. HIP also enables diffusion bonding of similar and dissimilar materials, either in powder or solid form.
In conclusion, each type of isostatic pressing method has its advantages and disadvantages, and the selection of the appropriate method depends on the characteristics of the powder material and the requirements of the molding effect. By considering the differences between CIP, WIP, and HIP, manufacturers can produce high-quality products that meet the industry's high standards.
Benefits of Warm Isostatic Press
Warm Isostatic Press (WIP) is a versatile equipment that has become increasingly popular in various industries. Here are some of the benefits of using WIP:
1. High Molding Quality and Efficiency
One of the main benefits of WIP is its ability to ensure high molding quality and efficiency. The equipment can maintain a uniform temperature and pressure inside the chamber, which helps in achieving a consistent density and shape of the molded material. This eliminates the need for post-molding treatments, such as sintering, which saves time and money.
2. Wide Range of Material Processing
WIP can be used to process a wide range of materials, such as ceramics, metals, and composites. This makes it a versatile option for various industries, such as aerospace, automotive, and medical devices.
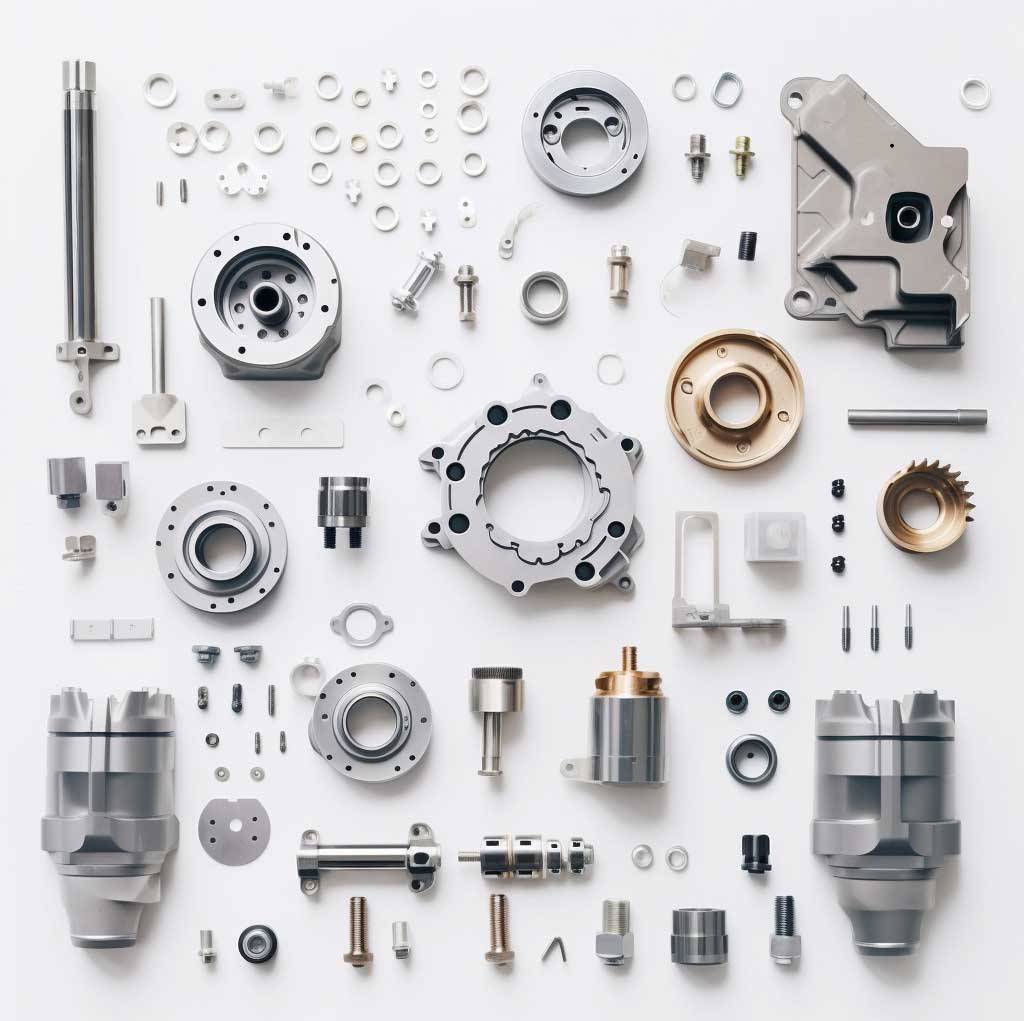
3. Environmental Friendly Option
The use of WIP helps in reducing the amount of waste generated during the molding process, which is an environmentally friendly option. This is because WIP eliminates the need for post-molding treatments, such as sintering, which generates waste.
4. Enhanced Mechanical Properties
WIP can improve the mechanical properties of the molded material. This is because WIP can achieve a high-quality mold, which has a consistent density and shape. This, in turn, results in a higher quality finished product.
5. Reduction in Production Costs
The use of WIP can result in a reduction in production costs. This is because WIP eliminates the need for post-molding treatments, such as sintering. Additionally, WIP can achieve a high-quality mold, which reduces the need for additional processing steps.
In conclusion, the use of Warm Isostatic Press has several benefits that make it a valuable investment for businesses that rely on precision manufacturing. From high molding quality to a reduction in production costs, WIP can significantly improve the quality and efficiency of molding processes.
Warm Isostatic Laminator for High-Quality Monolithic Multilayer Ceramics
A Warm Isostatic Laminator is an essential part of the Warm Isostatic Press (WIP) process. It is used to stack and compress ceramic materials to form a monolithic multilayer ceramic structure. The WIP process ensures that the ceramic product has high density, uniform microstructure, and excellent mechanical properties. Here are the steps involved in using a Warm Isostatic Laminator for high-quality monolithic multilayer ceramics:
Step 1: Preparation of Ceramic Materials
Before using the Warm Isostatic Laminator, the ceramic materials need to be prepared. The materials are usually in the form of powders, which are mixed with a binder to form a slurry. The slurry is then poured into a mold to form a green body.
Step 2: Stacking of Ceramic Materials
The green bodies are then stacked together to form a monolithic multilayer structure. The layers are arranged in a way that creates the desired shape and size of the final product. The layers can be of different materials and thicknesses, depending on the application.
Step 3: Compression of Ceramic Materials
Once the green bodies are stacked, they are placed in the Warm Isostatic Laminator. The laminator applies pressure and heat to the ceramic materials in a sealed chamber. The pressure and heat cause the powders to consolidate into a dense, high-quality ceramic structure. The laminator ensures that the layers are compressed evenly and uniformly, resulting in a monolithic multilayer structure with high density and uniform microstructure.
Step 4: Removal of Binder
After the compression process, the ceramic structure still contains a binder. The structure is then heated to remove the binder and sinter the ceramic materials together. The sintering process results in a ceramic product with excellent mechanical properties, such as high strength, hardness, and wear resistance.
The Warm Isostatic Laminator is an essential part of the WIP process for producing high-quality ceramic products with minimal waste and reduced energy consumption. It is widely used in industries such as aerospace, electronics, and medical devices, where high-quality ceramics are required for critical applications. With the help of the Warm Isostatic Laminator, manufacturers can produce complex geometries that are difficult to achieve with other molding methods.
In conclusion, the Warm Isostatic Laminator is a critical component of the WIP process for creating high-quality monolithic multilayer ceramics. The laminator ensures that the ceramic materials are stacked and compressed uniformly, resulting in a dense and high-quality product. By following the steps outlined above, manufacturers can ensure that their ceramic products meet the highest standards of quality and efficiency.
How Warm Isostatic Press Works
A warm isostatic press (WIP) is a laboratory equipment that uses high temperature and pressure to compact and shape materials into intricate shapes and designs. The WIP works by placing the material into a mold and then applying heat and pressure to the mold in a sealed chamber. This process helps to eliminate any voids or defects in the material, resulting in a more consistent and durable product.
Step 1: Loading the Material
The first step in using a WIP is loading the material into the mold. The material can be in the form of a powder, a preform, or a solid block. The mold may be made of graphite, ceramic, or metal depending on the material being processed.
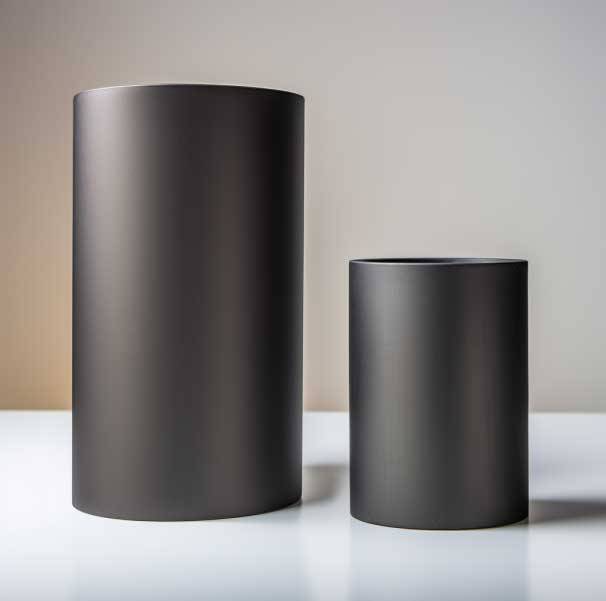
Step 2: Sealing the Chamber
Once the mold is loaded with the material, it is placed inside the WIP chamber. The chamber is then sealed tightly to prevent any gas from escaping during the process. The sealing process is critical to ensure that the heating and pressurization are carried out effectively.
Step 3: Heating the Chamber
The next step is to heat the chamber to the required temperature. The temperature and heating rate are critical factors in the success of the process. The temperature is often set at or above the melting point of the material being processed. This is to ensure that the material becomes plastic and can be easily shaped.
Step 4: Applying Pressure
Once the desired temperature is reached, the pressure is applied to the mold. The pressure is applied uniformly in all directions, which is known as isostatic pressure. This causes the material to become "plastic," allowing voids to collapse under the differential pressure. The surfaces of the voids diffusion bond together, effectively eliminating the defects and achieving near theoretical density.
Step 5: Cooling the Chamber
After the required pressure and temperature are maintained for a specified time, the chamber is cooled down to room temperature. This is done slowly to prevent any thermal shock to the material. The cooling rate is also an important factor that affects the final properties of the material.
In conclusion, using a warm isostatic press can significantly improve the quality and efficiency of molding processes. The WIP can be used with a variety of materials, including metals, ceramics, and composites, making it a versatile tool for a wide range of applications. However, it is crucial to carefully select the appropriate materials and mold designs and follow the manufacturer's instructions for operating and maintaining the equipment to ensure the best results.
Operating Temperature Range of Warm Isostatic Press
Warm Isostatic Press (WIP) is a technology that uses high pressure and temperature to compress and consolidate materials into a desired shape. The operating temperature range of a WIP is crucial to its effectiveness. The temperature range of a WIP typically ranges from 100°C to 200°C.
Ideal temperature range
This temperature range is ideal for materials like ceramics, metals, and polymers. The higher end of the temperature range is suitable for high-performance materials that require high temperatures to achieve the desired properties. The WIP process also helps to eliminate porosity and voids in the final product, resulting in high-quality and efficient molding.
WIP benefits
The WIP process has many benefits, including the ability to produce complex shapes, improve material properties, and eliminate defects. With its wide operating temperature range, the WIP is a versatile tool that can be used in a variety of industries, including aerospace, automotive, and medical equipment.
Temperature control
The temperature range of a WIP can be controlled by using a special liquid or gas as the pressure transfer medium, generally at temperatures between 100 and 200°C. The medium can be heated outside the high-pressure cylinder or inside the high-pressure cylinder when precise temperature control is required. When precise temperature control is required, the medium can also be heated inside the high-pressure cylinder with a heat generator. The oil heated in the supply tank is usually used to maintain the oil temperature at a stable level or heated and cooled according to the process requirements.
Importance of Proper Temperature Control for Molding Quality
Temperature control is a critical factor in ensuring the success of the molding process. The mold material needs to be in the correct state before it is molded, and proper temperature control is essential for achieving this.
The Effects of Improper Temperature Control
If the temperature is too low, it can cause the material to be brittle and prone to cracking. On the other hand, if the temperature is too high, it can cause the material to be too soft or even melt, making it unsuitable for molding. Therefore, maintaining the correct temperature range for the mold material is crucial to achieving the desired quality.
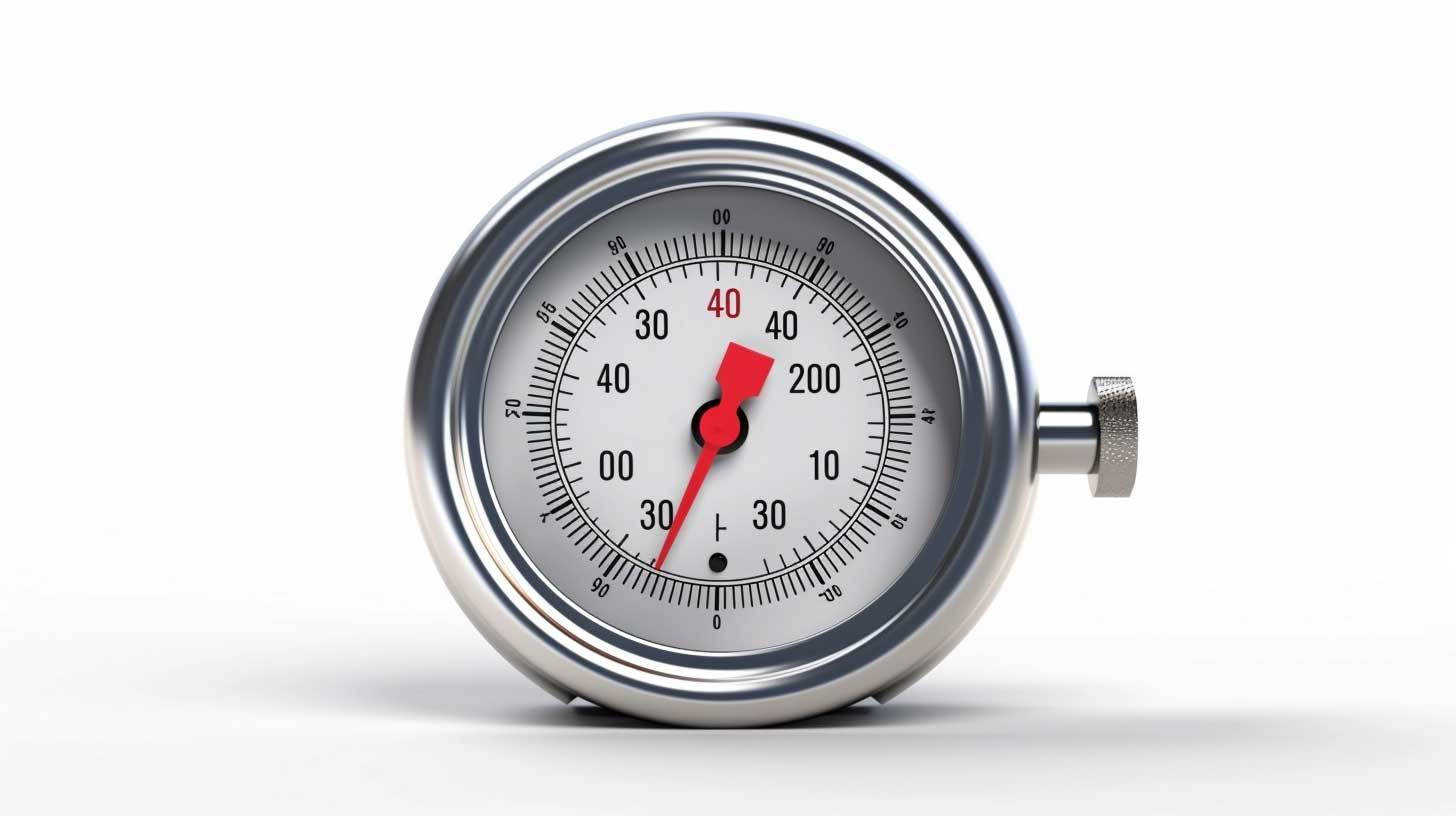
Benefits of Proper Temperature Control
Proper temperature control not only ensures the quality of the molded product but also helps to reduce the cycle time of the molding process, thereby increasing efficiency. The molded product will be of high quality and meet the required standards when temperature control is maintained correctly.
Tips for Ensuring Molding Quality and Efficiency
Manufacturing high-quality molded products using warm isostatic press (WIP) requires careful attention to detail and adherence to specific guidelines. Here are some essential tips for ensuring molding quality and efficiency with WIP:
Choose the Right Type of WIP
The first and most important tip is to choose the right type of WIP for your specific molding project. The WIP should have the right pressure and temperature controls to ensure optimal molding conditions. Make sure to consider factors such as the size and shape of the product, the type of material being molded, and the required molding pressure and temperature.
Prepare the Materials Properly
Proper preparation of the materials is crucial to ensure successful molding. This includes ensuring that the materials are clean and free from any contaminants, as well as keeping them at the appropriate temperature and pressure levels during the molding process. Any impurities or inconsistencies in the materials can affect the quality of the final product.
Monitor the Molding Process Closely
It is also important to monitor the molding process closely to ensure that the materials are being molded correctly and to make any necessary adjustments. This includes checking the pressure and temperature levels regularly and making sure that the product is being molded to the desired shape and size. Any deviations from the desired outcome should be addressed immediately.
Regular Maintenance and Cleaning of the WIP
Finally, regular maintenance and cleaning of the WIP is essential to ensure it is functioning properly and producing high-quality molded products consistently. This includes cleaning the mold and the chamber regularly to prevent the buildup of contaminants and ensuring that all parts are functioning correctly. Any malfunctions or defects should be addressed immediately to prevent any damage to the product or the equipment.
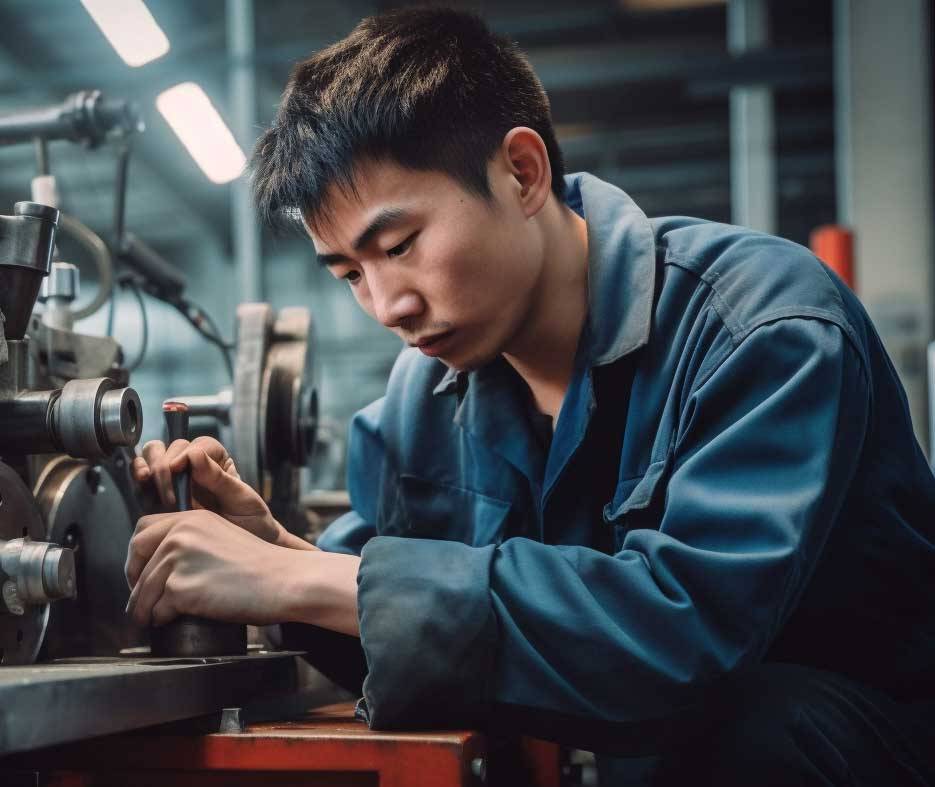
In conclusion, by following these tips, manufacturers can ensure that their WIP is operating at maximum efficiency and producing high-quality molded products consistently. Proper preparation of materials, close monitoring of the molding process, and regular maintenance and cleaning of the equipment are essential to achieving optimal results. Choosing the right type of WIP for the specific molding project is also critical to ensuring molding quality and efficiency.
Conclusion
In conclusion, Warm Isostatic Press (WIP) is an efficient and reliable method for molding high-quality monolithic multilayer ceramics and powder metallurgy (PM) forming process. The operating temperature range of WIP is between 200 and 1400°C, and proper temperature control is crucial for molding quality. WIP comes with various benefits such as uniform densification, improved mechanical properties, and better surface finish. By following the tips for ensuring molding quality and efficiency, WIP can help manufacturers achieve their desired product quality and reduce production costs.
CONTACT US FOR A FREE CONSULTATION
KINTEK LAB SOLUTION's products and services have been recognized by customers around the world. Our staff will be happy to assist with any inquiry you might have. Contact us for a free consultation and talk to a product specialist to find the most suitable solution for your application needs!