Induction furnaces generate heat through the principle of electromagnetic induction. When an alternating current (AC) passes through the induction coil, it creates a rapidly alternating magnetic field. This magnetic field penetrates the metal charge placed inside the furnace, inducing eddy currents within the material. These eddy currents flow through the resistance of the metal, generating heat via Joule heating. The process is efficient and allows for precise temperature control, making it ideal for melting and heating metals. The use of advanced components like IGBT induction furnaces enhances the efficiency and performance of these systems.
Key Points Explained:
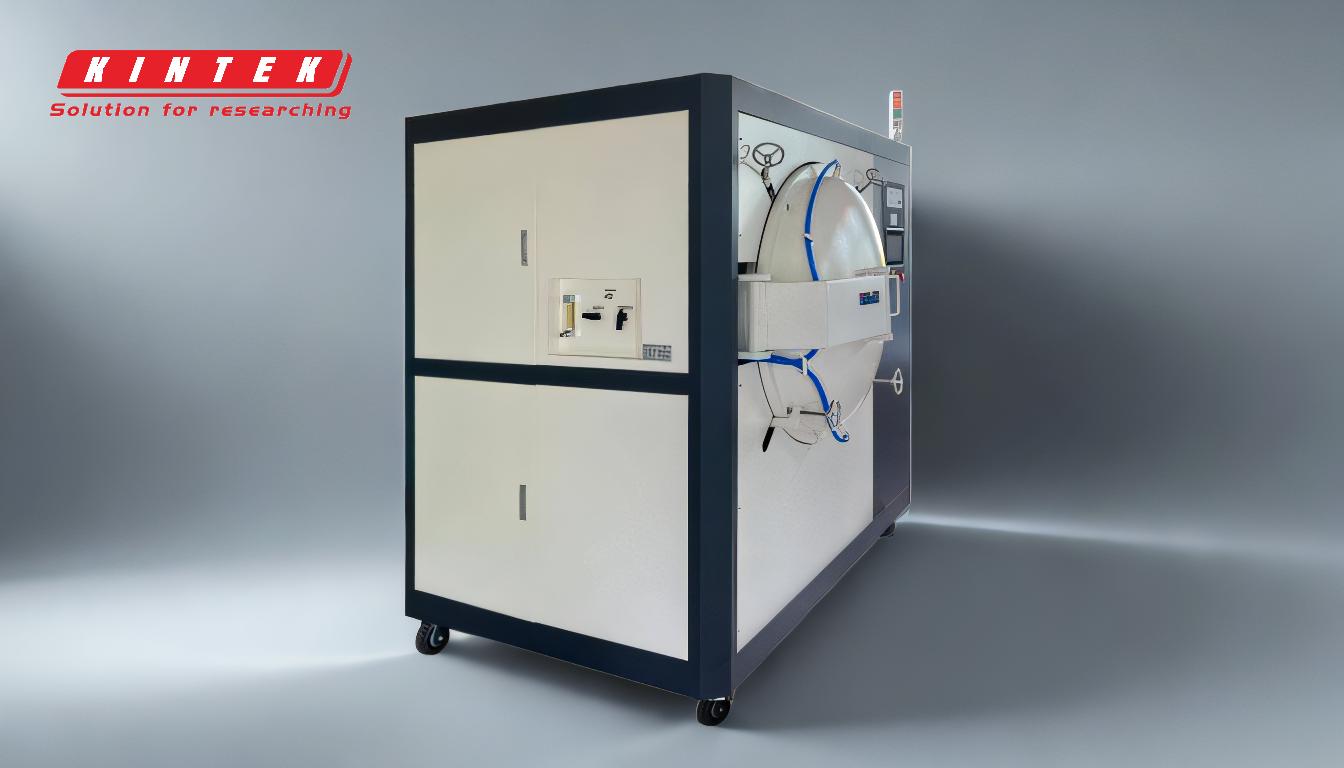
-
Principle of Electromagnetic Induction:
- An induction furnace operates on the principle of electromagnetic induction. When an AC power supply is connected to the induction coil, it generates an alternating magnetic field.
- This magnetic field penetrates the metal charge placed inside the furnace, inducing electric currents known as eddy currents within the material.
-
Generation of Eddy Currents:
- The alternating magnetic field causes the magnetic lines to cut through the metal charge, inducing an electromotive force (EMF).
- Since the metal charge forms a closed circuit, this EMF generates eddy currents that flow through the resistance of the metal.
-
Joule Heating:
- The eddy currents encounter resistance as they flow through the metal, leading to the generation of heat. This process is known as Joule heating.
- The heat generated is proportional to the square of the current and the resistance of the material, ensuring efficient and uniform heating.
-
Role of the Induction Coil:
- The induction coil is a crucial component that creates the alternating magnetic field. It is typically made of copper and is designed to withstand high temperatures and electrical loads.
- The coil's design and the frequency of the AC power supply can be adjusted to optimize the heating process for different materials and applications.
-
Advantages of Induction Heating:
- Induction heating is highly efficient, as it directly heats the metal charge without the need for a separate heating element.
- It allows for precise temperature control, rapid heating, and minimal heat loss, making it ideal for applications requiring high temperatures and uniformity.
-
Use of IGBT Technology:
- Modern induction furnaces often utilize IGBT induction furnaces, which employ Insulated Gate Bipolar Transistors (IGBTs) for power control.
- IGBTs offer improved efficiency, faster switching speeds, and better control over the heating process, enhancing the overall performance of the furnace.
-
Applications of Induction Furnaces:
- Induction furnaces are widely used in metal melting, heat treatment, and forging processes.
- They are particularly suitable for applications requiring high purity and precise temperature control, such as in the production of specialty alloys and semiconductors.
By understanding these key points, one can appreciate the efficiency and precision of induction furnaces in generating heat for various industrial applications. The integration of advanced technologies like IGBTs further enhances their performance, making them a preferred choice in modern metallurgical processes.
Summary Table:
Key Aspect | Description |
---|---|
Principle | Electromagnetic induction generates an alternating magnetic field. |
Eddy Currents | Magnetic field induces eddy currents in the metal charge. |
Joule Heating | Eddy currents flow through metal resistance, generating heat. |
Induction Coil | Copper coil creates the magnetic field; adjustable for optimal heating. |
Advantages | High efficiency, precise temperature control, and minimal heat loss. |
IGBT Technology | Enhances efficiency and control with faster switching speeds. |
Applications | Metal melting, heat treatment, forging, and specialty alloy production. |
Upgrade your metal processing with advanced induction furnaces—contact us today for expert advice!