Tubular heating elements are essential components in various heating applications, known for their durability and efficiency. They are constructed using a fine coil of nichrome resistance heating alloy wire housed within a metallic tube, typically made of copper or stainless steel. The space between the wire and the tube is filled with magnesium oxide powder, which acts as an insulator. The ends of the tube are sealed to prevent moisture ingress, and the tube is compressed to enhance heat transmission. This design ensures efficient heat transfer and longevity, making tubular heating elements suitable for a wide range of industrial and domestic applications.
Key Points Explained:
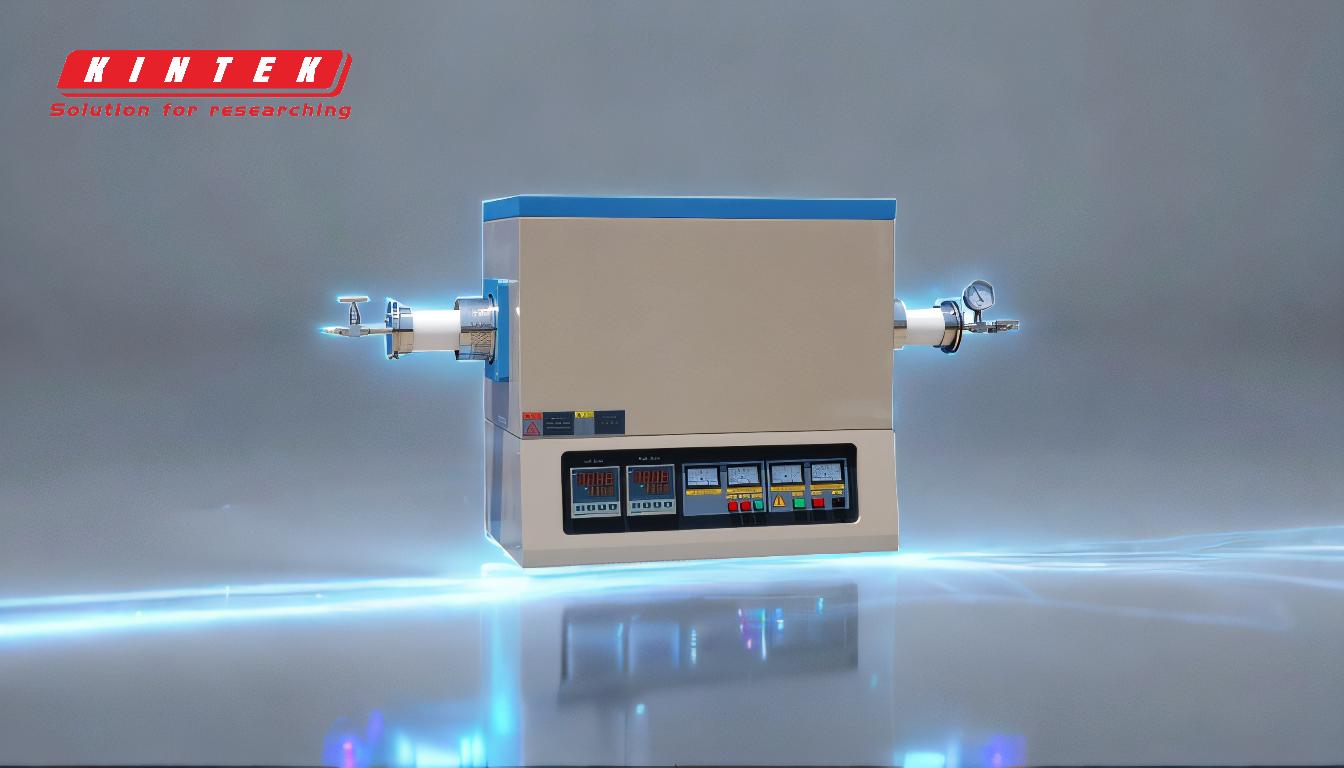
-
Nichrome Resistance Heating Alloy Wire:
- The core of a tubular heating element is a fine coil of nichrome wire. Nichrome is an alloy of nickel and chromium, chosen for its high electrical resistance and ability to withstand high temperatures without oxidizing. This wire generates heat when an electric current passes through it, making it the primary heating component.
-
Metallic Tube (Copper or Stainless Steel):
- The nichrome wire is encased in a metallic tube, which can be made of either copper or stainless steel. The choice of material depends on the application:
- Copper: Offers excellent thermal conductivity and is often used in applications requiring rapid heat transfer.
- Stainless Steel: Provides superior corrosion resistance and is preferred in environments where the element may be exposed to moisture or chemicals.
- The nichrome wire is encased in a metallic tube, which can be made of either copper or stainless steel. The choice of material depends on the application:
-
Magnesium Oxide Powder Insulation:
- The space between the nichrome wire and the metallic tube is filled with magnesium oxide (MgO) powder. This material serves several critical functions:
- Electrical Insulation: Prevents electrical shorts by insulating the nichrome wire from the metallic tube.
- Thermal Conductivity: Facilitates efficient heat transfer from the wire to the tube, ensuring uniform heating.
- Stability: Maintains its insulating properties even at high temperatures, ensuring the element's reliability.
- The space between the nichrome wire and the metallic tube is filled with magnesium oxide (MgO) powder. This material serves several critical functions:
-
Sealing the Ends:
- The ends of the metallic tube are sealed with insulating material to prevent moisture ingress. Moisture can compromise the insulation properties of the magnesium oxide powder and lead to electrical failures. The sealing process typically involves:
- Compression: The tube is compressed to ensure a tight seal, enhancing the element's durability and performance.
- Insulating Plugs: Insulating plugs or caps are used to seal the ends, providing an additional barrier against environmental factors.
- The ends of the metallic tube are sealed with insulating material to prevent moisture ingress. Moisture can compromise the insulation properties of the magnesium oxide powder and lead to electrical failures. The sealing process typically involves:
-
Compression for Heat Transmission:
- After the tube is filled with magnesium oxide powder and the ends are sealed, the entire assembly is compressed. This compression serves to:
- Maximize Heat Transfer: Ensures close contact between the nichrome wire, magnesium oxide powder, and the metallic tube, optimizing heat conduction.
- Enhance Structural Integrity: Improves the mechanical strength of the heating element, making it more resistant to physical stress and thermal expansion.
- After the tube is filled with magnesium oxide powder and the ends are sealed, the entire assembly is compressed. This compression serves to:
-
Applications and Benefits:
- Tubular heating elements are widely used in various applications due to their efficiency and durability:
- Industrial Heating: Used in furnaces, ovens, and heat treatment processes.
- Domestic Appliances: Found in water heaters, toasters, and coffee makers.
- Benefits: High thermal efficiency, long service life, and resistance to environmental factors make them a preferred choice for many heating needs.
- Tubular heating elements are widely used in various applications due to their efficiency and durability:
In summary, the manufacturing process of tubular heating elements involves precise engineering to ensure optimal performance and longevity. The combination of nichrome wire, metallic tubing, magnesium oxide insulation, and effective sealing techniques results in a robust and efficient heating solution suitable for a wide range of applications.
Summary Table:
Component | Function |
---|---|
Nichrome Resistance Wire | Generates heat when electric current passes through it. |
Metallic Tube (Copper/Stainless) | Encases the wire; copper for rapid heat transfer, stainless for corrosion resistance. |
Magnesium Oxide Powder | Insulates electrically, conducts heat, and ensures stability at high temps. |
Sealed Ends | Prevents moisture ingress, enhancing durability and performance. |
Compression | Maximizes heat transfer and improves structural integrity. |
Upgrade your heating systems with durable tubular heating elements—contact us today for expert advice!