An electron beam works by generating and accelerating electrons in a vacuum environment, where they are manipulated using electric and magnetic fields to form a focused beam. This beam can be directed onto a target material, where the energy of the electrons is converted into heat or kinetic energy, enabling precise control over material properties. The process involves heating a filament to produce electrons, accelerating them through a voltage gradient, and using electromagnets to scan or focus the beam. Electron beams are used in various applications, including material processing, semiconductor manufacturing, and thin-film coating, due to their ability to deliver concentrated energy with high precision.
Key Points Explained:
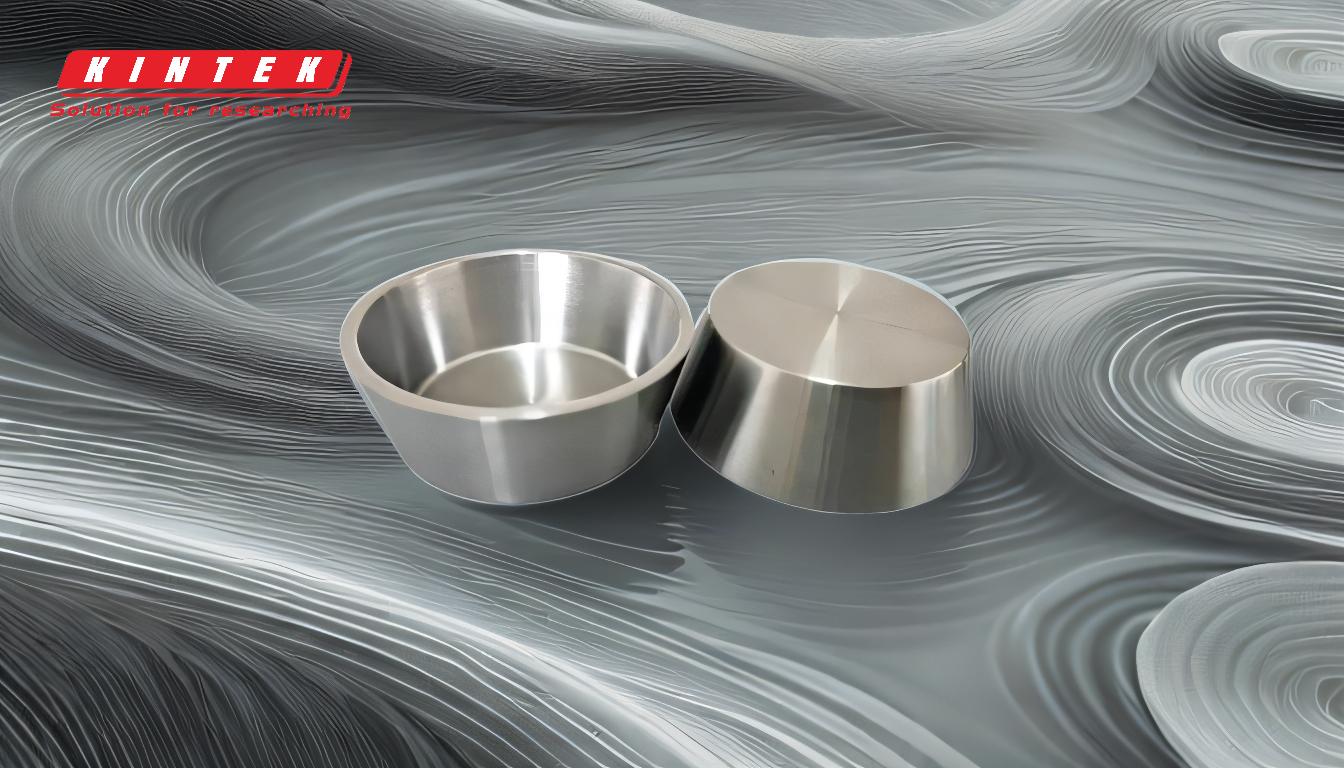
-
Electron Generation:
- Electrons are generated by heating a filament, typically made of tungsten or another high-melting-point material. This process, known as thermionic emission, releases electrons into a vacuum environment.
- The vacuum ensures that the electrons travel without colliding with gas molecules, maintaining the integrity of the beam.
-
Electron Acceleration:
- A voltage gradient is applied to draw the electrons away from the filament and accelerate them through a vacuum tube. This creates a high-energy electron beam.
- The energy of the electrons is proportional to the applied voltage, allowing precise control over the beam's properties.
-
Beam Manipulation:
- Electric and magnetic fields are used to focus and steer the electron beam. Electromagnets can scan the beam to create specific patterns or concentrate it into a fine spot.
- This manipulation is crucial for applications like electron microscopy, lithography, and material processing, where precision is essential.
-
Energy Conversion:
- When the electron beam collides with solid-state matter, the electrons transfer their energy to the material, converting it into heat or kinetic energy.
- This concentrated energy can induce changes in the material's properties, such as polymer crosslinking, chain scissioning, or thin-film deposition.
-
Applications of Electron Beams:
- Material Processing: Electron beams are used for polymer modification, curing composite materials, and enhancing semiconductor properties.
- Thin-Film Deposition: In electron beam coating, the beam heats an evaporant material, creating a vapor that condenses on a substrate to form a thin film.
- Microscopy and Lithography: Electron beams enable high-resolution imaging and the creation of sub-micrometer and nano-dimensional patterns.
- Industrial and Environmental Uses: Applications include cable isolation treatment, food processing, and microelectronics manufacturing, offering economic and environmental benefits.
-
Advantages of Electron Beam Technology:
- Precision: The ability to control the beam's energy and focus allows for highly accurate material modifications.
- Versatility: Electron beams can be used in a wide range of industries, from electronics to food processing.
- Efficiency: The process is energy-efficient and can be automated, reducing costs and improving productivity.
- Environmental Benefits: Electron beam processing often reduces the need for chemical additives, making it a cleaner alternative to traditional methods.
By understanding these key points, one can appreciate the versatility and precision of electron beam technology, making it a valuable tool in modern science and industry.
Summary Table:
Key Aspect | Description |
---|---|
Electron Generation | Electrons are produced via thermionic emission by heating a tungsten filament. |
Electron Acceleration | A voltage gradient accelerates electrons, creating a high-energy beam. |
Beam Manipulation | Electric and magnetic fields focus and steer the beam for precise applications. |
Energy Conversion | Electron energy converts to heat or kinetic energy upon material interaction. |
Applications | Material processing, thin-film deposition, microscopy, and industrial uses. |
Advantages | Precision, versatility, efficiency, and environmental benefits. |
Unlock the potential of electron beam technology for your industry—contact our experts today!