Yes, stainless steel can be PVD (Physical Vapor Deposition) coated. PVD coating is a versatile and environmentally friendly process that involves depositing a thin, durable layer of material onto a substrate, such as stainless steel, in a vacuum chamber. This process enhances the properties of stainless steel, including hardness, wear resistance, corrosion resistance, and aesthetic appeal. PVD coatings are widely used in industries such as aerospace, automotive, medical, and industrial tools due to their ability to improve the performance and longevity of components.
Key Points Explained:
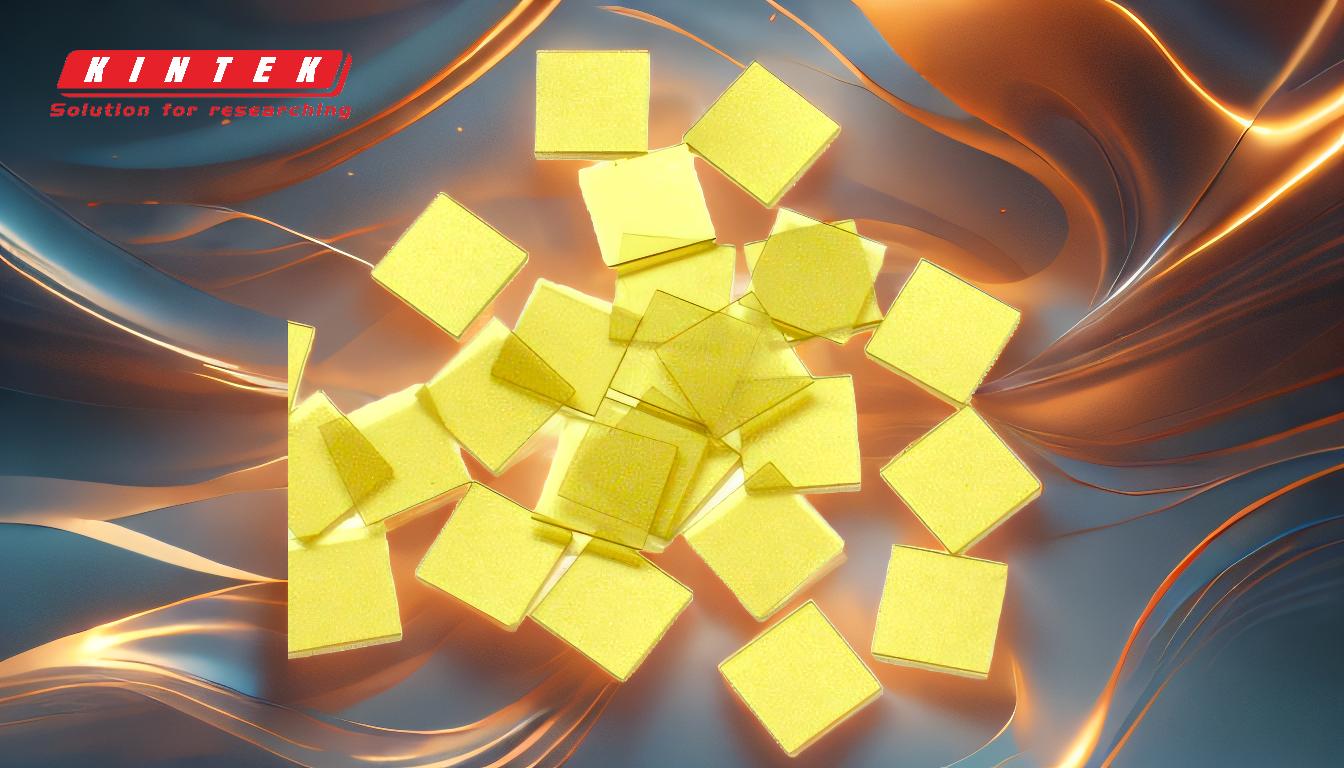
1. PVD Coating Process Overview
- Definition: PVD coating is a thin-film deposition process that occurs in a vacuum chamber. It involves vaporizing a solid material (target) and depositing it atom by atom onto a substrate (e.g., stainless steel).
-
Steps:
- Ablation: The target material is vaporized using methods like sputtering or evaporation.
- Transport: The vaporized material is transported through the vacuum chamber.
- Reaction: The material may react with gases (e.g., nitrogen or oxygen) to form compounds like nitrides or oxides.
- Deposition: The material is deposited onto the substrate, forming a thin, uniform layer.
-
Advantages:
- Environmentally friendly compared to traditional plating methods.
- Produces a highly adherent, pure, and durable coating.
2. Why Stainless Steel is Suitable for PVD Coating
- Surface Preparation: Stainless steel must be thoroughly cleaned before PVD coating to ensure proper adhesion. This involves removing contaminants like oils, oxides, and residues.
- Compatibility: Stainless steel’s smooth and stable surface makes it an ideal substrate for PVD coatings. The coating bonds well with the steel, creating a strong interpenetrating layer that resists flaking or chipping.
- Enhanced Properties: PVD coatings improve stainless steel’s hardness, wear resistance, and corrosion resistance, making it suitable for demanding applications.
3. Applications of PVD-Coated Stainless Steel
- Aerospace: Used for components requiring high hardness and oxidation resistance, such as turbine blades and engine parts.
- Automotive: Enhances the durability and aesthetics of parts like wheels, pistons, and decorative trims.
- Medical: Applied to surgical tools and implants to improve biocompatibility, corrosion resistance, and wear resistance.
- Industrial Tools: Used for cutting tools, dies, and molds to extend their lifespan and performance.
- Firearms: Provides corrosion resistance and durability for gun components.
4. Benefits of PVD Coating on Stainless Steel
- Improved Hardness: PVD coatings like titanium nitride (TiN) or chromium nitride (CrN) significantly increase surface hardness.
- Enhanced Wear Resistance: The coating protects against abrasion and friction, extending the lifespan of components.
- Corrosion Resistance: PVD coatings act as a barrier, preventing oxidation and chemical attack.
- Aesthetic Appeal: PVD coatings can produce a variety of colors (e.g., gold, black, or bronze) for decorative purposes.
- Environmentally Friendly: PVD is a cleaner alternative to chrome plating, as it does not produce hazardous waste.
5. Types of PVD Coatings for Stainless Steel
- Titanium Nitride (TiN): Provides a gold-colored coating with high hardness and wear resistance.
- Chromium Nitride (CrN): Offers excellent corrosion resistance and a silver-gray appearance.
- Zirconium Nitride (ZrN): Known for its golden color and high-temperature stability.
- Diamond-Like Carbon (DLC): Provides a black coating with exceptional hardness and low friction.
- Titanium Aluminum Nitride (TiAlN): Used for high-temperature applications due to its oxidation resistance.
6. Considerations for PVD Coating Stainless Steel
- Surface Finish: The quality of the PVD coating depends on the surface finish of the stainless steel. A polished surface yields a smoother and more uniform coating.
- Thickness: PVD coatings are typically 1-5 microns thick, providing a balance between performance and cost.
- Temperature Sensitivity: Stainless steel must withstand the high temperatures (200-500°C) used in the PVD process without losing its structural integrity.
- Cost: While PVD coating is more expensive than some traditional methods, its long-term benefits often justify the investment.
7. Comparison with Other Coating Methods
- Chrome Plating: PVD is more environmentally friendly and produces a thinner, more uniform coating.
- Electroplating: PVD offers better adhesion and durability, with no risk of hydrogen embrittlement.
- Anodizing: PVD provides a wider range of colors and better wear resistance.
8. Longevity and Durability
- PVD coatings can extend the lifespan of stainless steel components by up to ten times, depending on the application.
- The coatings are highly resistant to wear, corrosion, and environmental factors, making them suitable for long-term use in harsh conditions.
In summary, PVD coating is an excellent option for enhancing the properties of stainless steel, offering improved hardness, wear resistance, corrosion resistance, and aesthetic appeal. Its versatility and environmental benefits make it a preferred choice for industries ranging from aerospace to medical devices.
Summary Table:
Aspect | Details |
---|---|
Process Overview | Thin-film deposition in a vacuum chamber, creating durable, adherent layers. |
Key Benefits | Improved hardness, wear resistance, corrosion resistance, and aesthetics. |
Applications | Aerospace, automotive, medical, industrial tools, and firearms. |
Coating Types | TiN, CrN, ZrN, DLC, TiAlN. |
Environmental Impact | Cleaner and more eco-friendly than traditional plating methods. |
Upgrade your stainless steel components with PVD coating—contact us today to learn more!