The relationship between pressure and deposition rate is complex and depends on the specific deposition process, such as plasma or sputter deposition. Higher gas pressure initially increases the deposition rate by providing more reaction gas in the unit, but excessive pressure reduces the mean free path of particles, hindering film coverage and quality. Conversely, low pressure can disrupt the deposition mechanism, leading to defects and reduced film density. Optimal pressure balances these factors, ensuring efficient ion bombardment, proper microstructure orientation, and desired film properties.
Key Points Explained:
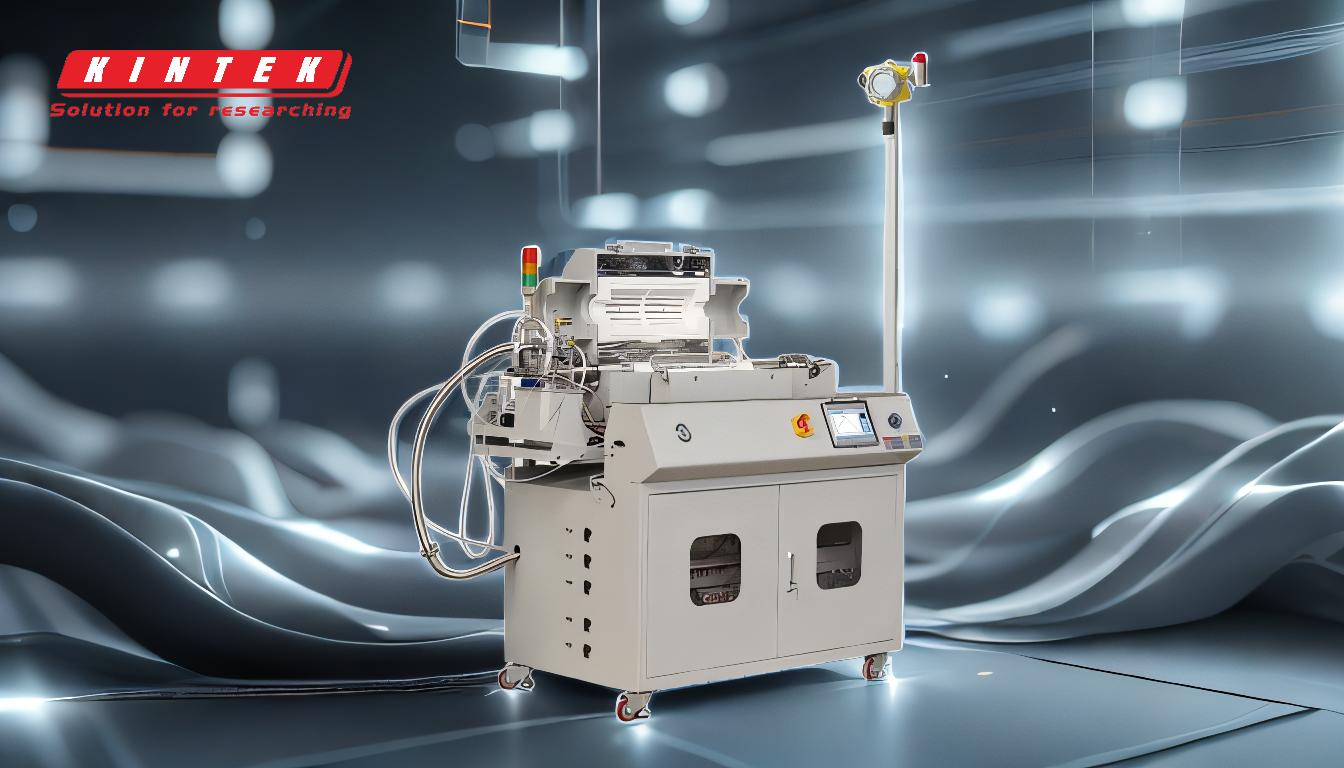
-
Initial Increase in Deposition Rate with Higher Pressure
- Higher gas pressure increases the concentration of reaction gases in the plasma or sputtering environment, enhancing the availability of reactive species for deposition.
- This leads to an initial increase in the deposition rate as more material is available to form the film.
-
Negative Effects of Excessive Pressure
- When gas pressure is too high, the mean free path of particles decreases.
- The mean free path is the average distance a particle travels before colliding with another particle. A shorter mean free path reduces the energy and directionality of particles reaching the substrate.
- This results in poor step coverage and uneven film growth, as particles lose kinetic energy and fail to reach all areas of the substrate uniformly.
- High pressure also enhances plasma polymerization, which can introduce defects and irregularities in the film structure.
- When gas pressure is too high, the mean free path of particles decreases.
-
Impact of Low Pressure on Deposition
- Insufficient gas pressure disrupts the deposition mechanism, leading to:
- Reduced film density due to insufficient ion bombardment and poor adatom mobility.
- Formation of needle-like defects, which compromise the film's structural integrity.
- Low pressure limits the availability of reactive species, slowing the deposition rate and potentially altering the film's composition.
- Insufficient gas pressure disrupts the deposition mechanism, leading to:
-
Role of Pressure in Microstructure Formation
- Gas pressure influences the kinetic energy of ions arriving at the substrate and the mean free path of particles.
- Higher kinetic energy promotes better adatom mobility, leading to denser and more uniform films.
- Pressure-induced changes in microstructure orientation can either enhance or reduce ion bombardment, affecting film quality.
- Gas pressure influences the kinetic energy of ions arriving at the substrate and the mean free path of particles.
-
Pressure as a Decisive Process Parameter
- In sputter deposition, pressure governs the energy distribution of source atoms by controlling the mean free path.
- It is a critical parameter that must be optimized alongside temperature and power to achieve the desired deposition rate and film properties.
-
Interaction with Other Deposition Parameters
- Deposition rate and film quality are also influenced by factors such as:
- Target-substrate distance: Closer distances increase deposition rates but may reduce uniformity.
- Power and temperature: Higher power and temperature generally increase deposition rates but must be balanced with pressure to avoid defects.
- Deposition rate and film quality are also influenced by factors such as:
-
Importance of Monitoring Plasma Characteristics
- The plasma's temperature, composition, and density are strongly influenced by pressure.
- Monitoring these characteristics ensures the correct elemental composition and minimizes contamination, which can affect deposition rates and film quality.
-
Balancing Pressure for Optimal Deposition
- The optimal pressure range depends on the specific deposition process and desired film properties.
- It must balance the trade-offs between increasing reaction gas availability, maintaining adequate mean free path, and ensuring proper ion bombardment and adatom mobility.
In summary, pressure plays a critical role in determining deposition rates and film quality. While higher pressure initially boosts deposition rates by increasing reaction gas availability, excessive pressure reduces particle energy and disrupts film growth. Conversely, low pressure can lead to defects and poor film density. Optimal pressure ensures efficient ion bombardment, proper microstructure formation, and high-quality film deposition. Balancing pressure with other parameters like temperature, power, and target-substrate distance is essential for achieving desired outcomes in deposition processes.
Summary Table:
Pressure Level | Effect on Deposition Rate | Impact on Film Quality |
---|---|---|
High Pressure | Increases initially | Poor step coverage, defects |
Low Pressure | Reduces deposition rate | Needle-like defects, low density |
Optimal Pressure | Balances rate and quality | Dense, uniform films |
Need help optimizing your deposition process? Contact our experts today for tailored solutions!