Annealing, particularly low hydrogen annealing, can indeed influence the yield strength of materials, but its effect depends on the specific material, temperature, and duration of the process. In the case of X80 pipeline steel, annealing at 200 °C for 12 hours increases the yield strength by approximately 10% while reducing elongation by about 20%. This is attributed to the diffusion of carbon atoms into interstitial sites of dislocations, forming a Cottrell atmosphere that pins dislocations and reduces the density of movable dislocations. However, annealing generally reduces yield strength in many materials by softening them, so its effect varies based on the material and process parameters.
Key Points Explained:
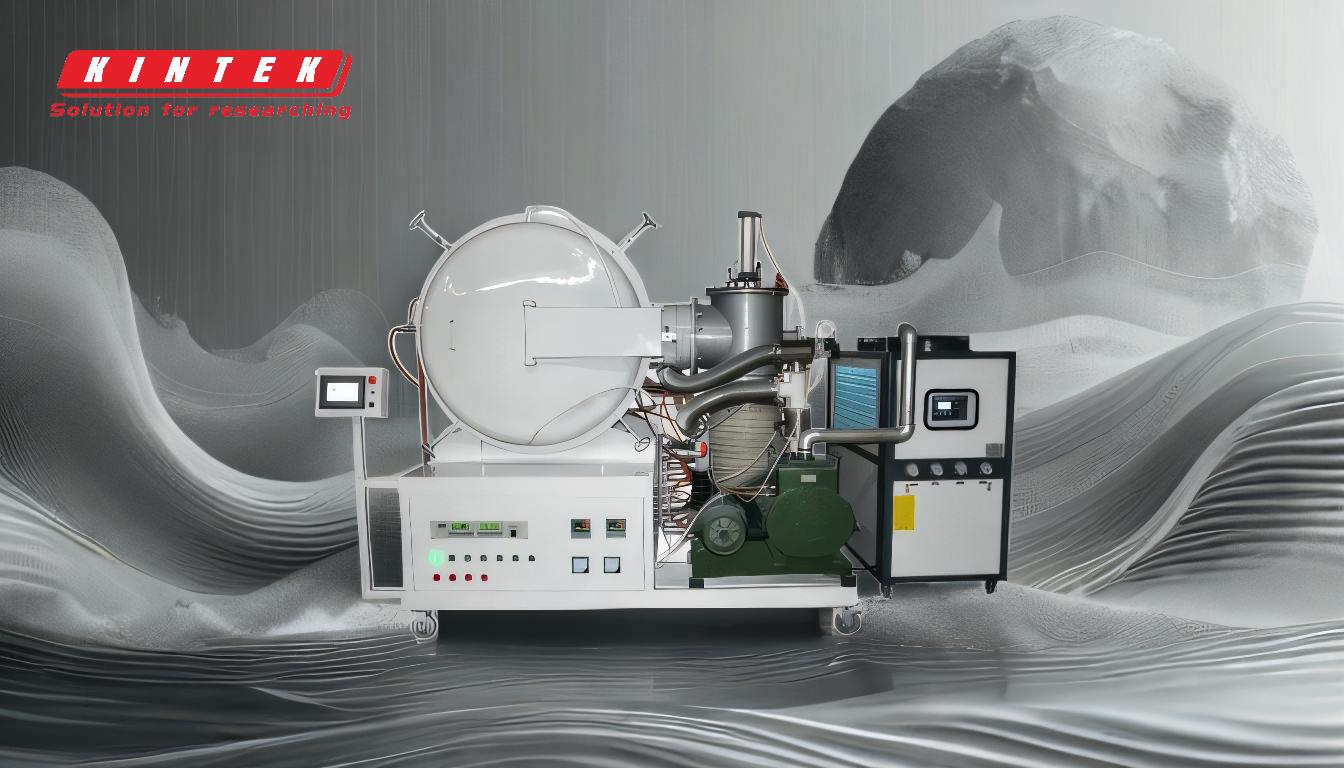
-
Effect of Annealing on Yield Strength:
- Annealing can either increase or decrease yield strength depending on the material and process conditions.
- In the case of X80 pipeline steel, low hydrogen annealing at 200 °C for 12 hours increases yield strength by approximately 10%.
-
Mechanism Behind Yield Strength Increase:
- The increase in yield strength is due to the diffusion of carbon atoms into interstitial sites of dislocations.
- This forms a Cottrell atmosphere, which pins dislocations in place and reduces the density of movable dislocations.
-
Trade-off with Elongation:
- While yield strength increases, elongation decreases by approximately 20%.
- This indicates a trade-off between strength and ductility, which is common in materials processing.
-
General Effects of Annealing:
- Annealing typically softens materials by reducing internal stresses and increasing grain size, which generally lowers yield strength.
- However, specific conditions (like low hydrogen annealing) can lead to localized strengthening effects, as seen in X80 pipeline steel.
-
Material-Specific Outcomes:
- The impact of annealing on yield strength is highly dependent on the material's composition and microstructure.
- For instance, in steels, the presence of carbon and other alloying elements can lead to unique strengthening mechanisms during annealing.
-
Importance of Process Parameters:
- The temperature and duration of annealing are critical factors.
- In the example provided, 200 °C for 12 hours is a specific condition that leads to the observed changes in mechanical properties.
-
Applications in Industry:
- Understanding the effects of annealing on yield strength is crucial for industries like pipeline manufacturing, where materials must balance strength and ductility.
- Tailoring annealing processes can optimize material properties for specific applications.
In summary, annealing can increase yield strength under specific conditions, such as low hydrogen annealing in X80 pipeline steel, but its effects vary widely depending on the material and process parameters. The interplay between strengthening mechanisms and ductility must be carefully considered in material design and processing.
Summary Table:
Aspect | Details |
---|---|
Effect on Yield Strength | Can increase or decrease depending on material and process conditions. |
Example: X80 Steel | Low hydrogen annealing at 200°C for 12 hours increases yield strength by 10%. |
Mechanism | Carbon diffusion forms Cottrell atmosphere, pinning dislocations. |
Trade-off | Yield strength increases, but elongation decreases by 20%. |
General Effect | Typically softens materials, reducing yield strength. |
Key Factors | Material composition, temperature, and duration of annealing. |
Industrial Application | Crucial for industries like pipeline manufacturing to balance strength and ductility. |
Optimize your material properties with tailored annealing processes—contact our experts today!