Press forging and hammer forging are two common methods used in metalworking to shape metal into desired forms. Both techniques involve the application of force to deform the metal, but they differ significantly in their mechanisms, applications, and outcomes. Press forging uses a continuous, controlled force to shape the metal, making it suitable for precise and uniform parts. Hammer forging, on the other hand, employs repeated blows to deform the metal, which is ideal for creating complex shapes and improving the metal's grain structure. The choice between the two methods depends on factors such as the type of metal, the desired precision, and the production volume.
Key Points Explained:
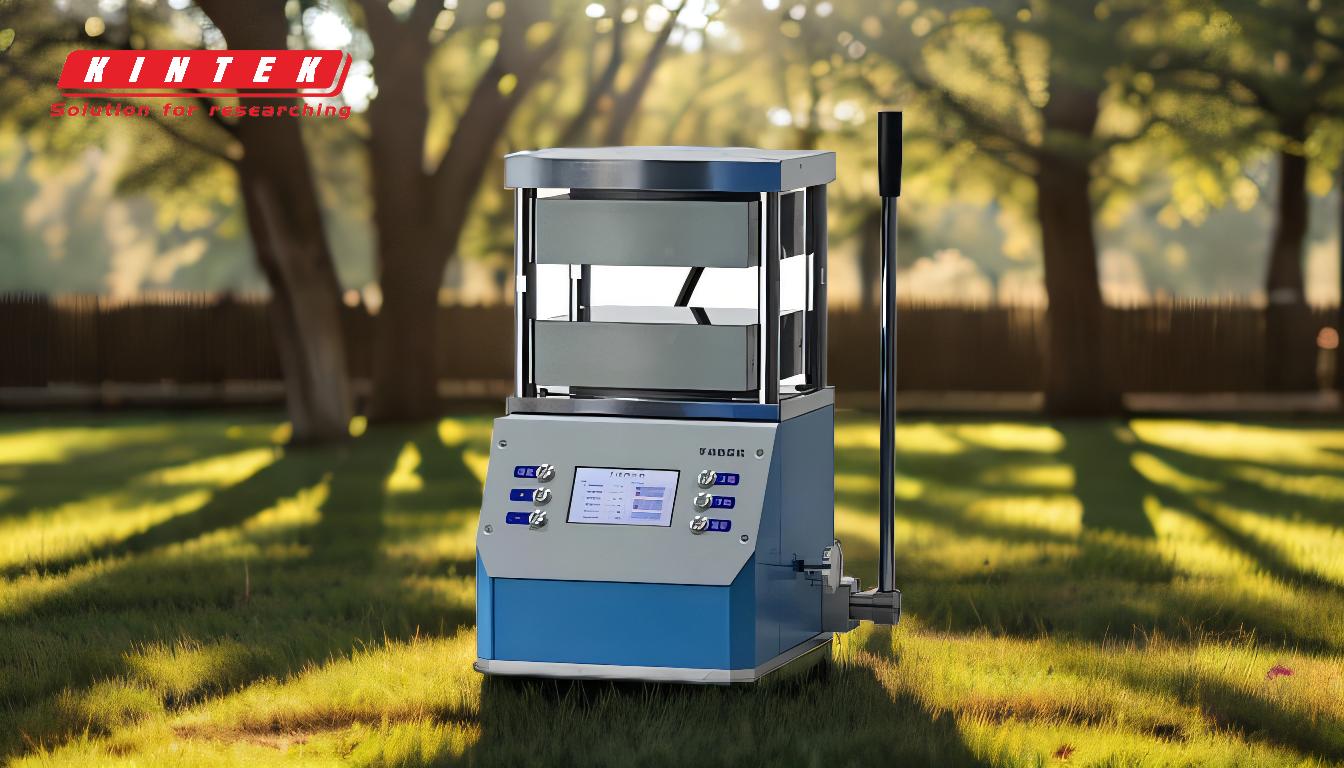
-
Mechanism of Force Application:
- Press Forging: In press forging, a continuous and steady force is applied to the metal using a hydraulic or mechanical press. This method ensures uniform deformation and is particularly effective for producing parts with tight tolerances.
- Hammer Forging: Hammer forging involves the use of a hammer or a series of hammers that deliver repeated blows to the metal. This method is more dynamic and can create intricate shapes by gradually deforming the metal.
-
Precision and Uniformity:
- Press Forging: The controlled force in press forging results in high precision and uniformity in the final product. This makes it suitable for applications where exact dimensions and consistent quality are critical.
- Hammer Forging: While hammer forging can produce complex shapes, the repeated blows can lead to less uniformity compared to press forging. However, it can improve the metal's grain structure, enhancing its mechanical properties.
-
Material Suitability:
- Press Forging: Press forging is well-suited for materials that require precise shaping and minimal internal stresses. It is often used for metals that are difficult to work with using other methods.
- Hammer Forging: Hammer forging is ideal for materials that benefit from improved grain structure and mechanical properties. It is commonly used for high-strength alloys and metals that require enhanced toughness.
-
Production Volume and Speed:
- Press Forging: Press forging is generally faster and more efficient for high-volume production runs. The continuous force application allows for quicker cycle times and higher throughput.
- Hammer Forging: Hammer forging is typically slower due to the repeated blows required to shape the metal. However, it is more flexible and can be adapted to smaller production runs or custom parts.
-
Cost Considerations:
- Press Forging: The initial setup cost for press forging can be high due to the need for specialized equipment. However, the efficiency and precision of the process can lead to lower per-unit costs in high-volume production.
- Hammer Forging: Hammer forging may have lower initial setup costs, but the slower production speed and potential for higher labor costs can make it more expensive for large-scale production.
-
Applications:
- Press Forging: Press forging is commonly used in industries where precision and uniformity are paramount, such as automotive, aerospace, and manufacturing of machinery parts.
- Hammer Forging: Hammer forging is often used in the production of tools, weapons, and custom metal components where complex shapes and enhanced material properties are required.
In summary, the choice between press forging and hammer forging depends on the specific requirements of the project, including the type of metal, desired precision, production volume, and cost considerations. Each method has its advantages and is suited to different applications within the metalworking industry.
Summary Table:
Aspect | Press Forging | Hammer Forging |
---|---|---|
Mechanism | Continuous, controlled force (hydraulic/mechanical press) | Repeated blows (hammer or series of hammers) |
Precision & Uniformity | High precision, uniform deformation | Less uniform, but improves grain structure |
Material Suitability | Ideal for precise shaping, minimal internal stresses | Best for improving grain structure, high-strength alloys |
Production Volume | Faster, efficient for high-volume production | Slower, flexible for smaller runs or custom parts |
Cost | High initial setup cost, lower per-unit cost in high-volume | Lower initial setup cost, potentially higher labor costs for large-scale |
Applications | Automotive, aerospace, machinery parts | Tools, weapons, custom components with complex shapes |
Need help choosing the right forging method for your project? Contact our experts today!