Creating an inert atmosphere in a furnace is essential for processes that require the absence of reactive gases like oxygen, carbon dioxide, or moisture. This is particularly important in applications such as heat treatment, sintering, or chemical reactions where oxidation or contamination must be avoided. The process involves replacing the ambient air inside the furnace with inert gases like argon or nitrogen, which are chemically inactive and prevent unwanted reactions. Below is a detailed explanation of how to achieve this and the key considerations involved.
Key Points Explained:
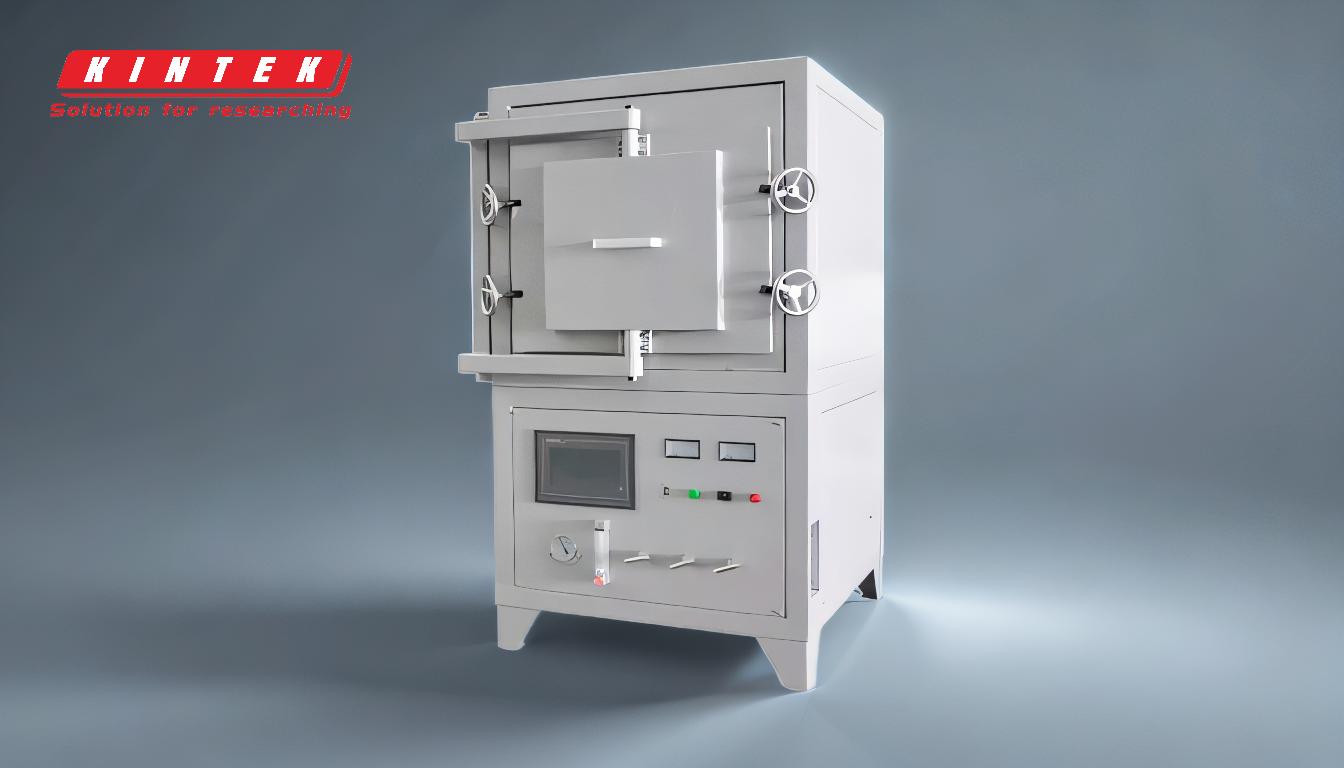
-
Purpose of an Inert Atmosphere
- An inert atmosphere furnace is used to eliminate reactive gases that could interfere with the process.
- Prevents oxidation, contamination, or chemical reactions that could alter the material properties.
- Commonly used in metallurgy, ceramics, and semiconductor manufacturing.
-
Choice of Inert Gases
-
Argon and Nitrogen: These are the most commonly used gases due to their high natural abundance and inert properties.
- Argon is heavier than air, making it ideal for creating a stable layer inside the furnace.
- Nitrogen is cost-effective and widely available, though it may not be suitable for materials that react with nitrogen at high temperatures.
- Other gases like helium can be used for specific applications, but they are less common due to higher costs.
-
Argon and Nitrogen: These are the most commonly used gases due to their high natural abundance and inert properties.
-
Gas Purging Process
- Sealing the Furnace: Ensure the furnace is airtight to prevent the ingress of ambient air.
- Initial Purging: Introduce the inert gas at a high flow rate to displace the existing air. This is often done through multiple purge cycles to ensure complete removal of reactive gases.
- Continuous Flow: Maintain a steady flow of inert gas during the process to counteract any potential leaks or diffusion of air.
-
Monitoring and Control
- Use sensors to monitor oxygen levels inside the furnace. Oxygen sensors or residual gas analyzers can ensure the atmosphere remains inert.
- Automated systems can regulate gas flow based on real-time feedback to maintain optimal conditions.
-
Safety Considerations
- Proper ventilation is necessary when working with inert gases to prevent asphyxiation hazards.
- Ensure gas cylinders and supply lines are securely connected and leak-free.
- Follow safety protocols for handling high-pressure gases.
-
Applications of Inert Atmosphere Furnaces
- Heat treatment of metals to prevent oxidation.
- Sintering of ceramics and powders.
- Annealing and brazing processes in manufacturing.
- Semiconductor fabrication where contamination must be minimized.
By following these steps and considerations, an inert atmosphere can be effectively created and maintained in a furnace, ensuring the success of sensitive processes. For more details on inert atmosphere furnaces, you can explore this resource.
Summary Table:
Key Aspect | Details |
---|---|
Purpose | Eliminate reactive gases, prevent oxidation, and avoid contamination. |
Common Inert Gases | Argon (stable layer) and nitrogen (cost-effective). |
Gas Purging Process | Seal furnace, perform initial purging, and maintain continuous gas flow. |
Monitoring & Control | Use oxygen sensors and automated systems for real-time regulation. |
Safety Considerations | Ensure proper ventilation, secure gas connections, and follow safety protocols. |
Applications | Heat treatment, sintering, annealing, brazing, and semiconductor fabrication. |
Need help setting up an inert atmosphere furnace? Contact our experts today for tailored solutions!