Temperature plays a critical role in determining the deposition rate and the resulting film properties during thin-film deposition processes. While the deposition rate itself may not always be strongly dependent on temperature, especially in processes like Plasma-Enhanced Chemical Vapor Deposition (PE-CVD), the film's characteristics, such as composition, stress, and morphology, are significantly influenced by temperature. Additionally, the application-specific requirements often dictate the permissible temperature range for deposition, as higher temperatures can alter film properties or damage sensitive substrates. Understanding the relationship between temperature and deposition rate is essential for optimizing film quality and process efficiency.
Key Points Explained:
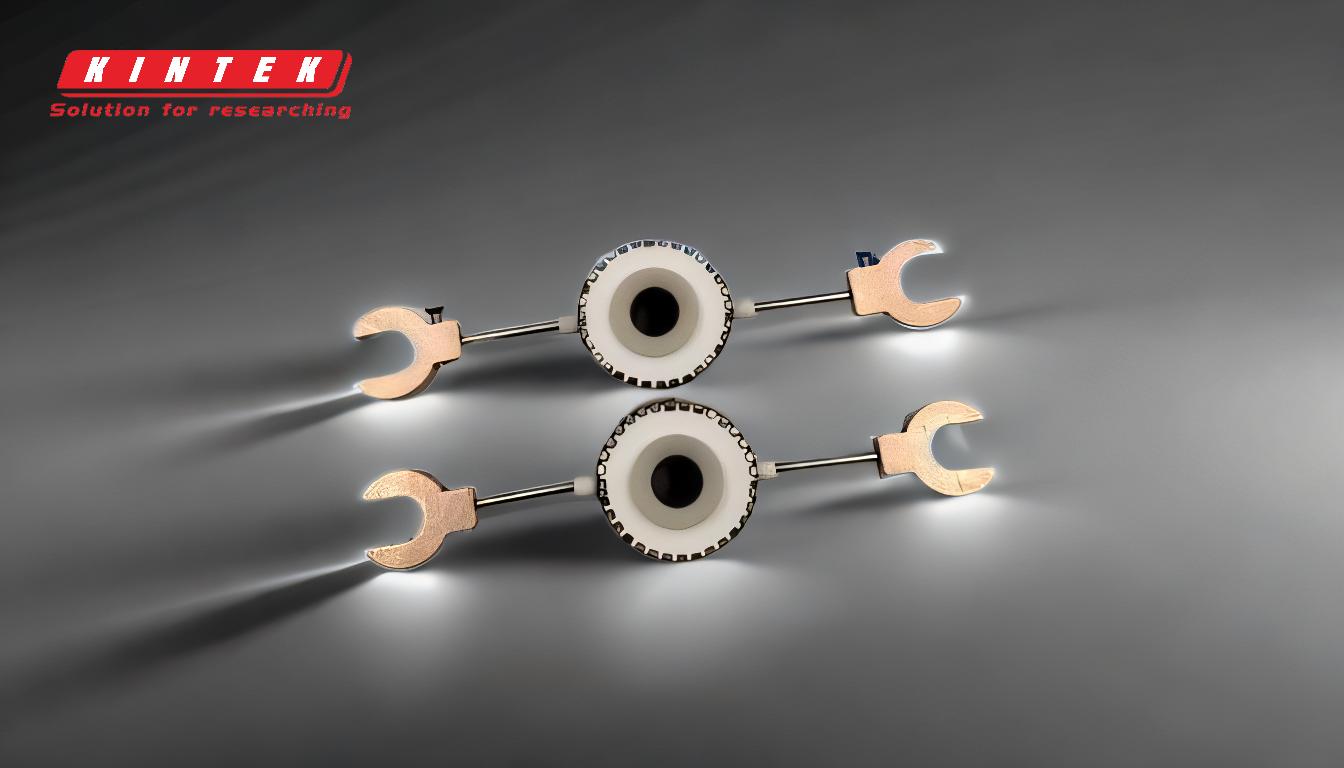
-
Temperature's Role in Deposition Processes:
- Temperature is a critical parameter in thin-film deposition, influencing both the rate and quality of the deposited film.
- In some processes, such as PE-CVD, the deposition rate may not be strongly dependent on temperature due to low surface activation energies. However, temperature still affects film properties like composition, stress, and morphology.
-
Measurement of Deposition Temperature:
- Accurate temperature measurement is essential for controlling the deposition process. For example, a two-color infrared ratio thermometer can be used to measure the deposition temperature. This method focuses thermal emission through a quartz window at a specific angle, ensuring precise temperature readings even for small target areas (minimum 2 mm in diameter).
-
Impact of Temperature on Film Characteristics:
- Temperature significantly affects the film's characteristics, such as its composition, stress levels, and morphology. Higher temperatures can lead to denser films with reduced stress but may also cause unwanted changes in composition or damage to temperature-sensitive substrates.
- The application often imposes limits on the deposition temperature to ensure the film meets specific performance criteria.
-
Application-Specific Temperature Constraints:
- The choice of deposition temperature is often constrained by the application. For instance, in semiconductor manufacturing, excessive temperatures can damage delicate substrates or alter the electrical properties of the film.
- Balancing temperature to achieve optimal deposition rates while maintaining desired film properties is a key challenge in process optimization.
-
Optimization of Deposition Processes:
- Understanding the relationship between temperature and deposition rate allows for better process control. By adjusting temperature within the permissible range, manufacturers can achieve the desired film properties while maintaining efficient deposition rates.
- Advanced techniques, such as real-time temperature monitoring and feedback control, can further enhance process stability and film quality.
By carefully controlling and monitoring temperature during deposition, manufacturers can optimize both the deposition rate and the resulting film properties, ensuring that the final product meets the stringent requirements of its intended application.
Summary Table:
Key Aspect | Details |
---|---|
Temperature's Role | Influences deposition rate and film quality; affects composition, stress, and morphology. |
Measurement Techniques | Use tools like two-color infrared ratio thermometers for precise readings. |
Impact on Film Characteristics | Higher temperatures can densify films but may damage sensitive substrates. |
Application Constraints | Temperature limits are often set by application-specific requirements. |
Process Optimization | Adjust temperature for optimal deposition rates and desired film properties. |
Optimize your thin-film deposition process today—contact our experts for guidance!