Electron beams are streams of electrons generated through various methods such as thermionic emission (heat), secondary electron emission (bombardment of charged particles), or field emission (strong electric fields). These methods involve the release of electrons from a material, which are then accelerated and focused into a coherent beam. The choice of method depends on the application, with each technique offering unique advantages in terms of electron energy, beam intensity, and control. Understanding these processes is crucial for applications ranging from scientific research to industrial manufacturing.
Key Points Explained:
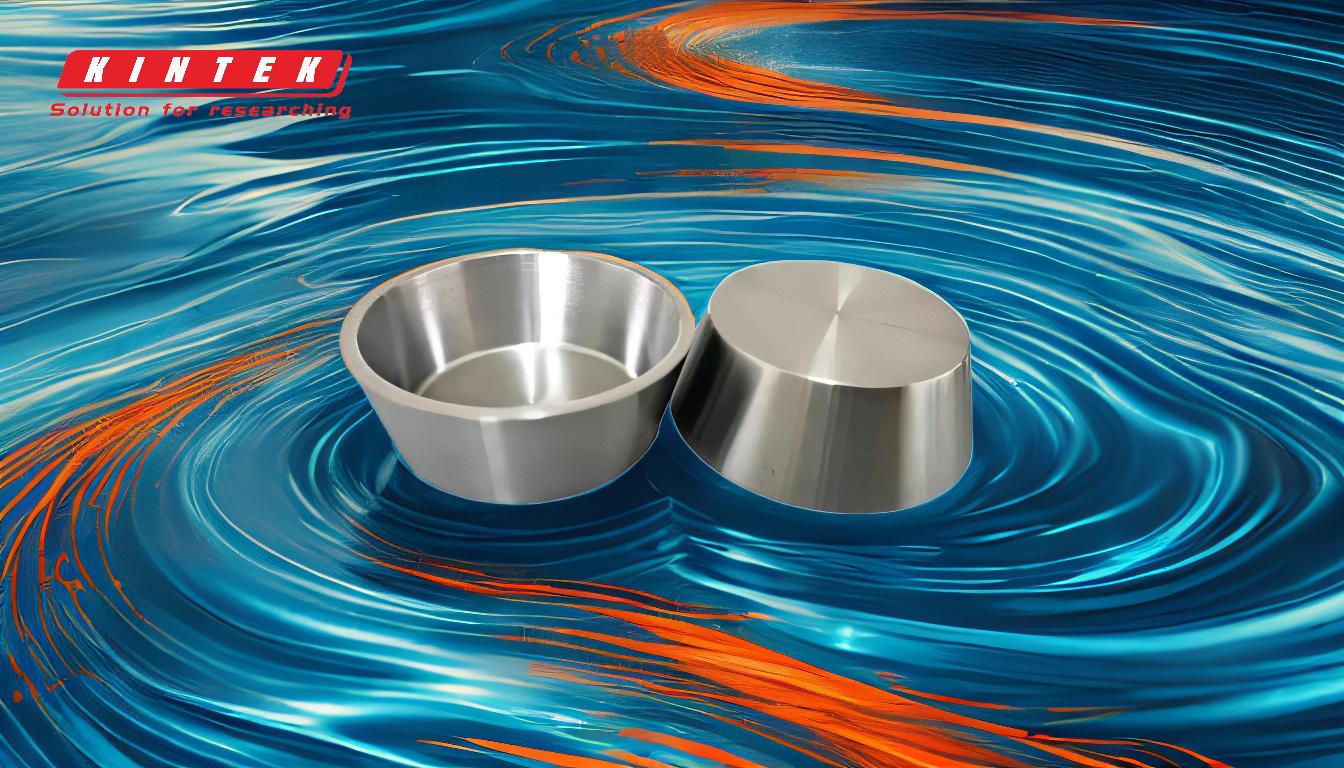
-
Thermionic Emission:
- Process: Electrons are emitted from a heated material, typically a metal filament, due to thermal energy overcoming the material's work function.
- Mechanism: When the filament is heated, electrons gain enough energy to escape the material's surface.
- Applications: Commonly used in vacuum tubes, cathode-ray tubes (CRTs), and electron microscopes.
- Advantages: Relatively simple and cost-effective method for generating electron beams.
- Limitations: Requires high temperatures, which can limit the lifespan of the emitting material.
-
Secondary Electron Emission:
- Process: Electrons are ejected from a material when it is bombarded by high-energy particles or ions.
- Mechanism: The impact of the primary particles transfers energy to the material's electrons, causing them to be emitted.
- Applications: Used in photomultiplier tubes, image intensifiers, and certain types of detectors.
- Advantages: Can generate high-intensity electron beams without the need for high temperatures.
- Limitations: Requires a source of high-energy particles, which can be complex and expensive.
-
Field Emission:
- Process: Electrons are extracted from a material by applying a strong electric field, typically at the tip of a sharp needle.
- Mechanism: The electric field reduces the potential barrier at the material's surface, allowing electrons to tunnel through and be emitted.
- Applications: Used in field emission displays (FEDs), electron guns, and certain types of electron microscopes.
- Advantages: Can produce very high-intensity electron beams with precise control.
- Limitations: Requires extremely high electric fields and precise engineering of the emitter tip.
-
Acceleration and Focusing:
- Process: Once emitted, electrons are accelerated by electric fields and focused into a coherent beam using magnetic or electrostatic lenses.
- Mechanism: Electric fields accelerate the electrons to high velocities, while magnetic or electrostatic lenses focus the beam to a fine point.
- Applications: Essential for all electron beam technologies, including electron microscopes, lithography, and welding.
- Advantages: Allows for precise control of the electron beam's energy and focus.
- Limitations: Requires sophisticated equipment and precise alignment.
-
Applications of Electron Beams:
- Scientific Research: Used in electron microscopes to study the structure of materials at the atomic level.
- Industrial Manufacturing: Employed in processes such as welding, cutting, and surface treatment.
- Medical Applications: Utilized in radiation therapy for cancer treatment.
- Electronics: Integral to the functioning of devices like CRTs and FEDs.
-
Considerations for Equipment and Consumable Purchasers:
- Beam Quality: Consider the required beam intensity, energy, and focus for your application.
- Cost and Maintenance: Evaluate the initial cost, operational expenses, and maintenance requirements of the electron beam source.
- Lifespan and Durability: Assess the longevity and durability of the emitting materials, especially in high-temperature or high-energy environments.
- Precision and Control: Ensure the equipment offers the necessary precision and control for your specific application.
By understanding these key points, purchasers can make informed decisions when selecting electron beam equipment and consumables, ensuring they meet the specific requirements of their applications.
Summary Table:
Method | Process | Applications | Advantages | Limitations |
---|---|---|---|---|
Thermionic Emission | Electrons emitted from a heated material (e.g., metal filament). | Vacuum tubes, CRTs, electron microscopes. | Simple, cost-effective. | High temperatures reduce material lifespan. |
Secondary Emission | Electrons ejected by bombarding material with high-energy particles. | Photomultiplier tubes, image intensifiers, detectors. | High-intensity beams without high temperatures. | Requires complex, expensive high-energy particle sources. |
Field Emission | Electrons extracted using strong electric fields at sharp tips. | Field emission displays (FEDs), electron guns, electron microscopes. | High-intensity beams with precise control. | Requires high electric fields and precise engineering. |
Acceleration/Focusing | Electrons accelerated by electric fields and focused using magnetic lenses. | Electron microscopes, lithography, welding. | Precise control of beam energy and focus. | Requires sophisticated equipment and alignment. |
Need help selecting the right electron beam equipment for your application? Contact our experts today!