Introduction
Table of Contents
In the world of manufacturing, one technique that has gained significant popularity is Zirconia Ceramic Cold Isostatic Pressing (CIP). But what exactly is CIP? Well, it's a process that involves applying high-pressure fluid or gas to shape and form ceramic materials. Imagine a high-pressure pump working its magic to create isotropic uniform pressure on a material. This technique is particularly useful when it comes to pressing parts with complex shapes. So, let's dive deeper into the world of CIP and explore its various applications and advantages.
The Concept of Isostatic Pressing
Explanation of isostatic pressing (CIP)
Isostatic pressing, also known as cold isostatic pressing (CIP), is a method used to compact powdered materials into a solid homogeneous mass before machining or sintering. It involves applying equal pressure from all directions to the powder mixture, which is enclosed within a flexible membrane or hermetic container. This pressure reduces the porosity of the powder mixture and helps create a dense and uniform product.
Application of static pressure produced by fluid or gas
Isostatic pressing utilizes the static pressure produced by a fluid or gas to compact the powder mixture. The powder is placed in a high-pressure container, and the incompressible nature of the liquid or gas medium allows for uniform transfer of pressure from all directions. This ensures that the powder is uniformly pressurized and of the same size in all directions.
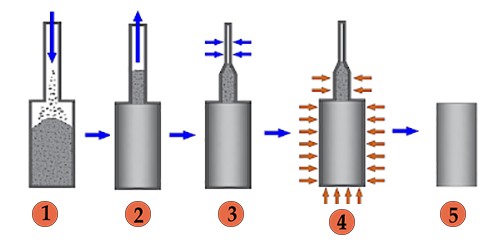
Action of high-pressure pump
To generate the necessary pressure, a high-pressure pump is used to pump the liquid or gas medium into the pressure vessel. According to the principles of fluid mechanics, the pressure is constant and uniformly transferred to all directions. This ensures that the powder in the high-pressure container is uniformly pressurized.
Pressure applied by isotropic uniform pressure
The pressure applied in isostatic pressing is isotropic, meaning it is uniform in all directions. This uniform pressure ensures that the powder is compacted evenly and that the final product has consistent density and dimensions. Isostatic pressing can provide isotropic, ultra-high molding pressure for products, making it suitable for various applications.
Isostatic pressing, specifically cold isostatic pressing (CIP), is a versatile and effective method for compacting powdered materials into solid components. It allows for the production of dense and uniform products, and it is widely used in industries such as medical, aerospace, and automotive manufacturing. The use of all-around pressure in isostatic pressing sets it apart from other powder processing techniques and offers unique benefits for ceramic and refractory applications.
Usage of Isostatic Pressing Technology
Production of new alloy products
Isostatic pressing technology can be used to produce new alloy products that are difficult to be produced by casting technology. This process allows for the creation of complex shapes and ensures uniform compaction of the powder, resulting in high billet strength and uniform density distribution. Isostatic pressing is particularly suited for the manufacturing of pistons, cylinders, tubes, sleeves, seats in aluminium oxide (alumina) and Y-TZP zirconium oxide (zirconia) ceramics in medium to large quantities.
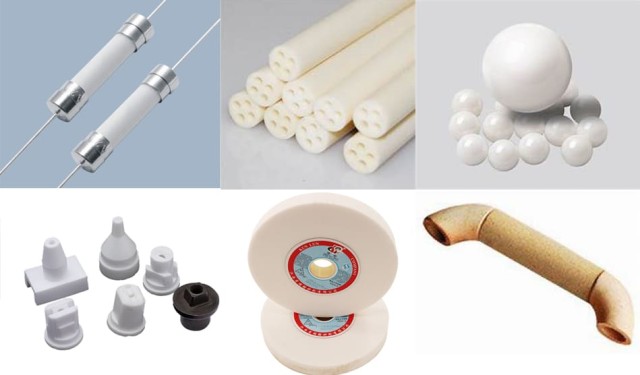
Formation process for zirconia ceramic and alumina ceramic products
Isostatic pressing technology is a very good forming process for zirconia ceramic products and alumina ceramic products with high performance and strength requirements. It ensures the uniform transfer of pressure from all directions, resulting in a uniform density distribution and high billet strength. This process is commonly used for the production of wear-resistant ceramic blanks and large size ZTA products.
Ability to press parts with complex shapes
Isostatic pressing technology enables the pressing of parts with concave, hollow, slender, and other complex shapes. The all-around pressure exerted by the fluid during isostatic pressing manufacture provides uniform compaction of the powder and ensures a uniform density within the compacted part. This process is widely used in the automotive, healthcare, aerospace, and defense industries, where the demand for low-penetrability material in 3D printed parts is high.
Isostatic pressing offers several advantages, including the ability to achieve high and uniform density, the capability to produce parts with precise tolerances, and the opportunity to work with difficult-to-compact and expensive materials. It is a versatile manufacturing process that has found applications in various industries, including ceramics, metals, composites, plastics, and carbon.
Advantages of Isostatic Pressing
Low friction loss and forming pressure
Isostatic pressing allows powder to be compacted with the same pressure in all directions, resulting in low friction loss and uniform density. Unlike other pressing methods, isostatic pressing does not require the use of lubricant, which further contributes to achieving high and uniform density. This advantage makes isostatic pressing suitable for a wide range of materials, including difficult-to-compact and expensive ones such as superalloys, titanium, tool steels, stainless steel, and beryllium.
Uniform pressure transfer and density distribution
The all-around pressure exerted by the fluid during isostatic pressing ensures uniform compaction of the powder and uniform density within the compacted part. This is a significant advantage compared to conventional processing methods, especially for parts with complex geometries. Isostatic pressing eliminates many of the constraints imposed by rigid dies and allows for the production of parts with consistent density distribution.
High billet strength
Isostatic pressing results in high billet strength due to the uniform density achieved throughout the compacted part. The absence of friction loss and the equal pressure applied from all directions contribute to the enhanced strength and structural integrity of the billet. This advantage is particularly beneficial for applications that require strong and durable components.
Cost-effectiveness of the mold
Isostatic pressing offers cost-effectiveness in terms of mold utilization. The process allows for efficient material utilization, especially for expensive materials. With isostatic pressing, there is minimal waste, as the powder is compacted uniformly, reducing the need for excess material. This advantage leads to cost savings and improved efficiency in production.
Isostatic pressing is a versatile and advantageous method for compacting powders and producing high-quality components. Its unique characteristics, such as low friction loss, uniform pressure transfer, high billet strength, and cost-effective mold utilization, make it a preferred choice for various industries and applications.
Conclusion
In conclusion, understanding the process of zirconia ceramic cold isostatic pressing (CIP) can greatly benefit businesses in various industries. This technology offers several advantages, such as low friction loss and forming pressure, uniform pressure transfer and density distribution, high billet strength, and cost-effectiveness of the mold. With the ability to produce new alloy products and form parts with complex shapes, isostatic pressing is a valuable tool for manufacturers. By harnessing the power of isostatic pressing, businesses can enhance their production capabilities and achieve superior quality in their ceramic products.
If you are interested in this product you can browse our company website: https://kindle-tech.com/product-categories/isostatic-press, we understand that every customer's needs are unique. Therefore, we offer a flexible customisation service to meet your specific requirements. Whether it is the specification, functionality or design of the equipment, we are able to personalise it to suit your needs. Our dedicated team will work closely with you to ensure that the customised solution will perfectly meet your experimental needs.
CONTACT US FOR A FREE CONSULTATION
KINTEK LAB SOLUTION's products and services have been recognized by customers around the world. Our staff will be happy to assist with any inquiry you might have. Contact us for a free consultation and talk to a product specialist to find the most suitable solution for your application needs!