Brazing is a critical joining process in the automotive industry, used to create strong, durable, and leak-proof bonds between metal components. It is particularly favored for its ability to join dissimilar metals, withstand high temperatures, and provide excellent corrosion resistance. In automotive applications, brazing is commonly used in the manufacturing of heat exchangers, fuel systems, exhaust systems, and electrical components. The process involves heating the base metals to a temperature above 450°C (842°F) but below their melting points, using a filler metal that melts and flows into the joint by capillary action. This results in a robust, high-integrity bond that meets the demanding performance requirements of automotive systems.
Key Points Explained:
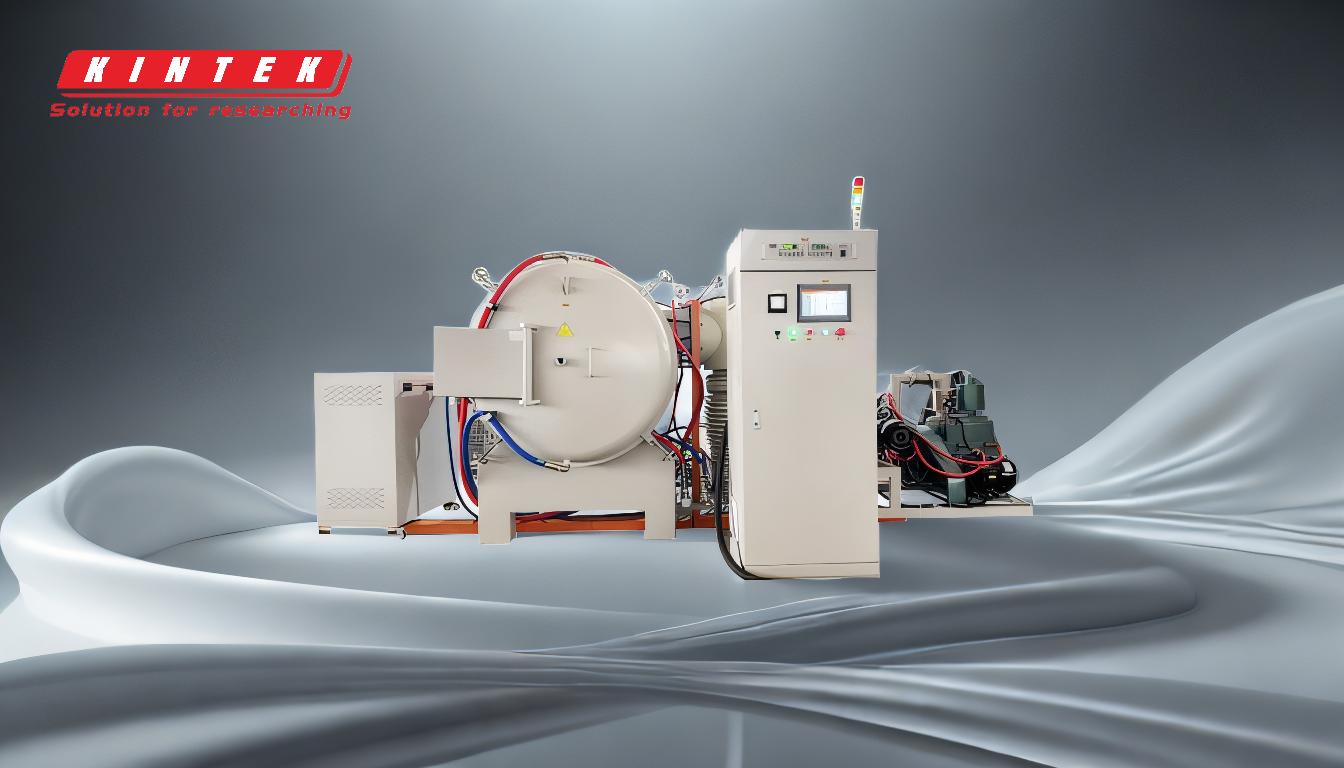
-
Brazing Process Overview:
- Brazing is a metal-joining technique that uses a filler metal with a lower melting point than the base metals being joined.
- The filler metal is heated until it melts and flows into the joint by capillary action, creating a strong bond upon cooling.
- Unlike welding, brazing does not melt the base metals, which helps maintain their structural integrity.
-
Applications in the Automotive Industry:
- Heat Exchangers: Brazing is widely used in the production of radiators, condensers, and evaporators. These components require leak-proof joints to ensure efficient heat transfer and system performance.
- Fuel Systems: Brazing is used to join components in fuel lines, tanks, and injectors, where leak-proof and corrosion-resistant joints are essential.
- Exhaust Systems: The high-temperature resistance of brazed joints makes them ideal for exhaust manifolds and catalytic converters.
- Electrical Components: Brazing is used to create reliable electrical connections in sensors, switches, and wiring harnesses.
-
Advantages of Brazing in Automotive Manufacturing:
- Joining Dissimilar Metals: Brazing allows for the joining of different metals, such as aluminum and steel, which is common in automotive design.
- High Strength and Durability: Brazed joints are strong and can withstand mechanical stress, vibration, and thermal cycling.
- Corrosion Resistance: The filler metals used in brazing often provide excellent resistance to corrosion, extending the lifespan of automotive components.
- Precision and Cleanliness: Brazing produces clean, precise joints with minimal distortion, which is crucial for high-performance automotive systems.
-
Types of Brazing Techniques Used in Automotive Industry:
- Torch Brazing: A handheld torch is used to heat the joint and filler metal. This method is versatile and suitable for small-scale or repair work.
- Furnace Brazing: Components are placed in a controlled atmosphere furnace, ensuring uniform heating and high-quality joints. This method is ideal for mass production.
- Induction Brazing: An induction coil generates heat in the joint area, allowing for rapid and localized heating. This technique is often used for high-precision applications.
- Vacuum Brazing: Performed in a vacuum environment, this method prevents oxidation and is used for critical components requiring high purity.
-
Materials Used in Automotive Brazing:
- Filler Metals: Common filler metals include silver-based alloys, copper-based alloys, and aluminum-based alloys. The choice depends on the base metals and application requirements.
- Fluxes: Fluxes are used to clean the metal surfaces and prevent oxidation during the brazing process. They are essential for achieving strong, defect-free joints.
-
Quality Control and Testing:
- Automotive brazed joints undergo rigorous testing to ensure they meet industry standards. Common tests include visual inspection, pressure testing, and metallurgical analysis.
- Non-destructive testing methods, such as X-ray and ultrasonic testing, are used to detect internal defects without damaging the components.
-
Future Trends in Automotive Brazing:
- Lightweight Materials: As the automotive industry shifts toward lightweight materials like aluminum and advanced composites, brazing techniques are being adapted to join these materials effectively.
- Automation: The use of robotic systems for brazing is increasing, improving precision, consistency, and production efficiency.
- Eco-Friendly Processes: There is a growing focus on developing environmentally friendly fluxes and filler metals to reduce the environmental impact of brazing.
Brazing plays a vital role in the automotive industry by enabling the production of high-performance, reliable, and durable components. Its versatility, strength, and ability to join dissimilar metals make it an indispensable process in modern automotive manufacturing.
Summary Table:
Aspect | Details |
---|---|
Process Overview | Joins metals using a filler metal that melts and flows into the joint. |
Applications | Heat exchangers, fuel systems, exhaust systems, electrical components. |
Advantages | Joins dissimilar metals, high strength, corrosion resistance, precision. |
Techniques | Torch, furnace, induction, and vacuum brazing. |
Materials | Silver, copper, and aluminum-based filler metals with fluxes. |
Quality Control | Visual inspection, pressure testing, X-ray, and ultrasonic testing. |
Future Trends | Lightweight materials, automation, eco-friendly processes. |
Ready to enhance your automotive manufacturing process with brazing? Contact our experts today to learn more!