Annealing is a heat treatment process that can alter the mechanical properties of steel, but its effect on strength depends on the specific type of annealing and the material being treated. In the case of low hydrogen annealing, it can increase yield strength by pinning dislocations through the formation of a Cottrell atmosphere, but this often comes at the cost of reduced elongation. While annealing can improve certain properties, it does not universally make steel stronger; its impact varies based on the material, annealing conditions, and desired outcomes.
Key Points Explained:
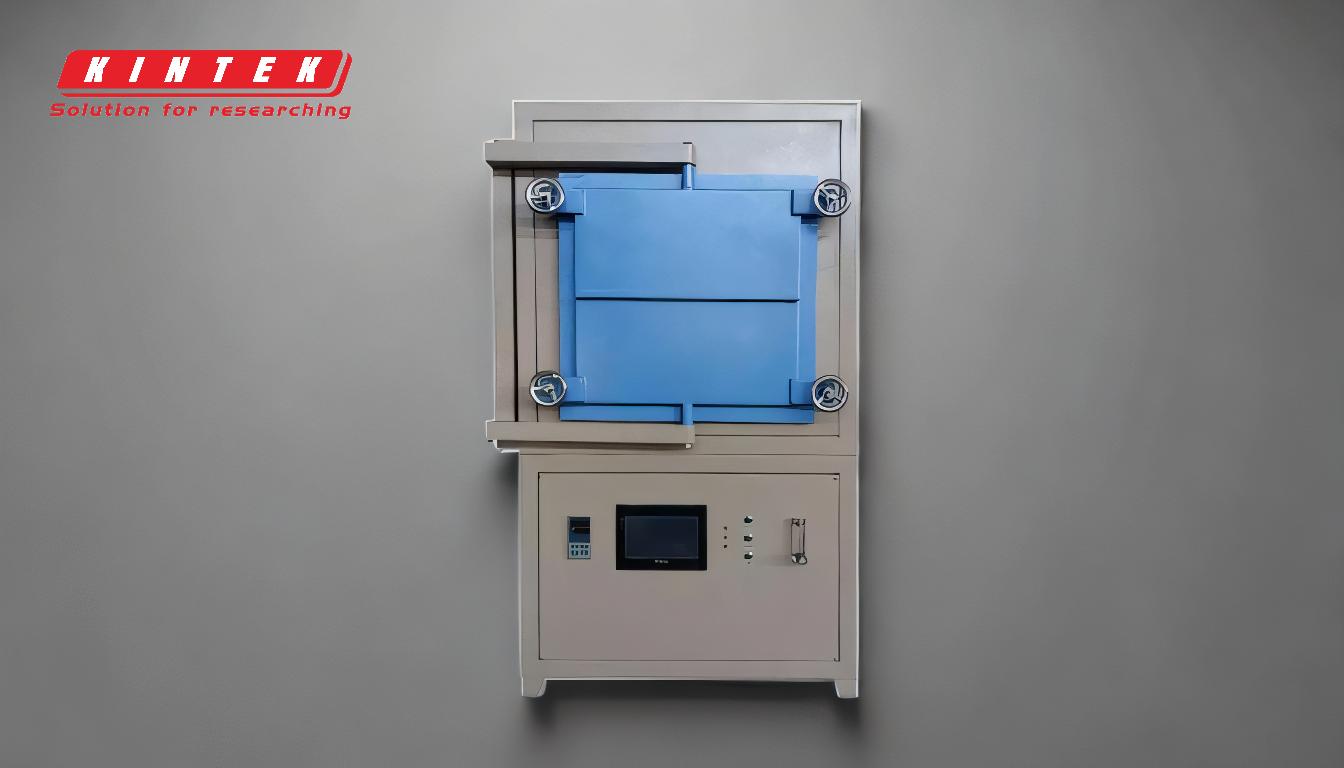
-
What is Annealing?
- Annealing is a heat treatment process that involves heating a material to a specific temperature, holding it at that temperature for a period, and then cooling it slowly. This process is used to relieve internal stresses, refine the grain structure, and improve ductility and toughness.
-
Effect of Low Hydrogen Annealing on Steel
- Low hydrogen annealing, as described in the reference, involves heating steel to a relatively low temperature (e.g., 200 °C) for an extended period (e.g., 12 hours). This process is particularly effective in reducing hydrogen embrittlement, which can weaken steel.
- The reference highlights that annealing at 200 °C for 12 hours increases the yield strength of X80 pipeline steel by approximately 10%. This is due to the diffusion of carbon atoms into interstitial sites of dislocations, forming a Cottrell atmosphere. This atmosphere pins dislocations, making it harder for them to move and thereby increasing yield strength.
-
Trade-offs in Mechanical Properties
- While low hydrogen annealing increases yield strength, it also reduces elongation by approximately 20%. This trade-off is common in materials science, where improving one property (e.g., strength) often comes at the expense of another (e.g., ductility).
- The reduction in elongation indicates that the material becomes less ductile, which may not be desirable for applications requiring high toughness or the ability to withstand deformation without breaking.
-
Cottrell Atmosphere and Dislocation Pinning
- The formation of a Cottrell atmosphere is a key mechanism in the annealing process described. Carbon atoms diffuse to dislocations and "pin" them in place, reducing the density of movable dislocations. This pinning effect increases the resistance to deformation, thereby increasing yield strength.
- However, this also means that the material has fewer dislocations available to accommodate plastic deformation, leading to reduced elongation.
-
Does Annealing Make Steel Stronger?
- The answer depends on the context. In the case of low hydrogen annealing, it can increase yield strength by pinning dislocations, but this is not a universal outcome of all annealing processes.
- Other types of annealing, such as full annealing or process annealing, are typically used to soften steel, improve ductility, and relieve internal stresses, which may result in lower strength but better formability.
-
Applications and Considerations
- Low hydrogen annealing is particularly useful in applications where hydrogen embrittlement is a concern, such as in pipeline steels or high-strength alloys. However, the trade-off between increased strength and reduced ductility must be carefully considered based on the intended use of the material.
- For applications requiring both high strength and good ductility, other heat treatment processes, such as quenching and tempering, might be more appropriate.
In summary, annealing can make steel stronger under specific conditions, such as low hydrogen annealing, but this is not a general rule. The process involves trade-offs in mechanical properties, and its effectiveness depends on the material, annealing parameters, and desired outcomes.
Summary Table:
Aspect | Details |
---|---|
What is Annealing? | Heat treatment process to relieve stress, refine grain structure, and improve ductility. |
Low Hydrogen Annealing | Increases yield strength by ~10% but reduces elongation by ~20%. |
Cottrell Atmosphere | Carbon atoms pin dislocations, increasing strength but reducing ductility. |
Trade-offs | Improved strength often comes at the cost of reduced elongation. |
Applications | Ideal for reducing hydrogen embrittlement in pipeline steels and alloys. |
Want to optimize your steel's properties? Contact our experts today for tailored heat treatment solutions!