Ceramics can break with temperature changes, but their resistance to thermal shock depends on several factors, including their composition, structure, and the rate of temperature change. Ceramics generally have low thermal conductivity and high thermal expansion coefficients, making them prone to cracking under rapid temperature fluctuations. However, certain ceramics, like silicon carbide and alumina, are engineered to withstand thermal shock better due to their specific properties. Understanding the thermal behavior of ceramics is crucial for applications involving temperature variations.
Key Points Explained:
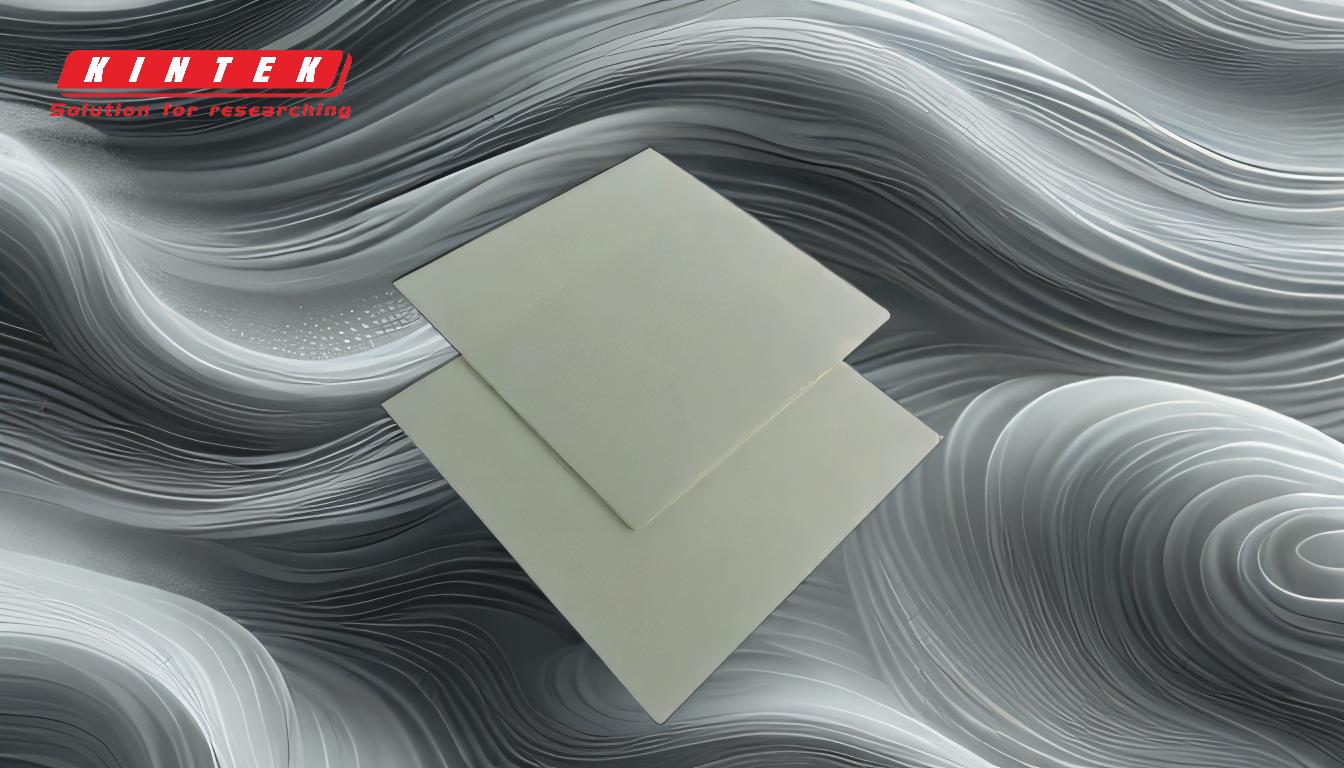
-
Thermal Shock and Ceramics:
- Thermal shock occurs when a material experiences rapid temperature changes, causing uneven expansion or contraction.
- Ceramics are brittle and have low thermal conductivity, meaning they cannot dissipate heat quickly. This makes them susceptible to cracking under rapid temperature changes.
-
Factors Influencing Thermal Shock Resistance:
- Thermal Expansion Coefficient: Materials with lower thermal expansion coefficients are less likely to crack because they expand and contract less with temperature changes.
- Thermal Conductivity: Higher thermal conductivity allows heat to distribute more evenly, reducing stress within the material.
- Material Composition: Certain ceramics, like silicon carbide and alumina, are designed to have better thermal shock resistance due to their unique properties.
-
Examples of Ceramics and Their Thermal Behavior:
- Silicon Carbide (SiC): Known for its excellent thermal shock resistance, SiC is used in high-temperature applications like furnace components.
- Alumina (Al₂O₃): While alumina has moderate thermal shock resistance, it is widely used in industrial applications due to its overall durability.
- Porcelain: Common in household items, porcelain is more prone to cracking under thermal shock due to its higher thermal expansion coefficient.
-
Applications and Considerations:
- In industries like aerospace, automotive, and electronics, ceramics are chosen for their ability to withstand extreme temperatures.
- For applications involving rapid heating or cooling, engineers often select ceramics with high thermal shock resistance or design components to minimize stress.
-
Mitigating Thermal Shock in Ceramics:
- Gradual Temperature Changes: Slower heating or cooling rates reduce the risk of cracking.
- Material Design: Using ceramics with lower thermal expansion and higher thermal conductivity can improve performance.
- Composite Materials: Combining ceramics with other materials can enhance their thermal shock resistance.
By understanding these factors, purchasers and engineers can select the right ceramics for specific applications, ensuring longevity and reliability under varying temperature conditions.
Summary Table:
Factor | Impact on Thermal Shock Resistance |
---|---|
Thermal Expansion Coefficient | Lower coefficients reduce cracking risk by minimizing expansion/contraction during temperature changes. |
Thermal Conductivity | Higher conductivity distributes heat evenly, reducing internal stress. |
Material Composition | Ceramics like silicon carbide and alumina are engineered for better thermal shock resistance. |
Gradual Temperature Changes | Slower heating/cooling rates reduce cracking risk. |
Composite Materials | Combining ceramics with other materials enhances thermal shock resistance. |
Need help selecting ceramics for high-temperature applications? Contact our experts today for tailored solutions!