Vacuum heat treatment is a sophisticated process used to enhance the properties of materials, particularly metals, by heating them in a vacuum environment. This method prevents oxidation and contamination, ensuring a clean and precise treatment. The process involves several steps, including heating, holding, and cooling, all conducted under controlled vacuum conditions. Key classifications of vacuum heat treatment include vacuum sintering, vacuum brazing, vacuum quenching, and more, each serving specific purposes in material processing.
Key Points Explained:
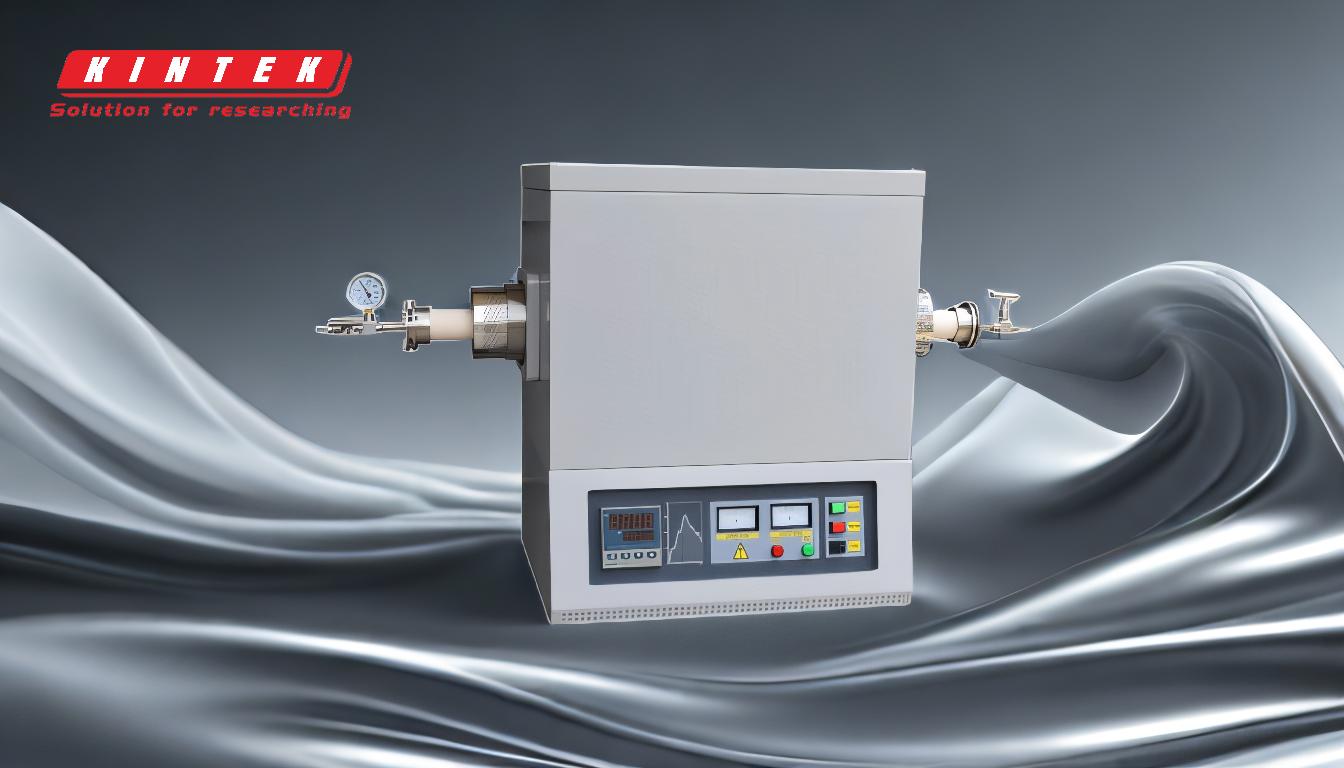
-
Vacuum Environment:
- The vacuum environment is crucial as it eliminates the presence of oxygen and other reactive gases, preventing oxidation and decarburization of the material. This ensures a clean surface and enhances the material's mechanical properties.
- The vacuum is typically achieved using a combination of roughing pumps and high-vacuum pumps, such as molecular pumps, to reach the desired pressure levels.
-
Heating Process:
- Materials are heated to specific temperatures depending on the type of heat treatment being performed. The heating is usually done using electric resistance heaters or induction heating, which provide precise temperature control.
- The absence of air in the vacuum chamber allows for uniform heating, reducing the risk of thermal stress and distortion.
-
Holding and Soaking:
- Once the desired temperature is reached, the material is held at that temperature for a specific period, known as soaking. This allows for the uniform distribution of heat and the completion of any phase transformations or diffusion processes.
- The duration of soaking depends on the material and the specific heat treatment process.
-
Cooling Process:
- After soaking, the material is cooled. Cooling can be done slowly (furnace cooling) or rapidly (quenching), depending on the desired properties. In vacuum heat treatment, cooling is often controlled to prevent thermal shock and ensure uniformity.
- Quenching in a vacuum environment may involve the use of inert gases like nitrogen or argon to achieve the desired cooling rate.
-
Types of Vacuum Heat Treatment:
- Vacuum Sintering: Used for powder metallurgy, where metal powders are compacted and heated to form a solid piece.
- Vacuum Brazing: Joining of metals using a filler material, performed in a vacuum to ensure a clean, strong bond.
- Vacuum Quenching: Rapid cooling of heated materials to achieve high hardness and strength.
- Vacuum Tempering: Reheating quenched materials to reduce brittleness and improve toughness.
- Vacuum Annealing: Heating materials to relieve internal stresses and improve ductility.
- Vacuum Solution Treatment: Used for alloys to dissolve precipitates and achieve a homogeneous structure.
- Vacuum Aging Heat Treatment: Aging of materials to enhance strength and stability.
- Vacuum Normalizing: Heating and cooling to refine the grain structure of steels.
- Vacuum Degassing: Removal of dissolved gases from metals to improve quality.
- Magnetic Annealing: Heat treatment in a magnetic field to enhance magnetic properties.
- Dehydroxylation: Removal of hydroxyl groups from materials, often used in ceramics.
-
Equipment and Safety:
- The equipment used for vacuum heat treatment includes vacuum furnaces, pumps, and cooling systems. Proper maintenance and operation of these components are essential for effective treatment.
- Safety protocols, such as sequentially closing the molecular pump switch, circulating water switch, external circulating water valve, and the main power supply gate, are crucial to prevent accidents and ensure the longevity of the equipment.
By understanding these key points, one can appreciate the complexity and precision involved in vacuum heat treatment, making it a preferred method for high-quality material processing. For more detailed information on vacuum heat treatment, you can refer to vacuum heat treatment.
Summary Table:
Key Step | Description |
---|---|
Vacuum Environment | Eliminates oxygen and reactive gases, preventing oxidation and contamination. |
Heating Process | Precise heating using electric resistance or induction for uniform temperature. |
Holding and Soaking | Maintains temperature to ensure uniform heat distribution and phase changes. |
Cooling Process | Controlled cooling to prevent thermal shock and achieve desired properties. |
Types of Treatment | Includes sintering, brazing, quenching, tempering, annealing, and more. |
Equipment and Safety | Uses vacuum furnaces, pumps, and cooling systems with strict safety protocols. |
Discover how vacuum heat treatment can elevate your material processing—contact our experts today!