Pressure plays a significant role in the pyrolysis process, influencing the yield, composition, and properties of the resulting products. While the references provided do not explicitly detail the effects of pressure, we can infer its impact based on general principles of pyrolysis and related chemical processes. Below is a detailed explanation of how pressure affects pyrolysis, structured for clarity and depth.
Key Points Explained:
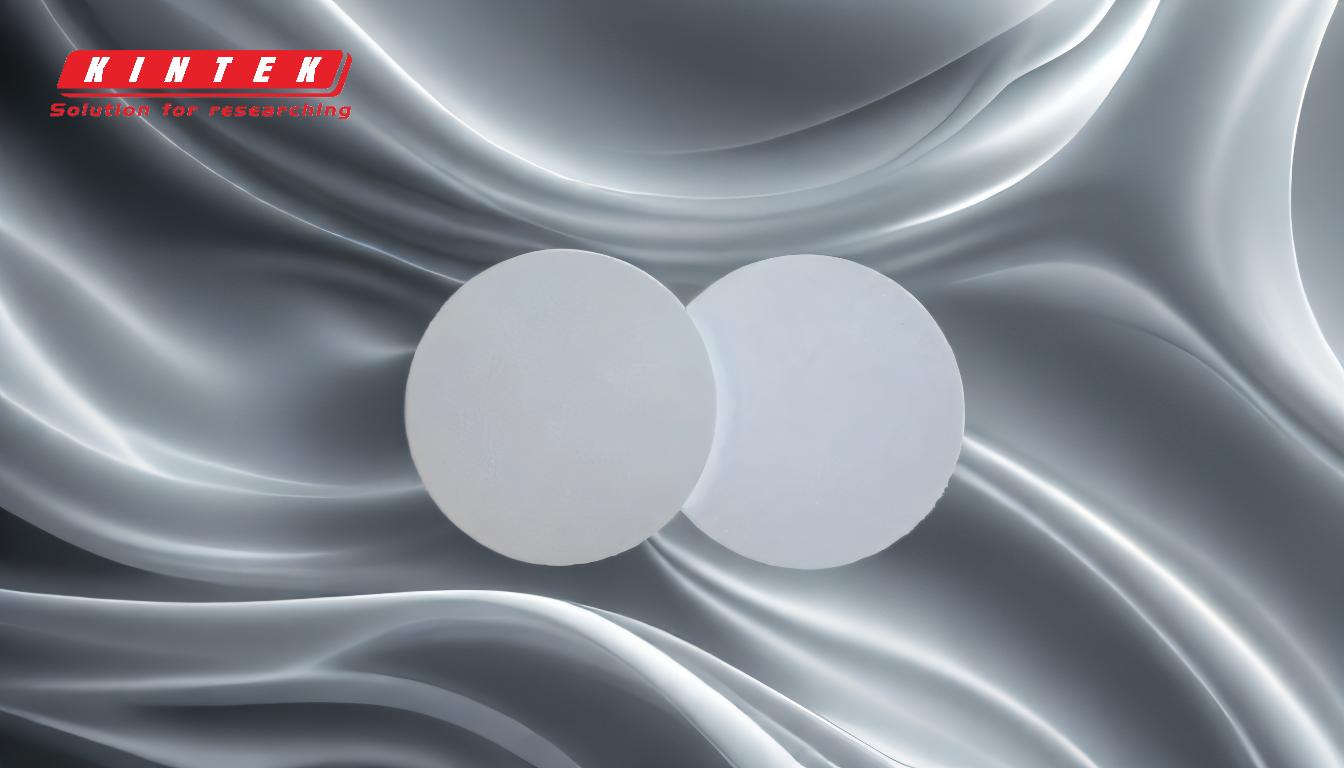
-
Effect on Reaction Kinetics
- Increased Pressure: Higher pressure can accelerate the rate of pyrolysis reactions by increasing the collision frequency between molecules. This can lead to faster decomposition of biomass into volatiles, char, and gases.
- Reduced Pressure: Lower pressure may slow down the reaction kinetics, as fewer molecular collisions occur. This can result in incomplete pyrolysis or a shift in product distribution toward more solid residues.
-
Influence on Product Distribution
- Gas Production: Higher pressure tends to favor the formation of non-condensable gases (e.g., methane, hydrogen, and carbon monoxide) due to increased cracking of heavier molecules.
- Liquid and Tar Formation: Lower pressure conditions may promote the production of bio-oil and tars, as volatiles have a higher chance of condensing before escaping the reactor.
- Char Yield: Pressure can affect char formation by altering the secondary reactions of volatiles. Higher pressure may lead to more char due to increased repolymerization of intermediate compounds.
-
Impact on Secondary Reactions
- Volatile Residence Time: Pressure influences the residence time of volatiles in the reactor. Higher pressure can extend the residence time, allowing for more secondary reactions (e.g., cracking, repolymerization) that modify the final product composition.
- Tar Cracking: Elevated pressure can enhance tar cracking, reducing the amount of tar and increasing gas yields.
-
Thermodynamic Considerations
- Energy Requirements: Higher pressure may increase the energy requirements for pyrolysis due to the need to overcome the pressure-volume work. This can affect the overall efficiency of the process.
- Equilibrium Shifts: Pressure can shift chemical equilibria, favoring certain reactions over others. For example, higher pressure may favor exothermic reactions that produce gases.
-
Reactor Design and Operation
- Pressure Control: The ability to control pressure in a pyrolysis reactor is crucial for optimizing product yields and quality. Reactors designed for high-pressure operation may require more robust materials and safety measures.
- Feedstock Compatibility: Different feedstocks may respond differently to pressure changes. For example, denser materials like tires may require higher pressures for effective pyrolysis compared to lighter biomass.
-
Practical Implications for Equipment and Consumables
- Reactor Selection: Purchasers should consider the pressure range of pyrolysis reactors when selecting equipment, as it directly impacts product outcomes.
- Safety and Maintenance: High-pressure systems may require additional safety features and maintenance, increasing operational costs.
- Product Quality: Understanding the relationship between pressure and product distribution can help purchasers choose systems that align with their desired outputs (e.g., gas, oil, or char).
By considering these key points, purchasers and operators can make informed decisions about the role of pressure in pyrolysis and its implications for equipment selection, process optimization, and product quality.
Summary Table:
Aspect | High Pressure | Low Pressure |
---|---|---|
Reaction Kinetics | Accelerates pyrolysis reactions, faster decomposition into volatiles, char, gases | Slows reaction kinetics, may lead to incomplete pyrolysis or more solid residues |
Product Distribution | Favors non-condensable gases (e.g., methane, hydrogen) | Promotes bio-oil and tar formation |
Char Yield | Increases char due to repolymerization | May reduce char yield |
Secondary Reactions | Enhances tar cracking, increases gas yields | Extends volatile residence time, modifies product composition |
Energy Requirements | Higher energy needed for pressure-volume work | Lower energy requirements |
Reactor Design | Requires robust materials, safety measures | Less demanding on reactor design |
Ready to optimize your pyrolysis process? Contact our experts today for tailored solutions!