Hydrogen can indeed be used in furnaces, and it is gaining attention as a cleaner alternative to traditional fossil fuels like natural gas. When hydrogen combusts, it produces only water vapor as a byproduct, making it an environmentally friendly option. However, there are challenges to consider, such as the need for specialized equipment to handle hydrogen safely, potential modifications to existing furnace designs, and the cost of hydrogen production. Despite these hurdles, hydrogen is increasingly being explored for industrial heating applications due to its potential to reduce carbon emissions and align with global sustainability goals.
Key Points Explained:
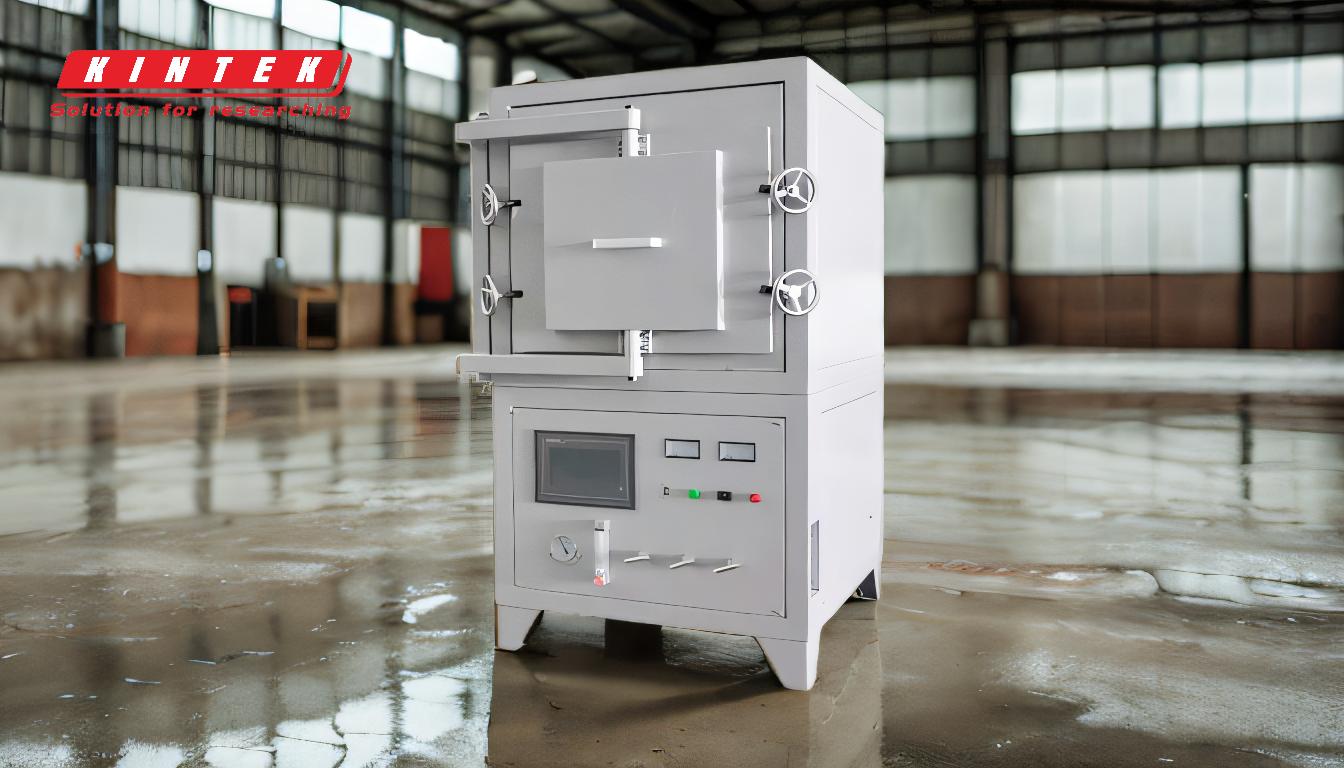
-
Hydrogen as a Clean Fuel:
- Hydrogen combustion produces only water vapor, making it a zero-emission fuel when burned. This is a significant advantage over fossil fuels, which release carbon dioxide and other pollutants.
- The use of hydrogen in furnaces can help industries reduce their carbon footprint and comply with stricter environmental regulations.
-
Challenges in Using Hydrogen:
- Safety Concerns: Hydrogen is highly flammable and requires specialized handling and storage systems to prevent leaks and explosions.
- Infrastructure Modifications: Existing furnace designs may need to be retrofitted or replaced to accommodate hydrogen, as it burns at a higher temperature and has different combustion properties compared to natural gas.
- Cost of Production: Currently, most hydrogen is produced through steam methane reforming, which is not environmentally friendly. Green hydrogen, produced via electrolysis using renewable energy, is cleaner but more expensive.
-
Applications in Industrial Furnaces:
- Hydrogen is being tested and used in various industrial heating processes, such as steel production, glass manufacturing, and heat treatment.
- In steelmaking, hydrogen can replace coke in blast furnaces, significantly reducing carbon emissions.
- In glass manufacturing, hydrogen burners can provide the high temperatures needed for melting raw materials without emitting CO2.
-
Technological Advancements:
- Research is ongoing to develop more efficient and cost-effective methods for hydrogen production, storage, and utilization in furnaces.
- Innovations in burner technology and furnace design are making it easier to integrate hydrogen into existing systems.
-
Environmental and Economic Benefits:
- Switching to hydrogen can help industries meet sustainability targets and reduce reliance on fossil fuels.
- While the initial investment in hydrogen infrastructure may be high, the long-term benefits of reduced emissions and potential government incentives can offset these costs.
In conclusion, hydrogen holds great promise as a fuel for furnaces, offering a cleaner and more sustainable alternative to traditional fuels. However, its widespread adoption will depend on overcoming technical and economic challenges, as well as continued advancements in hydrogen production and utilization technologies.
Summary Table:
Aspect | Details |
---|---|
Hydrogen as a Clean Fuel | Produces only water vapor, zero emissions, and reduces carbon footprint. |
Challenges | Safety concerns, infrastructure modifications, and high production costs. |
Applications | Steel production, glass manufacturing, and heat treatment. |
Technological Advancements | Innovations in production, storage, and burner technology. |
Benefits | Environmental sustainability, reduced emissions, and long-term cost savings. |
Ready to explore hydrogen-powered furnaces for your industry? Contact us today to learn more!