A hydrogen furnace operates by utilizing hydrogen as a medium to heat materials at high temperatures, enabling specific heat treatment processes. Unlike conventional furnaces that burn fuel to generate heat, hydrogen furnaces often use hydrogen in a controlled reaction with oxygen to produce both heat and electricity. These furnaces are designed to maintain precise temperature control, with features like automatic and manual control, high-temperature capabilities (up to 1600℃), and uniform heating. They are equipped with advanced systems for gas flow, pressure control, and safety, ensuring efficient and safe operation. Hydrogen furnaces are widely used in applications requiring oxidation reduction, rapid heating, and uniform temperature distribution.
Key Points Explained:
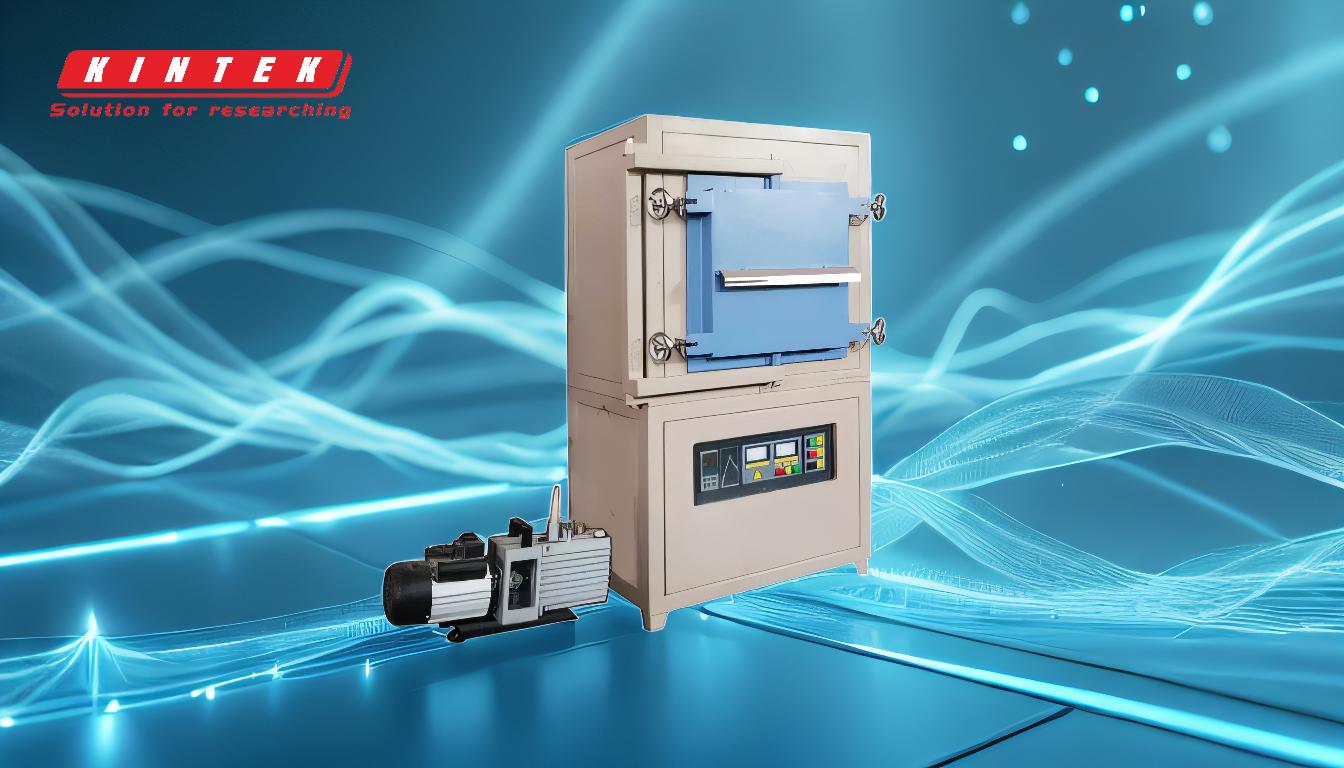
-
Working Principle of a Hydrogen Furnace:
- Hydrogen furnaces use hydrogen as a heating medium, reacting with oxygen to generate heat and electricity in a controlled manner.
- Unlike traditional furnaces, hydrogen is not burned but undergoes a chemical reaction in a fuel cell or similar system.
- This process allows for precise heat treatment of materials at high temperatures, often exceeding 1600℃.
-
Key Components of a Hydrogen Furnace:
- Heating Chamber: The core area where materials are heated.
- Hydrogen Supply System: Provides a controlled flow of hydrogen into the furnace.
- Temperature Control System: Ensures precise regulation of temperature, often with automatic and manual modes.
- Furnace Structure: Includes the furnace cover, bottom, body, and electric control system, designed for durability and efficiency.
-
Temperature Control and Uniformity:
- Hydrogen furnaces offer automatic temperature control with high precision (±1℃).
- Temperature uniformity is maintained within a range of ±3℃ to ±10℃, depending on user requirements.
- Multiple heating programs can be stored to accommodate various process needs.
-
Advanced Features for Efficiency and Safety:
- Automatic Control: Industrial microcomputers manage process time, temperature, gas flow, and pressure.
- Pressure Control System: Imported systems ensure closed-loop control and high stability.
- Safety Mechanisms: Alarm functions and safety interlock devices enhance operational safety.
- Corrosion-Resistant Materials: Stainless steel pipe fittings and valves ensure airtightness and longevity.
-
Applications and Benefits:
- Oxidation Reduction: Hydrogen furnaces create a high-purity hydrogen environment, reducing oxidation during heat treatment.
- Rapid Heating and Cooling: Efficient heat transfer allows for quick temperature changes.
- Uniform Heating: Ensures consistent material properties across the entire workpiece.
- Versatility: Suitable for a wide range of applications, including annealing, sintering, and reduction processes.
-
Comparison with Conventional Furnaces:
- Hydrogen furnaces are more environmentally friendly, as they do not produce harmful emissions.
- They offer superior temperature control and uniformity compared to traditional gas or oil-fired furnaces.
- The use of hydrogen as a fuel source can lead to energy savings and improved process efficiency.
-
Operational Flexibility:
- Hydrogen furnaces can be customized with multiple heating programs to meet specific industrial requirements.
- The man-machine interface and flexible technological performance allow for easy operation and adaptation to various processes.
-
Safety Considerations:
- The inclusion of advanced safety features, such as alarm systems and interlock devices, ensures safe operation even at high temperatures.
- The use of high-quality materials and components minimizes the risk of leaks or failures.
In summary, hydrogen furnaces are highly efficient, precise, and versatile tools for high-temperature heat treatment processes. Their advanced control systems, safety features, and ability to operate in a high-purity hydrogen environment make them ideal for applications requiring oxidation reduction, rapid heating, and uniform temperature distribution.
Summary Table:
Feature | Details |
---|---|
Working Principle | Uses hydrogen as a heating medium, reacting with oxygen to generate heat. |
Temperature Range | Up to 1600℃ with precision control (±1℃) and uniformity (±3℃ to ±10℃). |
Key Components | Heating chamber, hydrogen supply system, temperature control, furnace body. |
Advanced Features | Automatic control, pressure regulation, safety mechanisms, corrosion-resistant materials. |
Applications | Oxidation reduction, rapid heating, uniform temperature distribution. |
Benefits | Eco-friendly, energy-efficient, superior temperature control, and versatility. |
Ready to enhance your heat treatment processes? Contact us today to learn more about hydrogen furnaces!