Calculating a sieve test involves a systematic process to determine the particle size distribution of a granular material. The process begins with selecting a representative sample, preparing the sieves, and weighing the sample. The material is then sieved, either manually or using a sieve shaker, to separate particles based on size. After sieving, the retained material on each sieve is weighed, and the percentage of material retained on each sieve is calculated relative to the total sample mass. This data is then analyzed to evaluate the particle size distribution. Below is a detailed breakdown of the key steps and calculations involved in a sieve test.
Key Points Explained:
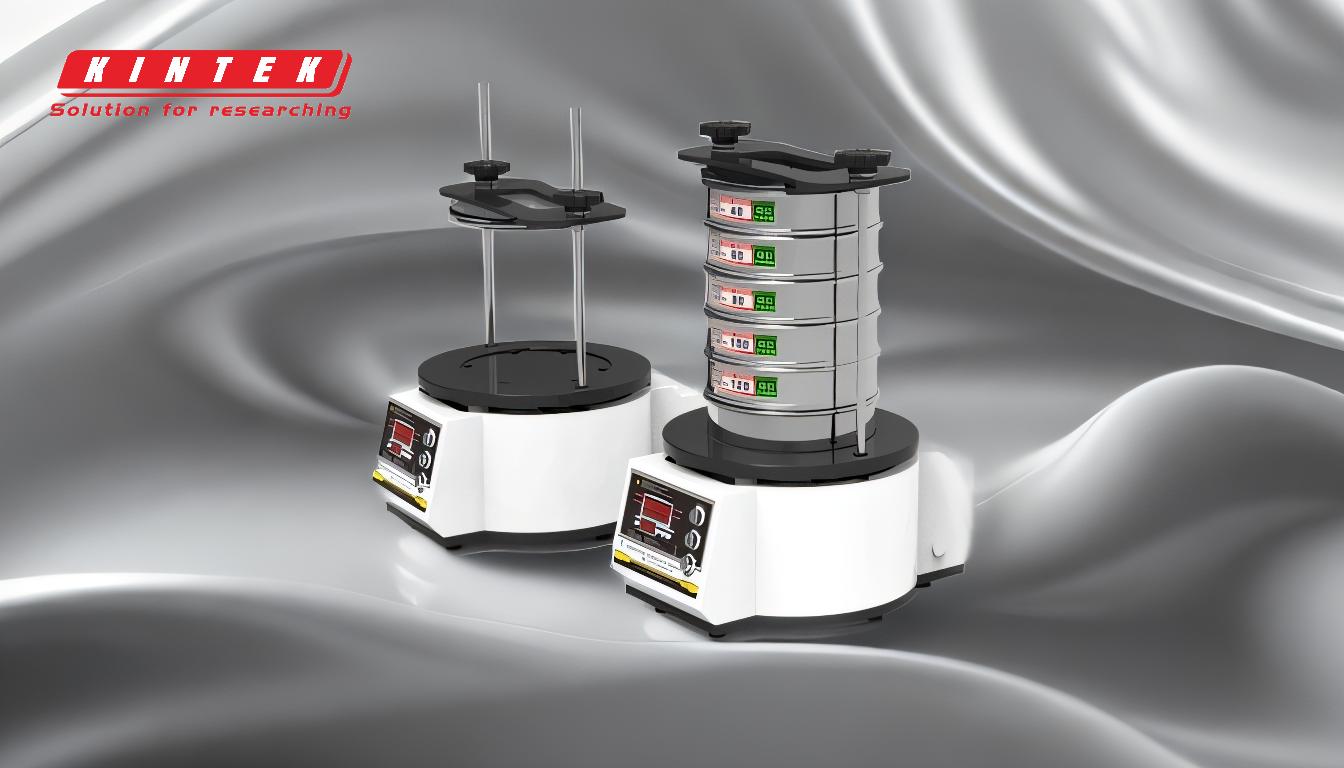
-
Sampling and Sample Preparation:
- Sampling: A representative sample of the material is collected to ensure the results reflect the entire batch.
- Sample Division: If the sample is too large, it may be divided to obtain a smaller, manageable quantity.
- Pre-Drying or Conditioning: Depending on the material, the sample may need to be dried or conditioned to remove moisture or other factors that could affect the results.
-
Selection of Test Sieves:
- Sieves with specific mesh sizes are selected based on the expected particle size distribution of the material.
- The sieves are arranged in a stack, with the largest mesh size at the top and the smallest at the bottom.
-
Weighing Sieves and Sample:
- Each sieve is weighed empty (tare weight) to account for its mass.
- The total sample is weighed before sieving to determine the initial mass.
-
Sieving Process:
- The sample is placed on the top sieve of the stack.
- The stack is shaken either manually or using a sieve shaker for a specified duration to allow particles to pass through the mesh.
- After sieving, the material retained on each sieve is collected.
-
Weighing Retained Material:
- Each sieve, along with the retained material, is weighed again.
- The mass of the retained material on each sieve is calculated by subtracting the tare weight of the sieve.
-
Calculating Percentage Retained:
- The percentage of material retained on each sieve is calculated using the formula: [ \text{Percentage Retained} = \left( \frac{\text{Mass Retained on Sieve}}{\text{Total Sample Mass}} \right) \times 100 ]
- This calculation is repeated for each sieve in the stack.
-
Data Evaluation:
- The cumulative percentage passing through each sieve is calculated by summing the percentages retained on all larger sieves and subtracting from 100.
- A particle size distribution curve can be plotted to visualize the results.
-
Cleaning and Drying Sieves:
- After the analysis, the sieves are cleaned and dried to remove any residual material, ensuring they are ready for future use.
-
Interpretation of Results:
- The results are interpreted to understand the particle size distribution, which can be used for quality control, material classification, or process optimization.
By following these steps, a sieve test provides a detailed understanding of the particle size distribution of a material, which is critical for various industrial and scientific applications.
Summary Table:
Step | Description |
---|---|
1. Sampling & Preparation | Collect a representative sample, divide if necessary, and pre-dry if required. |
2. Select Test Sieves | Choose sieves with specific mesh sizes and arrange them in descending order. |
3. Weigh Sieves & Sample | Weigh each sieve empty (tare weight) and the total sample before sieving. |
4. Sieving Process | Shake the sample on the sieve stack to separate particles by size. |
5. Weigh Retained Material | Weigh each sieve with retained material and calculate the mass retained. |
6. Calculate % Retained | Use the formula: (Mass Retained / Total Sample Mass) × 100. |
7. Data Evaluation | Calculate cumulative % passing and plot particle size distribution curves. |
8. Clean & Dry Sieves | Clean and dry sieves after use for future tests. |
9. Interpret Results | Analyze results for quality control, material classification, or optimization. |
Need help with sieve testing? Contact our experts today for tailored solutions!