Furnace cooling in the heat treatment process is a controlled method of reducing the temperature of treated metals to achieve specific material properties. It typically involves the use of inert gases, such as argon, which are circulated through the heating chamber to absorb heat and facilitate cooling. This process ensures that the metal cools uniformly and at a controlled rate, preventing defects such as warping or cracking. Cooling methods can vary depending on the desired outcome, with options including rapid quenching or slower, controlled cooling. The choice of cooling method depends on the material, the heat treatment process, and the intended application of the final product.
Key Points Explained:
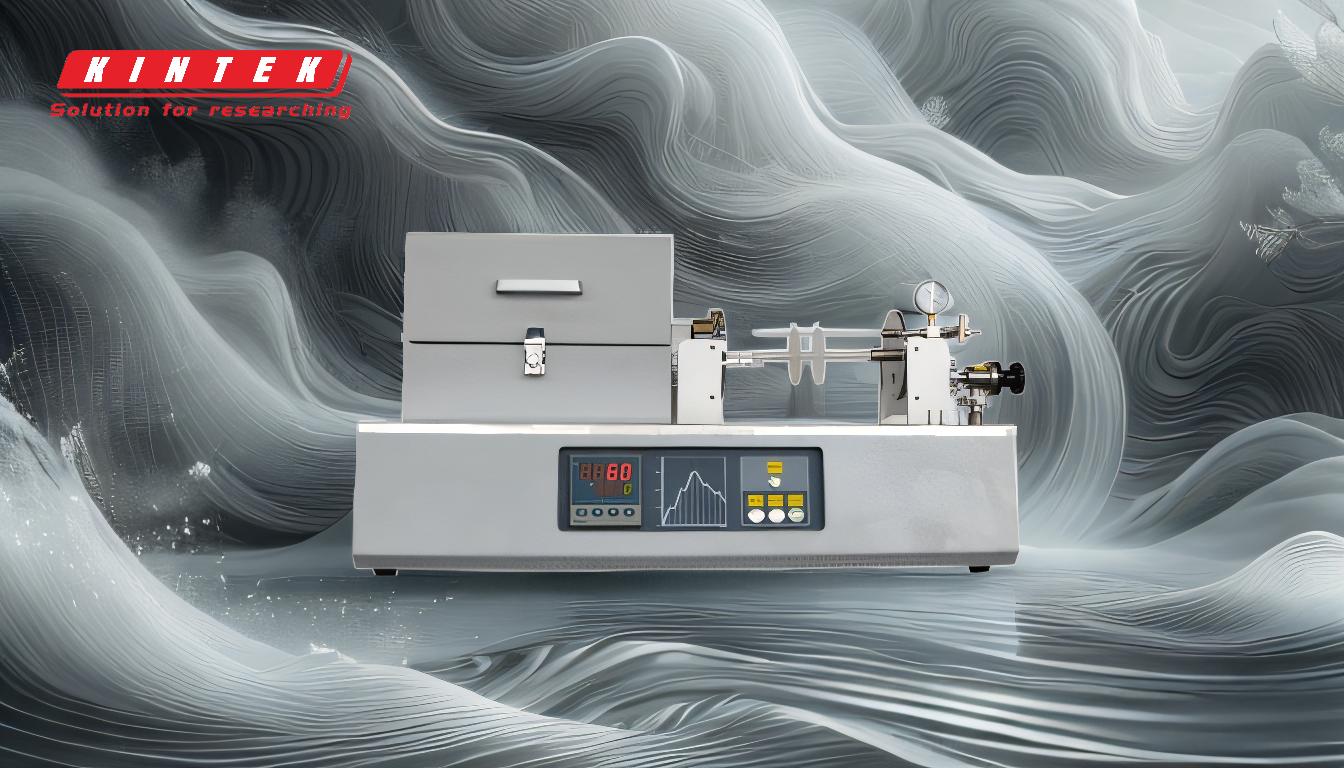
-
Purpose of Furnace Cooling:
- Furnace cooling is a critical step in the heat treatment process to achieve desired material properties such as hardness, strength, and ductility.
- It ensures that the metal cools uniformly, preventing defects like warping, cracking, or uneven microstructure.
-
Use of Inert Gases:
- Inert gases like argon are commonly used for cooling in vacuum furnaces.
- These gases are chemically inert, meaning they do not react with the metal, ensuring the material's integrity is maintained.
- The gas is pressurized and circulated through the furnace chamber to absorb heat from the workpiece.
-
Heat Exchange Mechanism:
- The absorbed heat is transferred to a heat exchanger, which removes the heat from the system.
- This allows for precise control over the cooling rate, ensuring the metal reaches the desired temperature without compromising its quality.
-
Cooling Methods:
- Controlled Cooling: A slower, more gradual cooling process that allows for the formation of specific microstructures, often used for materials requiring high toughness or ductility.
- Rapid Quenching: A faster cooling method used to achieve high hardness and strength, often employed for materials like tool steels or high-performance alloys.
-
Vacuum Furnace Cooling:
- In vacuum furnaces, cooling is achieved by introducing inert gases into the airtight chamber.
- This method allows for rapid and controlled cooling, ensuring the workpiece reaches the desired transformative temperature without oxidation or contamination.
-
Temperature and Time Considerations:
- Heat treatment processes can involve temperatures as high as 2,400°F, and cooling times can range from a few seconds to several hours, depending on the material and desired properties.
- The cooling rate must be carefully controlled to achieve the desired microstructure and mechanical properties.
-
Advantages of Furnace Cooling:
- Uniform Cooling: Ensures consistent material properties throughout the workpiece.
- Precision Control: Allows for precise adjustment of cooling rates to meet specific material requirements.
- Minimized Defects: Reduces the risk of warping, cracking, or other defects that can occur during uncontrolled cooling.
-
Applications:
- Furnace cooling is used in various industries, including aerospace, automotive, and tool manufacturing, where precise control over material properties is essential.
- It is particularly important for high-performance materials that require specific mechanical properties for their intended applications.
By understanding these key points, a purchaser can make informed decisions about the appropriate cooling methods and equipment needed for their specific heat treatment processes.
Summary Table:
Aspect | Details |
---|---|
Purpose | Achieve desired material properties like hardness, strength, and ductility. |
Inert Gases | Argon is used to absorb heat and ensure uniform cooling. |
Cooling Methods | Controlled cooling for toughness or rapid quenching for hardness. |
Temperature Range | Up to 2,400°F, with cooling times from seconds to hours. |
Advantages | Uniform cooling, precision control, and minimized defects. |
Applications | Aerospace, automotive, and tool manufacturing industries. |
Need help choosing the right furnace cooling method? Contact our experts today for tailored solutions!