Brazing copper to brass without flux is technically possible but not recommended due to the challenges involved. Flux is typically used to remove oxides and improve the wetting and flow of the filler metal. Without flux, achieving a strong and reliable joint becomes difficult, especially because both copper and brass oxidize quickly when exposed to heat. However, under specific conditions, such as using a filler metal with self-fluxing properties or in a controlled atmosphere, brazing without flux can be attempted. This requires precise control over the brazing environment and process parameters.
Key Points Explained:
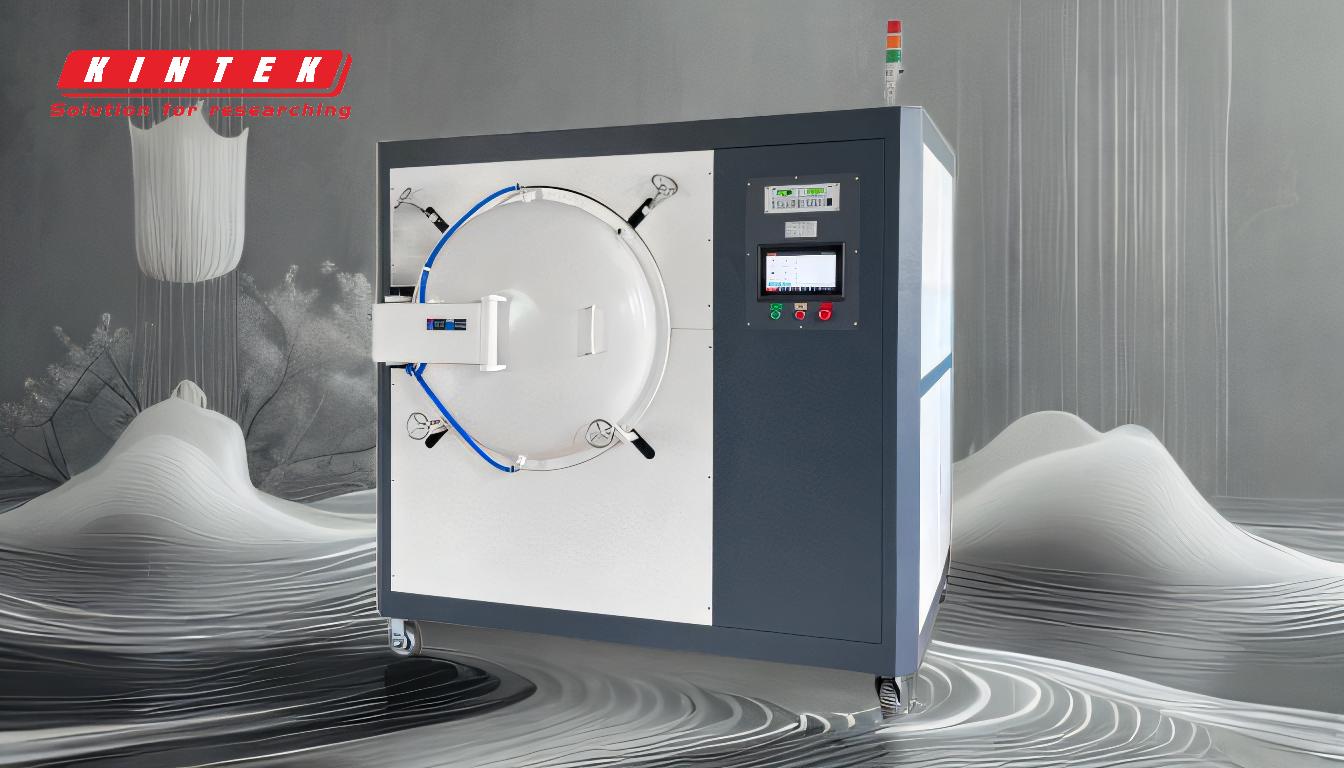
-
Role of Flux in Brazing
- Flux is essential in brazing to remove oxides from the metal surfaces, which form when metals are heated.
- It also promotes the wetting and flow of the filler metal, ensuring a strong bond.
- Without flux, oxides can prevent the filler metal from adhering properly, leading to weak joints.
-
Challenges of Brazing Without Flux
- Both copper and brass oxidize rapidly when heated, forming a layer that hinders the bonding process.
- The absence of flux increases the risk of incomplete fusion and porosity in the joint.
- Achieving a clean, oxide-free surface without flux requires exceptional control over the brazing environment.
-
Conditions for Fluxless Brazing
- Self-Fluxing Filler Metals: Some filler metals, like certain phosphorus-containing alloys, have self-fluxing properties that can reduce the need for external flux.
- Controlled Atmospheres: Brazing in an inert gas (e.g., argon or nitrogen) or a vacuum can prevent oxidation, making flux unnecessary.
- Surface Preparation: Thoroughly cleaning the surfaces to remove oxides and contaminants before brazing can improve results.
-
Practical Considerations
- Fluxless brazing is more complex and requires advanced equipment and expertise.
- For most applications, especially in industrial settings, using flux is more reliable and cost-effective.
- Fluxless brazing is typically reserved for specialized applications where flux residues are undesirable.
-
Alternative Methods
- If flux cannot be used, consider using a filler metal with self-fluxing properties or brazing in a controlled atmosphere.
- Pre-treating the surfaces with a chemical cleaning agent can help reduce oxidation.
- Ensure precise temperature control to minimize oxidation during the brazing process.
In summary, while brazing copper to brass without flux is possible under specific conditions, it is generally not recommended due to the increased difficulty and risk of joint failure. Using flux remains the most reliable and practical approach for most applications.
Summary Table:
Aspect | Details |
---|---|
Role of Flux | Removes oxides, improves wetting and flow of filler metal. |
Challenges Without Flux | Rapid oxidation, incomplete fusion, and porosity in joints. |
Fluxless Brazing Conditions | Use self-fluxing filler metals, controlled atmospheres, or clean surfaces. |
Practical Considerations | Requires advanced equipment and expertise; flux is more reliable. |
Alternative Methods | Chemical cleaning, precise temperature control, and specialized techniques. |
Need help with brazing copper to brass? Contact our experts today for tailored solutions!