Heat treatment is a critical process in metallurgy, used to enhance the mechanical properties of metals such as hardness, strength, toughness, and ductility. However, overheating during heat treatment can lead to detrimental effects, including grain growth, loss of mechanical properties, and even structural failure. Overheating occurs when the metal is exposed to temperatures beyond its optimal range, causing excessive diffusion and undesirable microstructural changes. This can result in reduced performance, cracking, or warping. Proper control of temperature, time, and cooling rates is essential to achieve the desired properties without compromising the metal's integrity.
Key Points Explained:
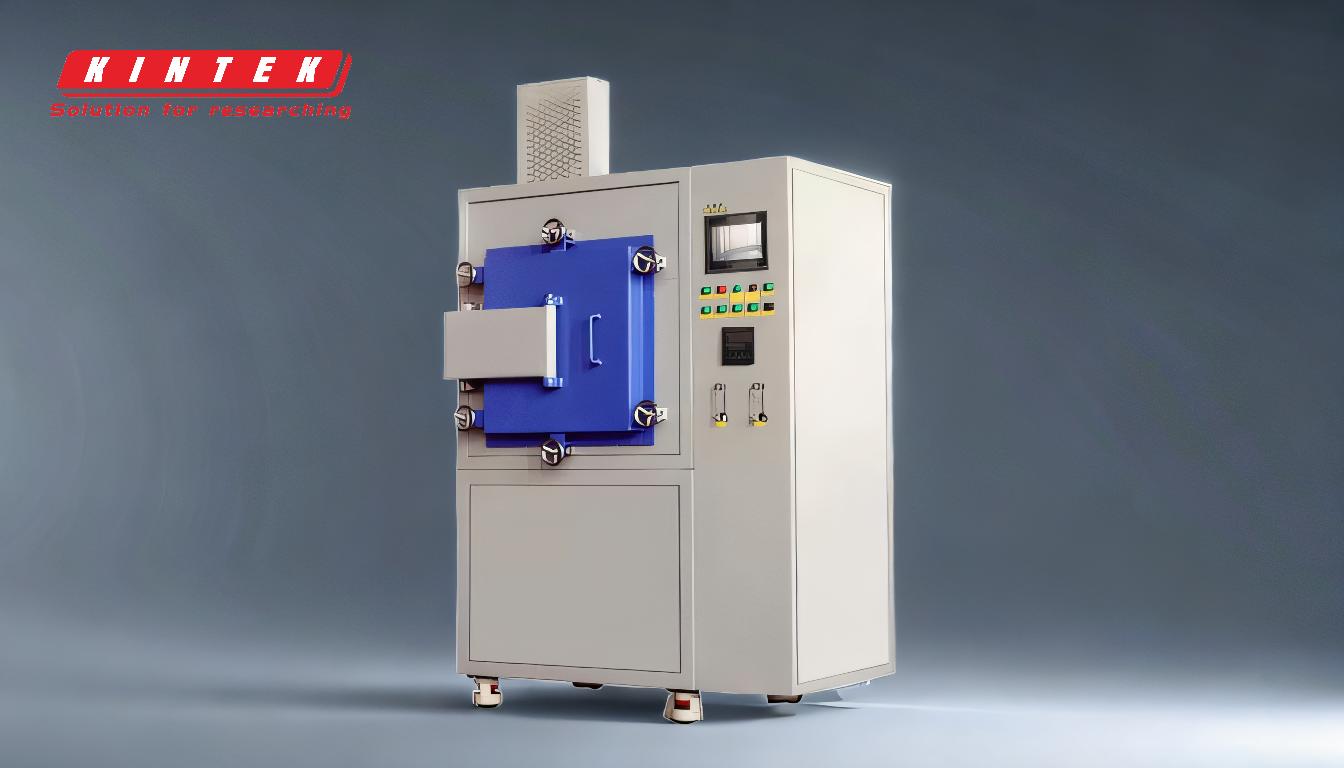
-
Understanding Heat Treatment and Its Goals:
- Heat treatment involves heating and cooling metals to alter their microstructure and mechanical properties.
- The primary goals are to improve hardness, strength, toughness, ductility, and elasticity.
- Processes like annealing, quenching, tempering, and case hardening are commonly used.
-
The Risks of Overheating During Heat Treatment:
- Overheating occurs when metals are exposed to temperatures higher than recommended for their specific alloy and treatment process.
- Excessive heat can cause grain growth, leading to a coarse microstructure that weakens the metal.
- Overheating can also result in oxidation, decarburization, or even melting, depending on the metal and temperature.
-
Effects of Overheating on Metal Properties:
- Loss of Mechanical Strength: Overheating can reduce the metal's tensile strength, making it more prone to failure under stress.
- Reduced Toughness and Ductility: Excessive heat can make the metal brittle, reducing its ability to absorb energy or deform without breaking.
- Warping and Cracking: Uneven heating or cooling can cause distortion or cracking, especially in complex shapes or thin sections.
-
Factors Contributing to Overheating:
- Incorrect Temperature Settings: Using temperatures outside the recommended range for a specific alloy or process.
- Prolonged Exposure: Keeping the metal at high temperatures for too long, even if within the recommended range, can lead to overheating.
- Poor Heat Distribution: Uneven heating in furnaces or during localized treatments can cause hotspots and overheating in certain areas.
-
Preventing Overheating During Heat Treatment:
- Accurate Temperature Control: Use precise thermocouples and controllers to maintain the correct temperature.
- Proper Timing: Follow recommended heating and cooling schedules to avoid prolonged exposure.
- Uniform Heating: Ensure even heat distribution in the furnace or during localized treatments.
- Monitoring and Testing: Regularly inspect the microstructure and mechanical properties to detect signs of overheating early.
-
Real-World Implications of Overheating:
- In industries like aerospace and automotive, overheating can compromise the safety and performance of critical components.
- Overheated parts may fail prematurely, leading to costly repairs, recalls, or accidents.
- Proper heat treatment is essential for ensuring the longevity and reliability of metal components.
-
Recovery from Overheating:
- If overheating is detected early, the metal can sometimes be re-treated to restore its properties.
- However, severe overheating may render the metal unusable, requiring replacement.
- Preventive measures are always more cost-effective than attempting to recover from overheating.
By understanding the risks and implementing proper controls, overheating during heat treatment can be avoided, ensuring that metals achieve their desired properties without compromising their structural integrity.
Summary Table:
Key Aspect | Details |
---|---|
Risks of Overheating | Grain growth, loss of mechanical properties, warping, cracking, and failure. |
Effects on Metal | Reduced strength, toughness, and ductility; increased brittleness. |
Prevention Strategies | Accurate temperature control, proper timing, uniform heating, and testing. |
Real-World Implications | Compromised safety, premature failure, and costly repairs in industries. |
Recovery from Overheating | Early detection allows re-treatment; severe cases may require replacement. |
Ensure your heat treatment processes are safe and effective—contact our experts today for guidance!