Vacuum deposition is a precise and versatile technique used to deposit thin films of material onto a substrate at the atomic or molecular level. This process is conducted in a vacuum or low-pressure environment to minimize interference from gas molecules, ensuring high-quality, uniform coatings. The key steps involve creating a vacuum, preparing the substrate, evaporating or sputtering the coating material, and depositing it onto the substrate. Common methods include physical vapor deposition (PVD), low-pressure chemical vapor deposition (LPCVD), and low-pressure plasma spraying (LPPS). These methods allow for the creation of films ranging from nanometers to millimeters in thickness, with applications in electronics, optics, and protective coatings.
Key Points Explained:
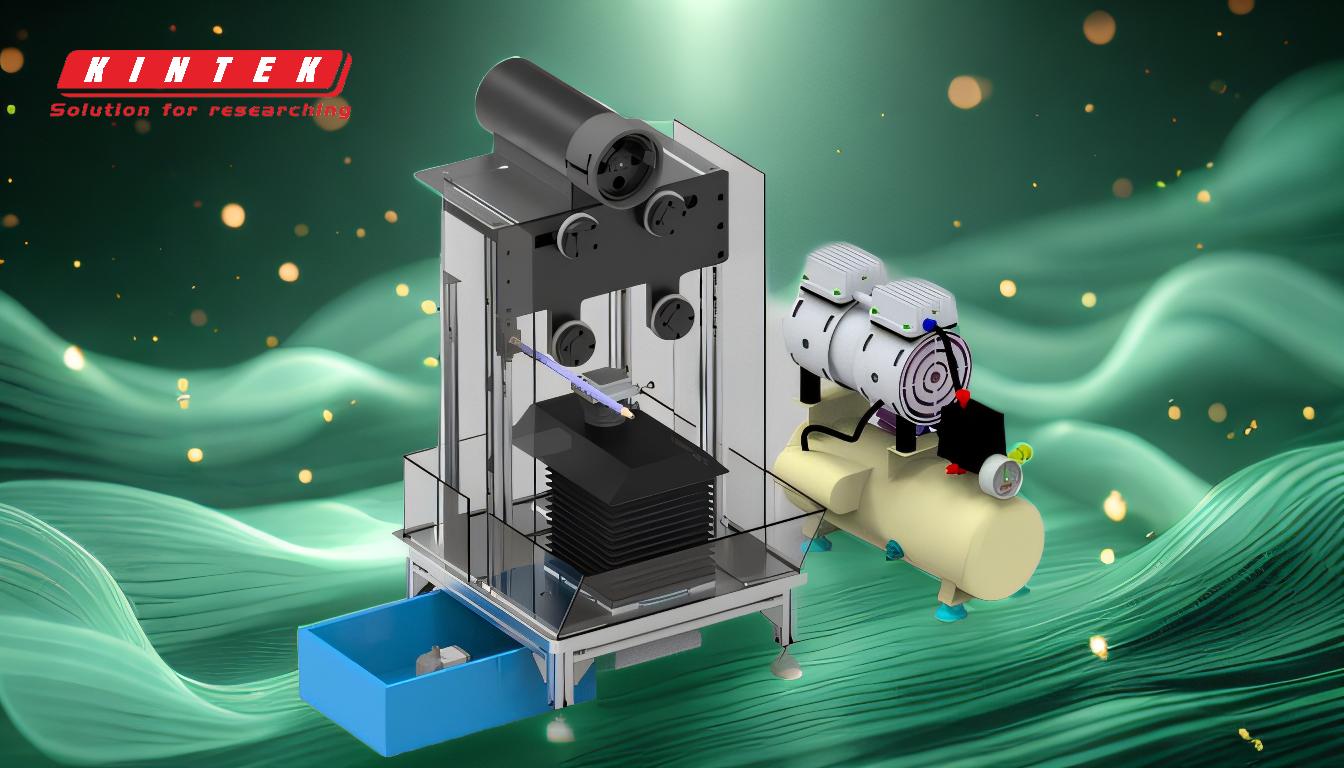
-
What is Vacuum Deposition?
- Vacuum deposition is a family of processes used to deposit thin layers of material onto a solid surface at the atomic or molecular level. This is achieved in a vacuum or low-pressure environment to ensure the purity and uniformity of the deposited film.
- The process is highly controlled, allowing for the deposition of films with thicknesses ranging from a single atom to several millimeters.
-
Key Processes in Vacuum Deposition:
- Physical Vapor Deposition (PVD): This process involves the physical transfer of material from a source to the substrate. Common PVD techniques include evaporation and sputtering. In evaporation, the material is heated until it vaporizes and then condenses on the substrate. In sputtering, high-energy ions knock atoms off a target material, which then deposit onto the substrate.
- Low-Pressure Chemical Vapor Deposition (LPCVD): This process involves the chemical reaction of gaseous precursors at low pressure to form a solid film on the substrate. LPCVD is often used for depositing materials like silicon dioxide and silicon nitride in semiconductor manufacturing.
- Low-Pressure Plasma Spraying (LPPS): This technique uses a plasma torch to melt and spray material onto the substrate in a low-pressure environment. LPPS is commonly used for depositing thermal barrier coatings and other high-performance materials.
-
Steps in the Vacuum Deposition Process:
- Creating a Vacuum: The first step is to create a vacuum in the deposition chamber. This is done to remove air and other gases that could interfere with the deposition process, ensuring a clean environment for the material to be deposited.
- Substrate Preparation: The substrate, or the surface to be coated, must be thoroughly cleaned and sometimes treated to ensure good adhesion of the deposited material. This may involve chemical cleaning, plasma treatment, or other surface preparation techniques.
- Evaporation or Sputtering: The coating material is then either evaporated or sputtered. In evaporation, the material is heated until it turns into vapor, which then condenses on the substrate. In sputtering, high-energy ions are used to knock atoms off a target material, which then deposit onto the substrate.
- Deposition: The vaporized or sputtered material is deposited onto the substrate, forming a thin film. The deposition process is carefully controlled to achieve the desired thickness and uniformity.
- Cooling and Venting: After the deposition is complete, the chamber is cooled down and vented to atmospheric pressure. The coated substrate is then removed for further processing or use.
-
Advantages of Vacuum Deposition:
- High Purity: The vacuum environment minimizes contamination, resulting in high-purity films.
- Precision: The process allows for precise control over film thickness and composition, making it ideal for applications requiring nanometer-scale accuracy.
- Versatility: Vacuum deposition can be used with a wide range of materials, including metals, ceramics, and polymers, and is applicable to various industries such as electronics, optics, and aerospace.
-
Applications of Vacuum Deposition:
- Electronics: Vacuum deposition is widely used in the semiconductor industry to deposit thin films of materials like silicon, silicon dioxide, and metals for integrated circuits and other electronic components.
- Optics: The process is used to create anti-reflective coatings, mirrors, and other optical components with precise optical properties.
- Protective Coatings: Vacuum deposition is used to apply hard, wear-resistant coatings to tools, medical devices, and other components that require enhanced durability.
-
Challenges and Considerations:
- Cost: The equipment and maintenance required for vacuum deposition can be expensive, making it less suitable for low-cost applications.
- Complexity: The process requires careful control of many parameters, including vacuum level, temperature, and deposition rate, which can be complex and time-consuming.
- Material Limitations: While vacuum deposition is versatile, not all materials are suitable for deposition using this method, and some may require specialized techniques or equipment.
In summary, vacuum deposition is a highly controlled and versatile process used to deposit thin films of material onto a substrate in a vacuum or low-pressure environment. The process involves several key steps, including creating a vacuum, preparing the substrate, evaporating or sputtering the coating material, and depositing it onto the substrate. Common methods include PVD, LPCVD, and LPPS, each with its own advantages and applications. Despite its complexity and cost, vacuum deposition is widely used in industries such as electronics, optics, and aerospace due to its ability to produce high-purity, precise, and durable coatings.
Summary Table:
Key Aspect | Details |
---|---|
Definition | A process to deposit thin films at the atomic/molecular level in a vacuum. |
Key Methods | PVD, LPCVD, LPPS |
Steps | Create vacuum, prepare substrate, evaporate/sputter, deposit, cool/vent. |
Advantages | High purity, precision, versatility. |
Applications | Electronics, optics, protective coatings. |
Challenges | High cost, complexity, material limitations. |
Discover how vacuum deposition can enhance your projects—contact us today for expert guidance!