Yes, cast iron can be remelted. Cast iron is a recyclable material, and remelting is a common practice in foundries to reuse scrap cast iron or to reform it into new products. The process involves melting the cast iron in a furnace at high temperatures (typically between 1,150°C to 1,400°C, depending on the type of cast iron) and then pouring it into molds to create new castings. However, the remelting process requires careful control of temperature and composition to maintain the desired mechanical properties of the cast iron.
Key Points Explained:
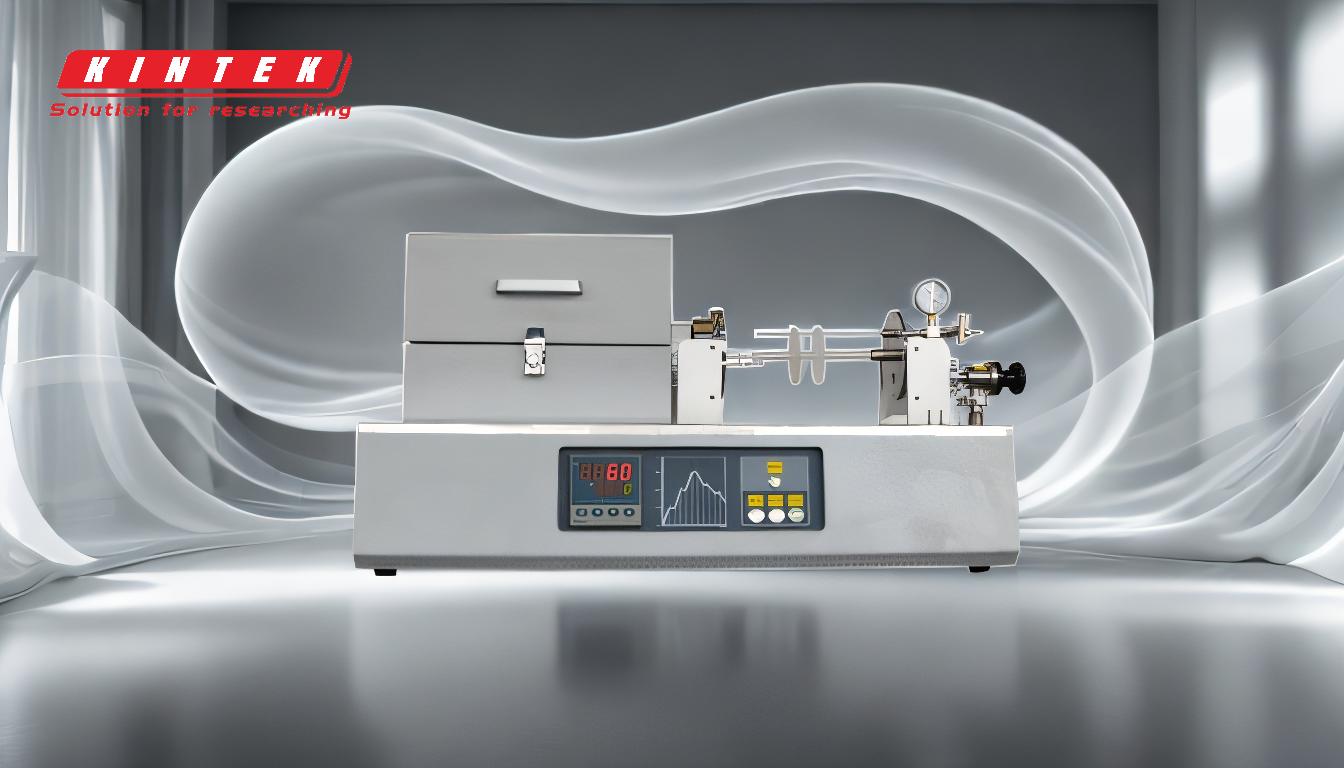
-
Recyclability of Cast Iron
- Cast iron is highly recyclable due to its composition and properties. It can be melted down and reused multiple times without significant degradation of its mechanical properties.
- Foundries often collect scrap cast iron from old machinery, pipes, or other components to remelt and reuse in new castings.
-
Melting Process
- Remelting cast iron requires heating it to temperatures between 1,150°C and 1,400°C, depending on the specific type of cast iron (e.g., gray iron, ductile iron, or white iron).
- Furnaces used for remelting include cupola furnaces, induction furnaces, and electric arc furnaces, each suited for different scales of operation and types of cast iron.
-
Composition Control
- During remelting, the chemical composition of the cast iron must be carefully monitored and adjusted. Elements like carbon, silicon, and manganese play critical roles in determining the final properties of the cast iron.
- Alloying elements may be added to achieve specific mechanical properties, such as increased hardness or tensile strength.
-
Mechanical Properties After Remelting
- Properly remelted cast iron retains its key mechanical properties, such as hardness, tensile strength, and castability.
- However, impurities or improper melting conditions can lead to defects like porosity, reduced ductility, or uneven hardness.
-
Applications of Remelted Cast Iron
- Remelted cast iron is used in a wide range of applications, including automotive parts, machinery components, pipes, and construction materials.
- The ability to remelt and reuse cast iron makes it a cost-effective and sustainable material for manufacturing.
-
Challenges in Remelting
- One challenge is controlling the carbon content, as excessive carbon can lead to brittleness, while insufficient carbon can reduce hardness.
- Another challenge is managing impurities, which can accumulate during repeated remelting cycles and affect the quality of the final product.
-
Environmental and Economic Benefits
- Remelting cast iron reduces the need for virgin materials, lowering production costs and minimizing environmental impact.
- It also aligns with circular economy principles by promoting the reuse of materials and reducing waste.
By understanding these key points, a purchaser of cast iron equipment or consumables can make informed decisions about sourcing and using remelted cast iron, ensuring quality and sustainability in their applications.
Summary Table:
Key Aspect | Details |
---|---|
Recyclability | Highly recyclable; can be reused multiple times without losing properties. |
Melting Temperature | 1,150°C to 1,400°C, depending on type (gray, ductile, or white iron). |
Furnace Types | Cupola, induction, and electric arc furnaces. |
Composition Control | Carbon, silicon, and manganese levels must be carefully monitored. |
Applications | Automotive parts, machinery, pipes, and construction materials. |
Challenges | Managing carbon content and impurities during remelting. |
Environmental Benefits | Reduces need for virgin materials and promotes sustainability. |
Interested in sustainable cast iron solutions? Contact us today to learn more!