The electron beam works by generating and manipulating free electrons in a vacuum environment to produce a concentrated beam of energy. This beam is created by heating a filament to release electrons, which are then accelerated through a vacuum tube using a voltage gradient. The beam can be precisely controlled using electric and magnetic fields, allowing it to be directed at specific targets. When the electron beam collides with solid-state matter, the energy is converted into heat or kinetic energy, making it highly effective for applications such as thin-film coating, where it heats an evaporant to produce a vapor stream that condenses on a substrate.
Key Points Explained:
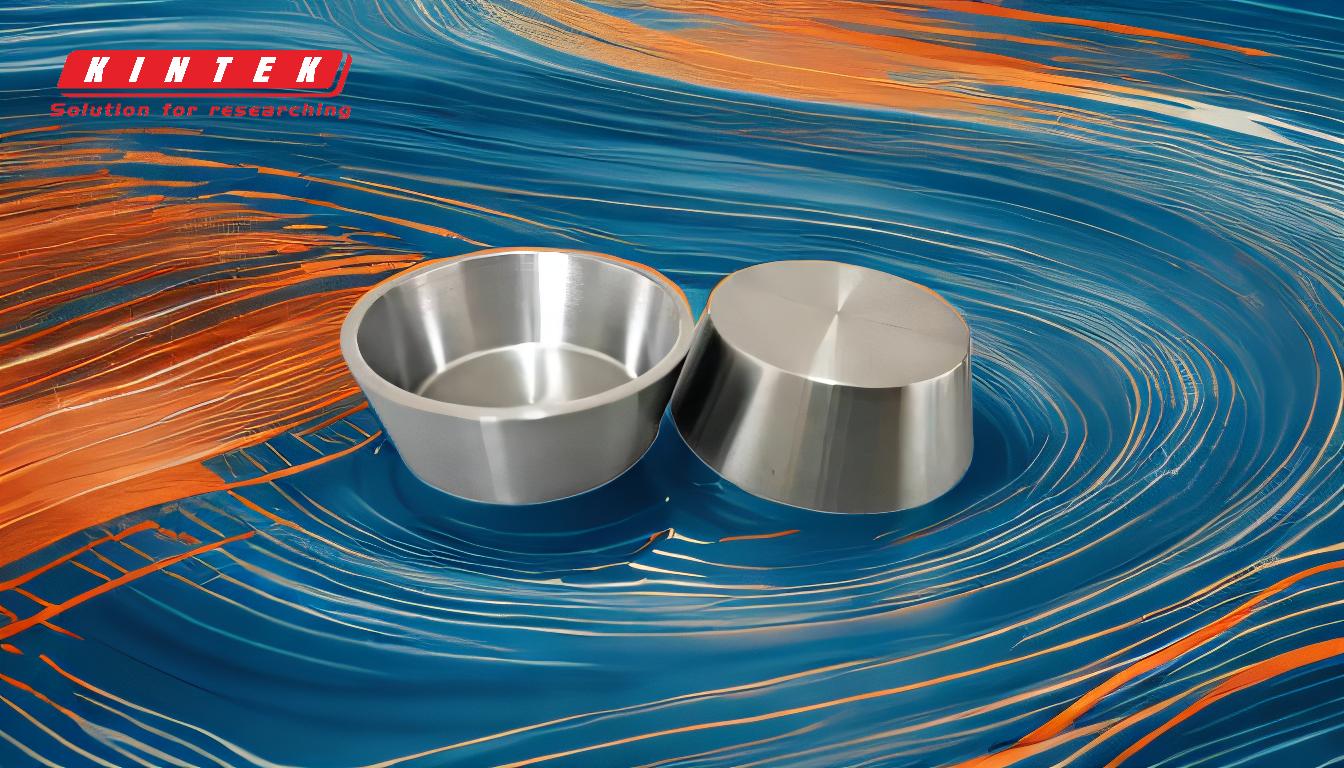
-
Generation of Electrons:
- Electrons are generated by heating a filament, typically made of tungsten or another high-melting-point material. The heat causes thermionic emission, releasing free electrons into the surrounding space.
- This process occurs in a vacuum to prevent collisions with gas molecules, ensuring the electrons can travel unimpeded.
-
Acceleration of Electrons:
- A voltage gradient is applied to draw the electrons away from the filament and accelerate them through a vacuum tube. The high voltage (often in the range of kilovolts) gives the electrons significant kinetic energy.
- The vacuum environment is crucial as it minimizes energy loss due to collisions with air molecules, ensuring the electron beam remains focused and powerful.
-
Formation of the Electron Beam:
- The accelerated electrons form a fine beam, which can be further shaped and directed using electric and magnetic fields. These fields allow for precise control over the beam's trajectory and focus.
- The beam can be scanned or deflected using electromagnets, creating a "curtain" of electrons that can cover a larger area or be directed at specific points.
-
Interaction with Matter:
- When the electron beam collides with solid-state matter, the kinetic energy of the electrons is converted into heat or kinetic energy in the target material. This localized heating can be used to evaporate materials in processes like thin-film coating.
- The energy transfer is highly efficient and can be precisely controlled, making electron beams ideal for applications requiring fine detail and high energy concentration.
-
Applications in Thin-Film Coating:
- In electron beam coating, the beam is directed at a crucible containing the material to be evaporated (the evaporant). The intense heat generated by the electron beam causes the evaporant to vaporize.
- The vapor stream then condenses on a substrate, forming a thin, uniform film. This process is widely used in industries such as optics, electronics, and aerospace for creating high-quality coatings.
-
Advantages of Electron Beam Technology:
- Precision: The electron beam can be precisely controlled electronically, allowing for accurate targeting and energy delivery.
- Efficiency: The high energy density of the beam ensures rapid and efficient heating of the target material.
- Versatility: Electron beams can be used for a wide range of applications, from material processing to sterilization and surface modification.
- Cleanliness: The vacuum environment prevents contamination, ensuring high-purity results in processes like thin-film deposition.
By understanding these key points, it becomes clear how electron beams function as a powerful and versatile tool in modern technology, particularly in applications requiring precise energy delivery and high-quality material processing.
Summary Table:
Key Aspect | Details |
---|---|
Generation of Electrons | Heating a tungsten filament in a vacuum releases free electrons via thermionic emission. |
Acceleration of Electrons | High voltage gradients accelerate electrons through a vacuum tube, ensuring minimal energy loss. |
Beam Formation | Electric and magnetic fields shape and direct the beam for precise targeting. |
Interaction with Matter | Electron beams convert kinetic energy into heat, ideal for processes like thin-film coating. |
Applications | Used in optics, electronics, and aerospace for high-quality coatings and material processing. |
Advantages | Precision, efficiency, versatility, and cleanliness in a vacuum environment. |
Discover how electron beam technology can revolutionize your processes—contact us today to learn more!