Induction melting is a highly efficient and precise method of melting metals using electromagnetic induction. It involves passing an alternating current through an induction coil, which generates a magnetic field. When a conductive metal is placed within this field, eddy currents are induced in the metal, generating heat due to electrical resistance. This heat melts the metal, while the magnetic field also causes inductive stirring, ensuring uniform temperature and composition. The process is widely used in metallurgy for its ability to produce high-quality molten metal with minimal impurities and consistent properties.
Key Points Explained:
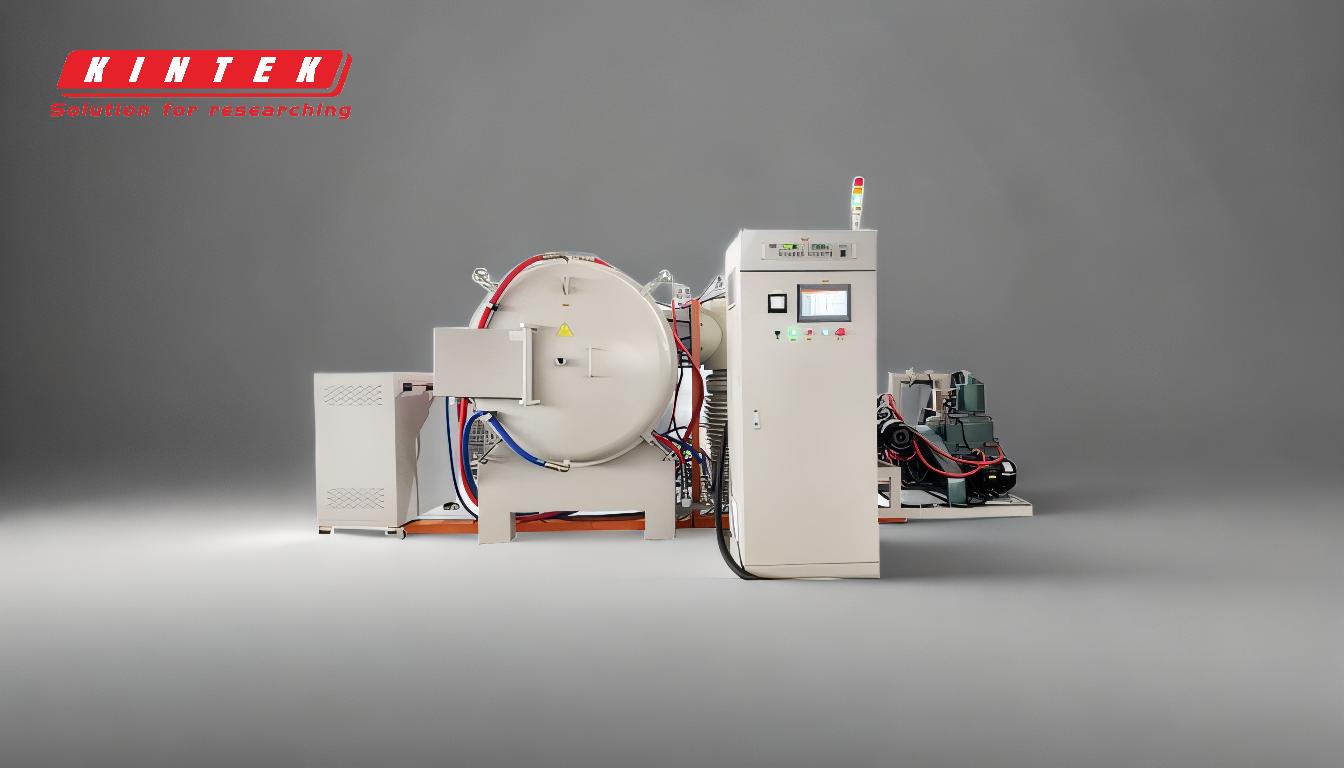
-
Electromagnetic Induction and Heat Generation:
- An alternating current (AC) flows through an induction coil, creating a fluctuating magnetic field.
- When a conductive metal (such as aluminum or steel) is placed within this field, Faraday’s Law of Induction causes eddy currents to flow within the metal.
- The resistance of the metal to these eddy currents generates heat through Joule heating (I²R heating), which raises the temperature of the metal until it melts.
-
Inductive Stirring:
- The alternating magnetic field not only heats the metal but also induces movement in the molten metal.
- This phenomenon, known as inductive or electromagnetic stirring, ensures uniform mixing of the molten metal.
- Stirring helps achieve consistent temperature distribution, reduces impurities, and facilitates alloying by evenly distributing added elements.
-
Components of an Induction Furnace:
- Induction Coil: Typically made of copper, the coil carries the alternating current and generates the magnetic field.
- Crucible: A container, often made of refractory materials, holds the metal being melted.
- Power Supply: Provides the high-frequency alternating current required for the process.
- Cooling System: Prevents the coil from overheating due to the high currents passing through it.
-
Advantages of Induction Melting:
- Precision and Control: The process allows for precise temperature control, which is critical for producing high-quality metal.
- Energy Efficiency: Induction melting is highly efficient, as heat is generated directly within the metal, minimizing energy loss.
- Cleanliness: The process produces less dross and impurities compared to traditional melting methods.
- Uniformity: Inductive stirring ensures consistent composition and temperature throughout the molten metal.
-
Applications of Induction Melting:
- Metallurgy: Used for melting and alloying metals such as steel, aluminum, copper, and precious metals.
- Foundries: Commonly employed in casting processes to produce components with precise specifications.
- Recycling: Ideal for melting and purifying scrap metal for reuse.
-
Process Steps in Induction Melting:
- Charging: The metal to be melted is placed inside the crucible.
- Heating: The induction coil generates heat, melting the metal.
- Stirring: The magnetic field induces movement, ensuring uniformity.
- Refining: Impurities are removed, and alloying elements are added if necessary.
- Casting: The molten metal is poured into molds or used for further processing.
-
Technical Considerations:
- Frequency of Alternating Current: Higher frequencies are used for smaller furnaces and lower frequencies for larger ones.
- Material Properties: The electrical conductivity and magnetic permeability of the metal affect the efficiency of the process.
- Temperature Control: Sensors and control systems are used to maintain the desired temperature throughout the process.
-
Comparison with Other Melting Methods:
- Induction Melting vs. Arc Melting: Induction melting is cleaner and more energy-efficient, while arc melting is better suited for very high temperatures.
- Induction Melting vs. Gas Furnaces: Induction melting offers better temperature control and uniformity, whereas gas furnaces are simpler and cheaper to operate.
By leveraging electromagnetic induction, induction melting provides a highly controlled and efficient method for melting metals, making it indispensable in modern metallurgy and manufacturing.
Summary Table:
Aspect | Details |
---|---|
Process | Uses electromagnetic induction to generate heat and melt metals. |
Key Components | Induction coil, crucible, power supply, and cooling system. |
Advantages | Precise control, energy efficiency, cleanliness, and uniformity. |
Applications | Metallurgy, foundries, and recycling. |
Comparison | Cleaner and more efficient than arc melting; better control than gas furnaces. |
Discover how induction melting can transform your metal processing—contact our experts today!