A resistance furnace operates by converting electrical energy into heat energy through the Joule heating effect, where electric current passes through a conductor (resistor) to generate heat. This heat is then used to heat materials or workpieces placed inside the furnace. The furnace can be designed for direct heating, where the material itself acts as the resistor, or indirect heating, where heating elements or conductive media transfer heat to the material via conduction, convection, and radiation. Resistance furnaces are widely used in industrial applications due to their precise temperature control, efficiency, and ability to operate in controlled environments like vacuum chambers.
Key Points Explained:
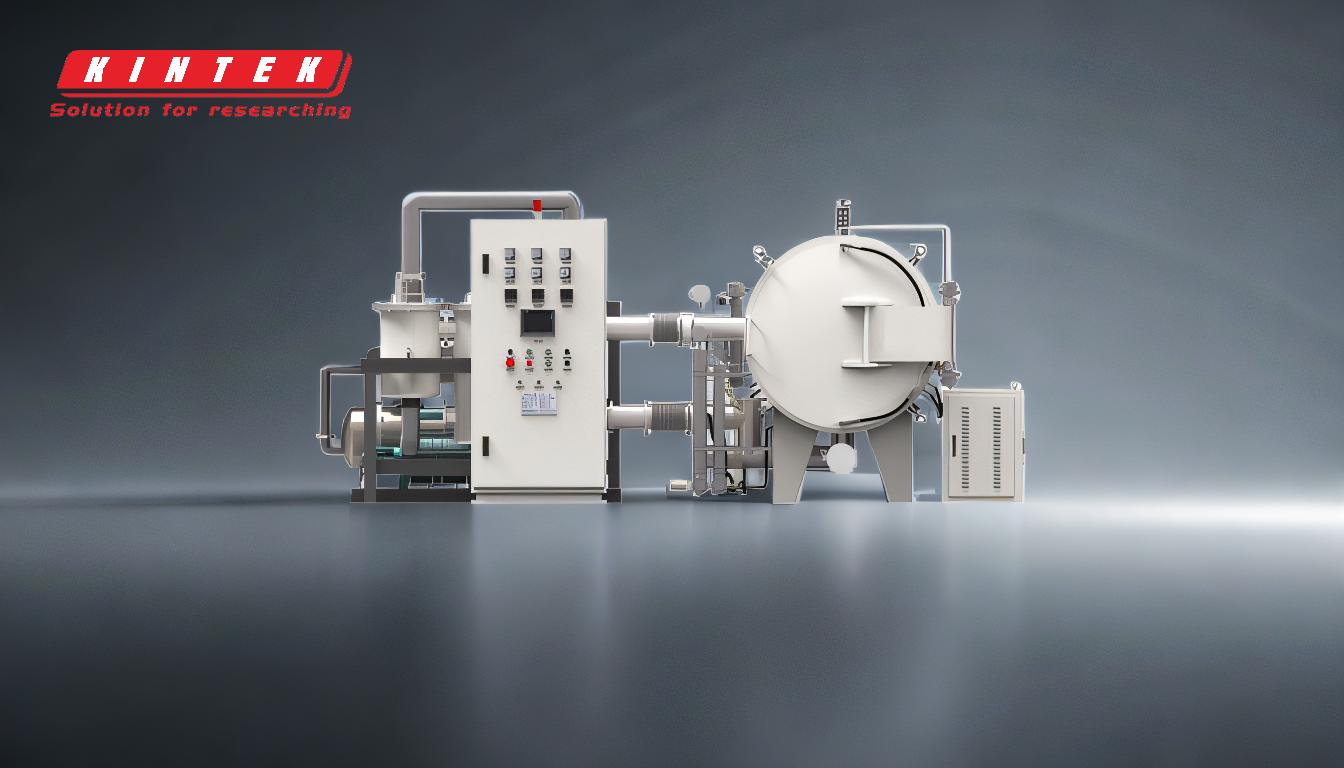
-
Principle of Joule Heating:
- A resistance furnace works on the principle of Joule heating, where electrical energy is converted into heat energy as current passes through a resistive element. This heat is then used to raise the temperature of the material or workpiece inside the furnace.
-
Types of Resistance Furnaces:
- Direct Heating Furnaces: In these furnaces, the material to be heated acts as the resistor. Electrodes are buried in the material, and the current flows directly through it, generating heat. This method is efficient for conductive materials like metals.
- Indirect Heating Furnaces: Here, heating elements or conductive media (like ceramic or metal resistors) are used to generate heat. The heat is then transferred to the material through conduction, convection, and radiation. This method is suitable for materials that cannot act as resistors themselves.
-
Heat Transfer Mechanisms:
- Conduction: Heat is transferred through direct contact between the heating elements and the material.
- Convection: Heat is transferred through the movement of heated air or gas within the furnace chamber.
- Radiation: Heat is transferred through electromagnetic waves emitted by the heating elements, which are absorbed by the material.
-
Applications in Controlled Environments:
- Resistance furnaces can operate in controlled environments, such as vacuum chambers. For example, in a vacuum hardening furnace, metal components are heated to specific temperatures in a vacuum to minimize surface contaminants like oxides and reactive gases. This ensures the desired mechanical properties are achieved.
-
Advantages of Resistance Furnaces:
- Precise Temperature Control: Resistance furnaces allow for accurate and uniform heating, making them ideal for processes requiring specific temperature profiles.
- Energy Efficiency: By directly converting electrical energy into heat, these furnaces minimize energy losses.
- Versatility: They can be used for a wide range of materials and processes, including annealing, hardening, and sintering.
-
Industrial Use:
- Resistance furnaces are commonly used in industries such as metallurgy, ceramics, and electronics. They are driven by electricity, typically utilizing existing plant voltage, making them easy to integrate into industrial setups.
By understanding these key points, a purchaser can evaluate the suitability of a resistance furnace for their specific needs, considering factors like material type, required temperature range, and the desired heating method.
Summary Table:
Aspect | Details |
---|---|
Principle | Joule heating: Converts electrical energy into heat via resistive elements. |
Types | Direct heating (material as resistor) or indirect heating (heating elements). |
Heat Transfer | Conduction, convection, and radiation. |
Applications | Vacuum hardening, annealing, sintering, and more. |
Advantages | Precise temperature control, energy efficiency, and versatility. |
Industrial Use | Metallurgy, ceramics, electronics, and other high-temperature processes. |
Ready to enhance your industrial processes with a resistance furnace? Contact us today to find the perfect solution!