Quenching in chemistry is a rapid cooling process used to alter the microstructure of materials, particularly metals and fine ceramics, to achieve desired mechanical properties. This process involves heating the material to a specific temperature and then rapidly cooling it, often using water, oil, or air. The rapid cooling prevents the formation of equilibrium phases, leading to a hardened structure. Quenching is crucial in materials science for enhancing hardness, strength, and wear resistance, but it must be carefully controlled to avoid issues like cracking or distortion.
Key Points Explained:
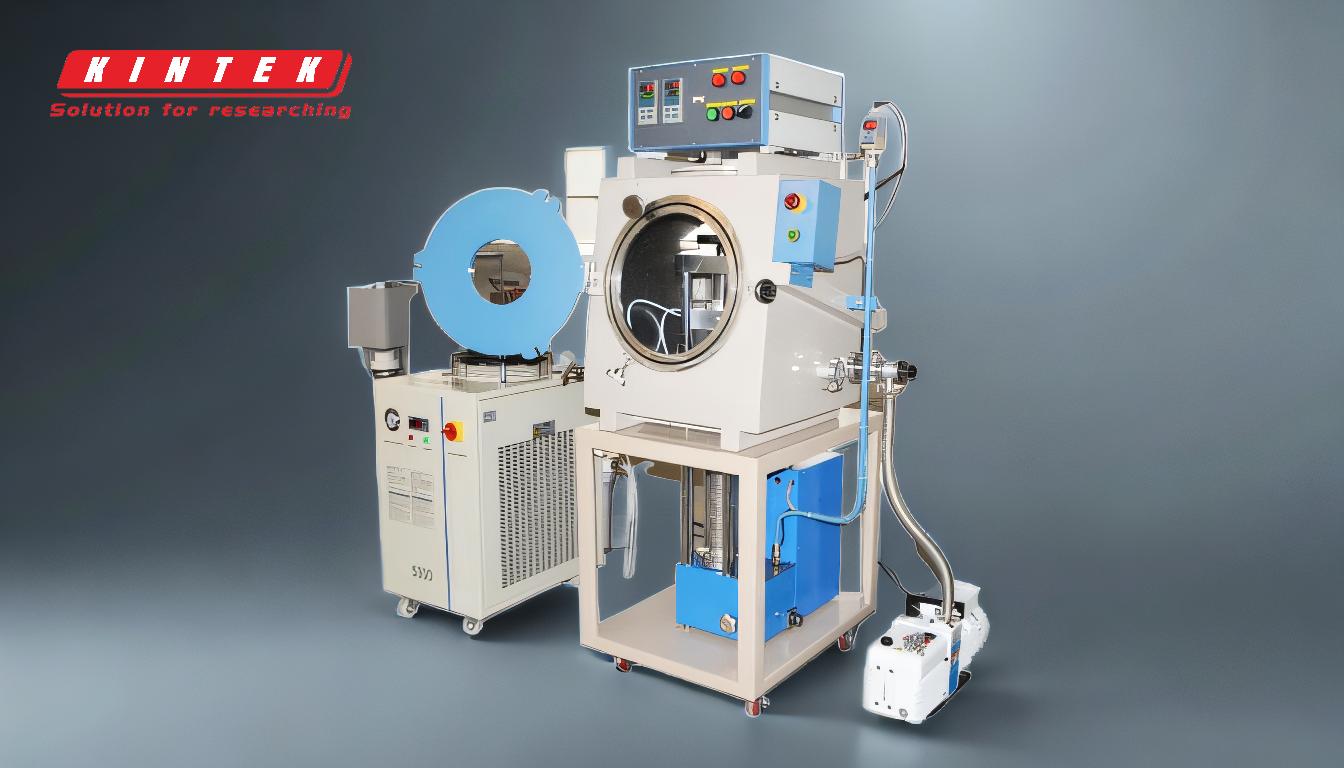
-
Definition and Purpose of Quenching:
- Quenching is a heat treatment process where a material is heated to a high temperature and then rapidly cooled. This rapid cooling is essential to achieve a non-equilibrium microstructure, which enhances the material's mechanical properties such as hardness and strength.
- For fine ceramics, quenching can help in achieving a dense and uniform microstructure, which is critical for their performance in high-temperature and high-stress applications.
-
Mechanism of Quenching:
- During quenching, the material is heated to a temperature where its microstructure becomes austenitic (for metals) or amorphous (for ceramics). Rapid cooling then prevents the formation of equilibrium phases, leading to a hardened structure.
- The cooling rate is critical; too slow, and the material will not harden sufficiently, too fast, and it may crack or distort.
-
Role of Cooling Medium:
- The choice of cooling medium (water, oil, air, etc.) depends on the material and the desired properties. Water provides the fastest cooling rate, making it suitable for hardening steels, while oil and air are used for materials that require a slower cooling rate to prevent cracking.
- For fine ceramics, the cooling medium must be carefully selected to avoid thermal shock, which can cause cracking.
-
Controlled Atmosphere in Quenching:
- A controlled atmosphere is often used during quenching to prevent oxidation and decarburization. This is particularly important for metals but can also be relevant for fine ceramics, where surface reactions can affect the material's properties.
- The controlled atmosphere ensures that the material's surface remains free from unwanted reactions, preserving its integrity and performance.
-
Applications in Fine Ceramics:
- Quenching is used in the production of fine ceramics to achieve specific microstructures that enhance their mechanical and thermal properties. For example, quenching can be used to create a dense, fine-grained structure that improves the ceramic's strength and resistance to thermal shock.
- The process must be carefully controlled to avoid defects such as cracking or warping, which can compromise the ceramic's performance.
-
Challenges and Considerations:
- One of the main challenges in quenching is controlling the cooling rate to achieve the desired properties without introducing defects. This requires precise control of the quenching process, including the temperature, cooling medium, and atmosphere.
- For fine ceramics, additional considerations include the material's thermal conductivity and thermal expansion coefficient, which can affect how the material responds to rapid cooling.
-
Future Directions:
- Research is ongoing to develop new quenching techniques and cooling media that can provide better control over the material's microstructure and properties. This includes the use of advanced cooling methods such as cryogenic quenching and the development of new ceramic materials with improved thermal and mechanical properties.
- The integration of quenching with other processes, such as sintering, is also being explored to further enhance the performance of fine ceramics.
In summary, quenching is a critical process in materials science, particularly for fine ceramics, where it is used to achieve specific microstructures that enhance mechanical and thermal properties. The process involves rapid cooling from a high temperature, and it must be carefully controlled to avoid defects and ensure the desired outcome.
Summary Table:
Aspect | Details |
---|---|
Definition | Rapid cooling process to alter material microstructure. |
Purpose | Enhances hardness, strength, and wear resistance. |
Cooling Mediums | Water (fastest), oil, air (slower for delicate materials). |
Applications | Metals, fine ceramics for high-temperature and high-stress environments. |
Challenges | Controlling cooling rate to avoid cracking or distortion. |
Future Directions | Advanced cooling methods like cryogenic quenching and new ceramic materials. |
Learn how quenching can optimize your material properties—contact our experts today!