Improving the performance of a lab filter press involves optimizing various operational and maintenance practices to ensure efficient filtration, longer equipment lifespan, and consistent results. Key areas to focus on include proper preparation of the slurry, regular maintenance of the filter plates and cloths, optimizing pressure and cycle times, and ensuring the equipment is used within its designed parameters. Additionally, understanding the specific properties of the material being filtered, such as particle size and viscosity, can help tailor the process for better outcomes. By addressing these aspects systematically, you can enhance the efficiency, reliability, and longevity of your lab filter press.
Key Points Explained:
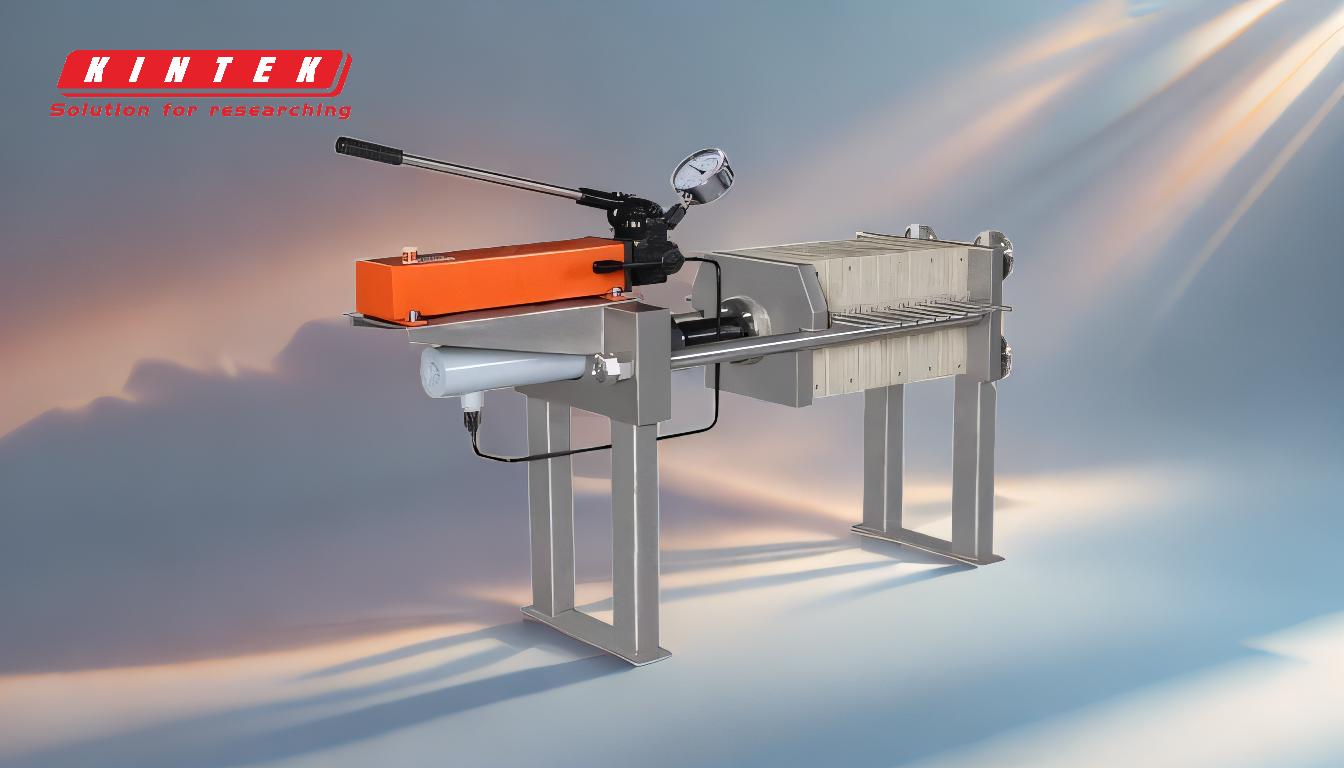
-
Proper Slurry Preparation
- The quality of the slurry significantly impacts the performance of the filter press. Ensure the slurry is well-mixed and free from large particles that could clog the filter cloth.
- Adjust the slurry concentration to optimize filtration rates. Too high a concentration can lead to slow filtration, while too low a concentration may result in inefficient separation.
- Use coagulants or flocculants if necessary to improve particle agglomeration and enhance filtration efficiency.
-
Regular Maintenance of Filter Plates and Cloths
- Inspect filter plates for wear, cracks, or warping, as these can compromise the seal and lead to leaks or reduced filtration efficiency. Replace damaged plates promptly.
- Clean filter cloths regularly to prevent clogging and ensure consistent flow rates. Use appropriate cleaning methods based on the type of material being filtered.
- Replace worn-out or damaged filter cloths to maintain optimal performance. Cloths with holes or tears can allow solids to pass through, reducing the quality of the filtrate.
-
Optimizing Pressure and Cycle Times
- Adjust the operating pressure to suit the specific slurry being filtered. Higher pressures can improve filtration rates but may also increase wear on the equipment.
- Monitor and optimize cycle times to balance throughput and filter cake dryness. Longer cycle times can result in drier cakes but may reduce overall productivity.
- Use automated controls to maintain consistent pressure and cycle times, reducing variability and improving repeatability.
-
Understanding Material Properties
- Analyze the particle size distribution, viscosity, and chemical composition of the slurry to tailor the filtration process. For example, finer particles may require finer filter cloths or longer cycle times.
- Consider pre-treatment steps, such as screening or sedimentation, to remove large particles or reduce viscosity before filtration.
- Test different filter cloth materials to find the best match for the specific slurry. Materials like polypropylene, polyester, or nylon may perform differently depending on the application.
-
Ensuring Proper Equipment Usage
- Operate the filter press within its designed capacity to avoid overloading, which can lead to premature wear or failure.
- Follow the manufacturer’s guidelines for setup, operation, and maintenance to ensure optimal performance and avoid common pitfalls.
- Train operators on best practices for using the filter press, including proper loading, unloading, and cleaning procedures.
-
Monitoring and Troubleshooting
- Regularly monitor key performance indicators, such as filtration rate, cake dryness, and filtrate clarity, to identify potential issues early.
- Troubleshoot common problems, such as uneven cake formation, leaks, or slow filtration, by checking for issues like uneven plate alignment, clogged cloths, or insufficient pressure.
- Keep detailed records of operational parameters and maintenance activities to track performance trends and identify areas for improvement.
By addressing these key areas, you can significantly improve the performance of your lab filter press, ensuring more efficient and reliable filtration processes. Regular maintenance, proper slurry preparation, and a thorough understanding of the material properties are essential for achieving consistent and high-quality results.
Summary Table:
Key Area | Action Steps |
---|---|
Slurry Preparation | - Ensure well-mixed slurry, free of large particles. Adjust concentration. Use coagulants if needed. |
Maintenance | - Inspect plates for wear. Clean/replace filter cloths regularly. |
Pressure & Cycle Times | - Optimize pressure and cycle times. Use automated controls for consistency. |
Material Properties | - Analyze particle size, viscosity. Pre-treat slurry if necessary. Test cloth materials. |
Equipment Usage | - Operate within capacity. Follow manufacturer guidelines. Train operators. |
Monitoring & Troubleshooting | - Monitor KPIs. Troubleshoot leaks, slow filtration, or uneven cake formation. |
Ready to optimize your lab filter press performance? Contact our experts today for tailored solutions!