Sintered metal is produced through a series of steps that involve blending powdered metals, compacting them into a desired shape, and then heating the compacted part to bond the material. This process, known as powder metallurgy, results in a final product that is harder and stronger due to the fusion of particles. The key steps include blending the metal powder with additives, pressing it into shape, and sintering it in a furnace to achieve the desired mechanical properties. The process is highly controlled, often involving specific temperatures, pressures, and atmospheres to ensure the quality and integrity of the final product.
Key Points Explained:
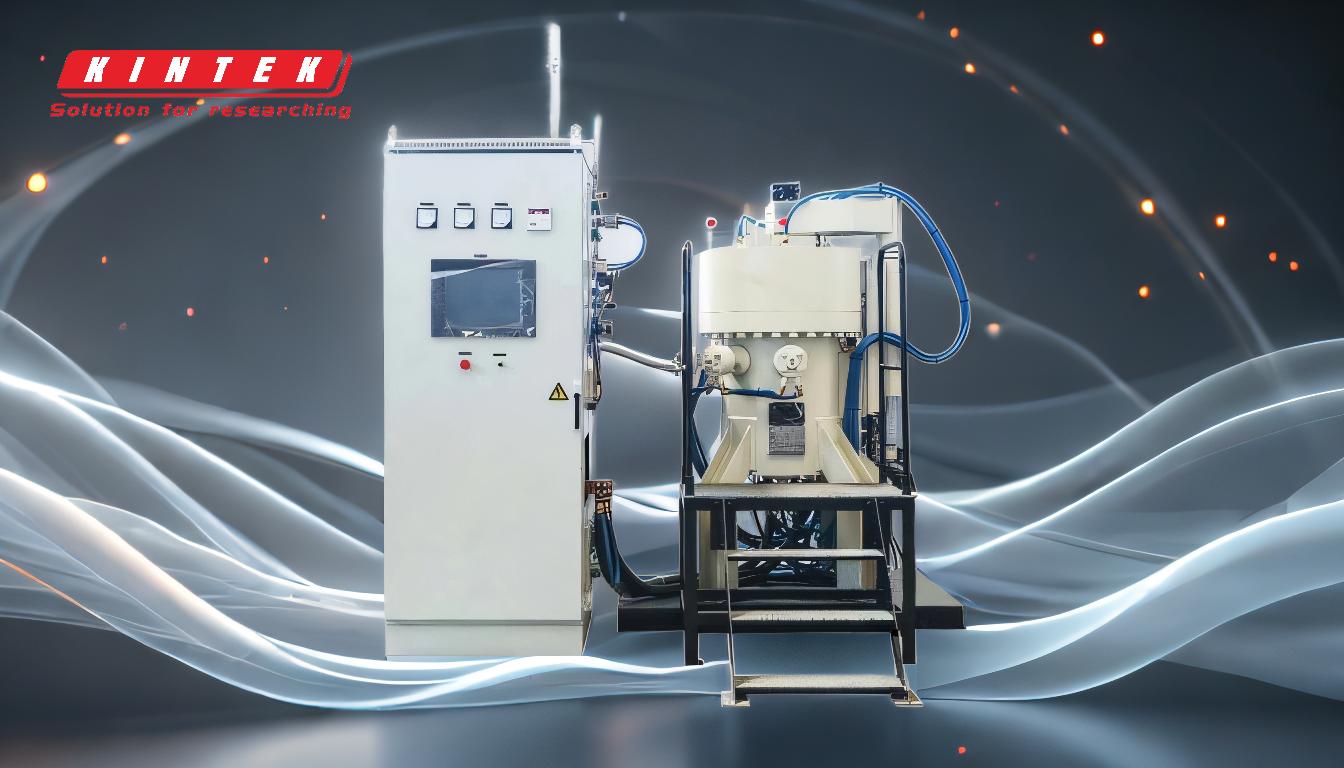
-
Blending of Metal Powders:
- The process begins with the blending of fine metal powders, which may include primary metals and alloying elements. Additives such as lubricants or binders (e.g., paraffin) are often mixed in to improve the flow and compaction properties of the powder. This step ensures uniformity in the composition of the final product.
-
Compaction:
- The blended powder is then pressed into a desired shape using high-pressure tools or dies. This step is crucial for forming the green compact, which is a fragile, pre-sintered shape. The compaction process can be done at room temperature or under heated conditions, depending on the material and desired outcome.
-
Sintering:
- The compacted part is placed in a sintering furnace, where it is heated to a temperature just below the melting point of the metal. This heating process causes the particles to bond through diffusion, resulting in a denser and stronger material. The sintering process often involves controlled atmospheres (e.g., vacuum or inert gases) to prevent oxidation and ensure proper bonding.
-
Debinding (if applicable):
- In cases where binders are used, a debinding step is necessary to remove the binder material before sintering. This is typically done in a controlled environment, such as a vacuum furnace, to protect the integrity of the part.
-
Cooling and Solidification:
- After sintering, the part is allowed to cool and solidify into its final form. This step may involve controlled cooling rates to achieve specific microstructures and mechanical properties.
-
Post-Sintering Treatments (optional):
- Depending on the application, additional treatments such as machining, heat treatment, or surface finishing may be applied to enhance the properties or appearance of the sintered part.
The sintering process is highly versatile and can be adapted to produce a wide range of metal components with precise dimensions and properties. It is widely used in industries such as automotive, aerospace, and electronics due to its efficiency and ability to produce complex shapes with minimal material waste.
Summary Table:
Step | Description |
---|---|
Blending | Mix fine metal powders with additives for uniformity and improved compaction. |
Compaction | Press blended powder into a desired shape using high-pressure tools or dies. |
Sintering | Heat compacted part in a furnace to bond particles, creating a denser material. |
Debinding | Remove binders (if used) in a controlled environment before sintering. |
Cooling | Allow part to cool and solidify, often with controlled cooling rates. |
Post-Treatments | Apply optional treatments like machining or heat treatment for enhanced properties. |
Interested in producing high-quality sintered metal parts? Contact us today to learn more!