Using a crucible furnace involves a series of steps to ensure safe and efficient melting of materials. The process begins with preparing the furnace and crucible, followed by heating the material to its melting point, and finally pouring the molten material into a mold or container. Proper temperature control, crucible selection, and safety precautions are essential for successful operation. The furnace's design, size, and heating source (e.g., natural gas, propane, or electricity) also play a significant role in the melting process. Below is a detailed explanation of the key steps and considerations for using a crucible furnace.
Key Points Explained:
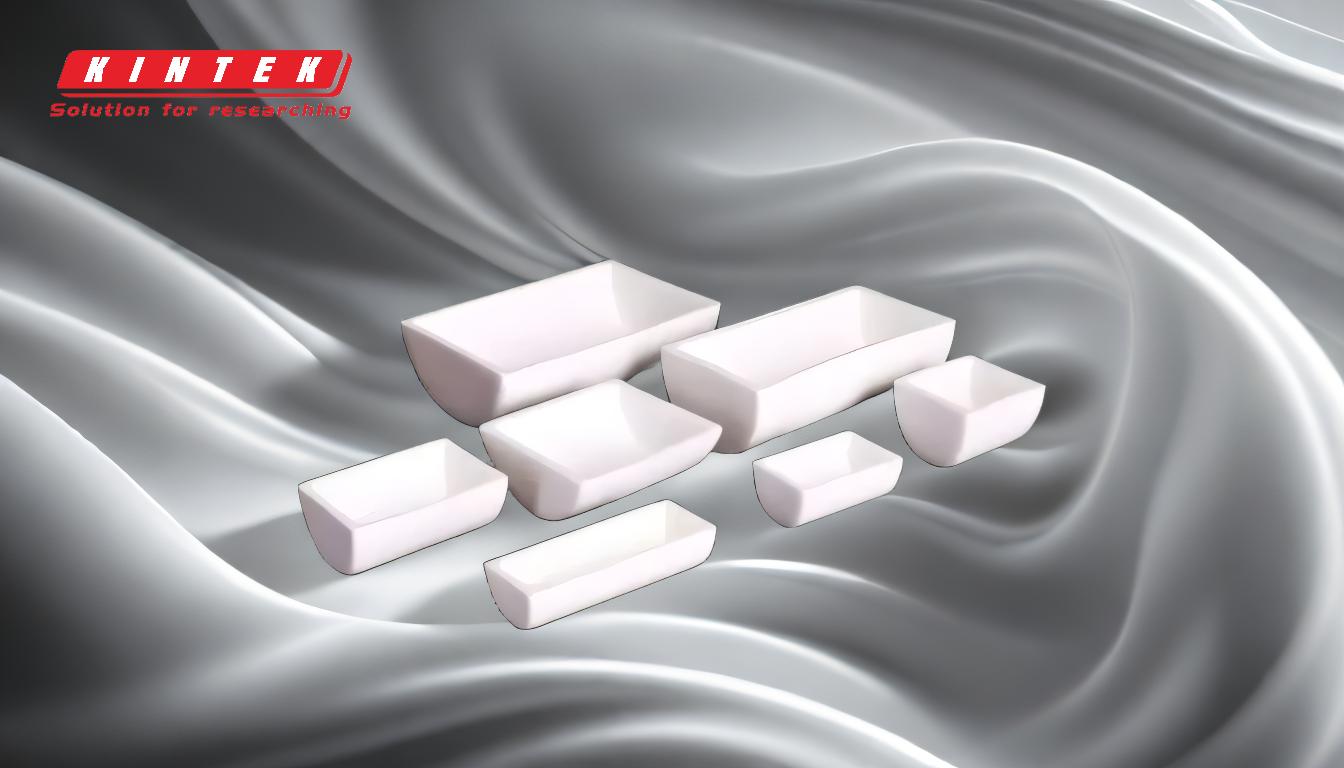
-
Preparation Before Use
- Inspect the Furnace and Crucible: Ensure the furnace chamber and crucible are clean and free from debris or residues from previous uses. This prevents contamination and ensures efficient heat transfer.
- Select the Right Crucible: Choose a crucible made of material compatible with the substance you intend to melt. For example, graphite crucibles are suitable for metals, while ceramic crucibles are better for glass or chemicals.
- Check the Heating Source: Verify that the furnace's heating element (e.g., gas burner or electric coil) is functioning properly. Ensure there are no leaks if using a gas-powered furnace.
-
Loading the Material
- Place the Material in the Crucible: Add the material to be melted into the crucible. Avoid overfilling, as this can cause spills or uneven heating.
- Position the Crucible in the Furnace: Place the crucible securely in the furnace chamber, ensuring it is centered and stable. This ensures even heat distribution and prevents tipping during the melting process.
-
Heating the Material
- Set the Desired Temperature: Adjust the furnace's temperature control system to the required melting point of the material. Use a thermometer or digital controller for precise temperature regulation.
- Monitor the Heating Process: Keep an eye on the material as it heats up. The heating element transfers heat to the crucible, causing the material to melt gradually. Avoid rapid temperature increases, which can damage the crucible or cause thermal shock.
-
Melting and Pouring
- Wait for the Material to Melt: Once the material reaches its melting point, it will become molten. Stir the material gently if necessary to ensure uniformity.
- Pour the Molten Material: Use tongs or a crucible holder to carefully remove the crucible from the furnace. Pour the molten material into a preheated mold or container. Ensure the mold is clean and dry to prevent defects in the final product.
-
Post-Operation Steps
- Cool Down the Furnace: Allow the furnace to cool naturally after use. Do not expose it to cold air or water, as this can cause cracking or damage to the furnace lining.
- Clean the Crucible and Furnace: Remove any remaining material from the crucible and clean the furnace chamber. This prevents contamination in future uses and extends the equipment's lifespan.
-
Safety Considerations
- Wear Protective Gear: Always use heat-resistant gloves, safety goggles, and protective clothing when operating the furnace.
- Avoid Overheating: Do not exceed the recommended temperature for the crucible or material, as this can lead to equipment failure or hazardous situations.
- Ensure Proper Ventilation: Use the furnace in a well-ventilated area to avoid inhaling fumes or gases released during the melting process.
-
Factors Affecting Performance
- Furnace Design and Size: Larger furnaces may take longer to heat up but can accommodate bigger crucibles. Compact furnaces are suitable for small-scale operations.
- Heating Source Efficiency: Electric furnaces offer precise temperature control, while gas-powered furnaces provide higher heat output. Choose the heating source based on your specific needs.
- Material Properties: Different materials have varying melting points and thermal conductivities. Adjust the heating process accordingly to achieve optimal results.
By following these steps and considerations, you can effectively use a crucible furnace to melt and shape materials for various applications, such as metal casting, glassmaking, or chemical processing. Proper maintenance and adherence to safety protocols are crucial for achieving consistent and reliable results.
Summary Table:
Step | Key Actions |
---|---|
Preparation Before Use | Inspect furnace and crucible, select the right crucible, check heating source. |
Loading the Material | Place material in crucible, position crucible securely in the furnace. |
Heating the Material | Set desired temperature, monitor heating process to avoid thermal shock. |
Melting and Pouring | Wait for material to melt, pour molten material into a preheated mold. |
Post-Operation Steps | Cool down the furnace, clean crucible and furnace chamber. |
Safety Considerations | Wear protective gear, avoid overheating, ensure proper ventilation. |
Factors Affecting Performance | Consider furnace design, heating source efficiency, and material properties. |
Ready to optimize your melting process? Contact us today for expert advice and solutions!