Yes, thick aluminum can be brazed, but it requires careful consideration of the aluminum alloy type, brazing method, and process parameters. Aluminum alloys are categorized into non-hardenable and hardenable types, with some being more suitable for brazing than others. Non-hardenable alloys like Series 1xxx, 3xxx, and 5xxx (with low magnesium content) and hardenable alloys like Series 6xxx are generally brazable. However, Series 2xxx and 7xxx alloys are typically not brazable due to their low melting points, unless specific conditions are met. Common brazing methods include flame brazing, furnace brazing, inert gas brazing, and vacuum brazing, each suited for different applications and alloy types.
Key Points Explained:
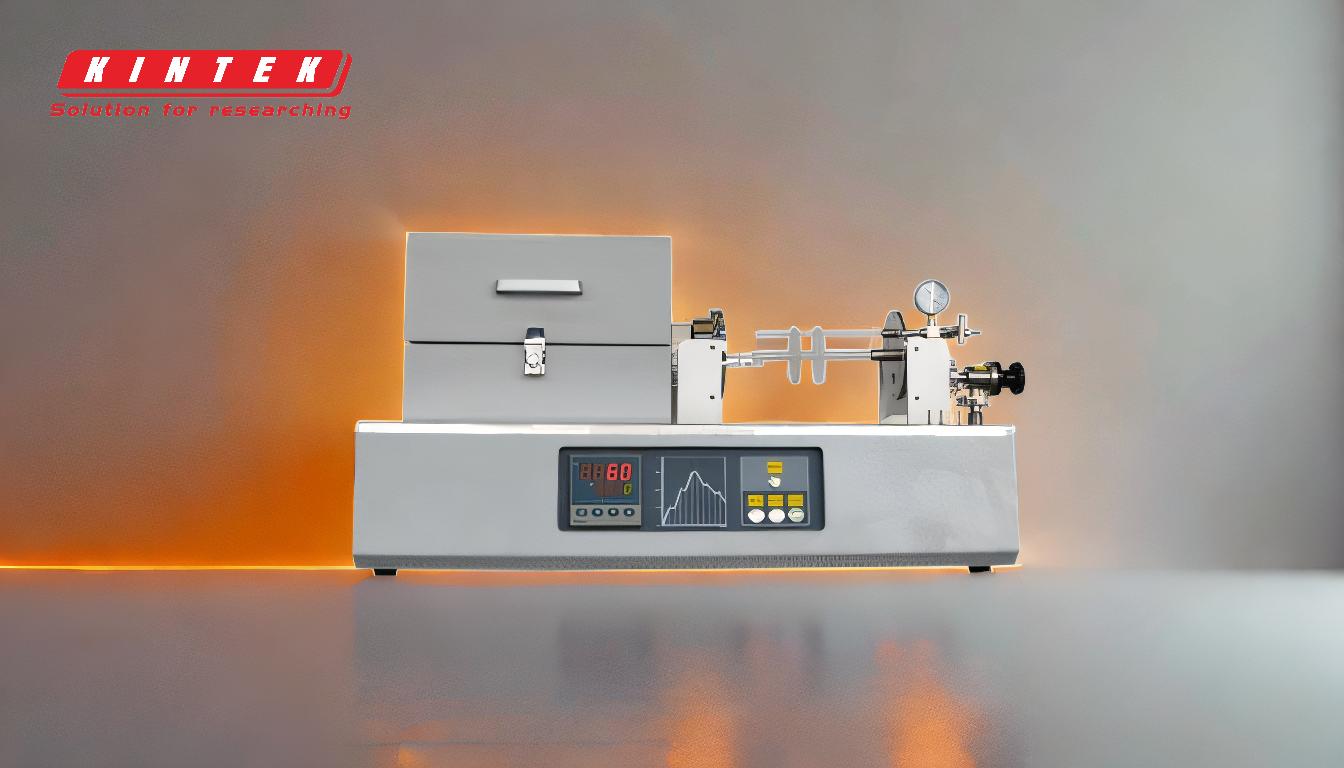
-
Brazing Thick Aluminum:
- Thick aluminum can be brazed, but the process requires proper heat management to ensure uniform heating and avoid warping or incomplete joints. The thickness of the material affects the heat distribution, so preheating or controlled heating rates may be necessary.
-
Suitable Aluminum Alloys:
- Non-hardenable Alloys: Series 1xxx (pure aluminum), 3xxx (aluminum-manganese), and 5xxx (aluminum-magnesium with low magnesium content) are brazable. These alloys have higher melting points and better thermal conductivity, making them easier to braze.
- Hardenable Alloys: Series 6xxx (aluminum-magnesium-silicon) can also be brazed. These alloys are commonly used in structural applications due to their strength and brazability.
- Non-brazable Alloys: Series 2xxx (aluminum-copper) and 7xxx (aluminum-zinc) are generally not brazable because their melting points are too close to the brazing filler metal's melting point, leading to potential melting of the base material.
-
Brazing Methods:
- Flame Brazing: Suitable for localized heating and small-scale applications. It requires precise control of the flame temperature to avoid overheating the aluminum.
- Furnace Brazing: Ideal for large or complex parts. It provides uniform heating and is often used in mass production.
- Inert Gas Brazing: Uses gases like argon or nitrogen to create an oxygen-free environment, preventing oxidation during the brazing process.
- Vacuum Brazing: Suitable for high-precision applications where oxidation must be minimized. It is often used for aerospace components.
-
Challenges with Thick Aluminum:
- Thick aluminum sections require more heat input, which can lead to uneven heating and thermal stress. Preheating and controlled cooling rates are essential to avoid distortion.
- The thermal conductivity of aluminum can cause heat to dissipate quickly, making it challenging to achieve the required brazing temperature.
-
Filler Metals and Fluxes:
- Aluminum brazing typically uses aluminum-silicon filler metals, which have melting points lower than the base material. Fluxes are used to remove oxides and improve wetting of the filler metal.
-
Post-Brazing Considerations:
- After brazing, it is essential to clean the joint to remove any residual flux, which can cause corrosion. Proper cooling and stress relief may also be required to ensure the integrity of the joint.
In summary, brazing thick aluminum is feasible but requires careful selection of the alloy, brazing method, and process parameters. Proper heat management, suitable filler metals, and post-brazing treatments are critical to achieving strong, durable joints.
Summary Table:
Key Aspect | Details |
---|---|
Suitable Alloys | 1xxx, 3xxx, 5xxx (low Mg), 6xxx |
Non-brazable Alloys | 2xxx, 7xxx (low melting points) |
Brazing Methods | Flame, Furnace, Inert Gas, Vacuum |
Challenges | Heat management, thermal stress, uneven heating |
Filler Metals | Aluminum-silicon with fluxes for oxide removal |
Post-Brazing | Clean joints, proper cooling, stress relief |
Need expert advice on brazing thick aluminum? Contact us today for tailored solutions!