Calculating the capacity of a lab filter press involves understanding its key components, operational parameters, and the specific requirements of the filtration process. The capacity is typically determined by factors such as the volume of slurry to be processed, the filtration area, the number of filter plates, and the cycle time. By analyzing these elements, you can estimate the throughput and efficiency of the filter press, ensuring it meets your laboratory or industrial needs.
Key Points Explained:
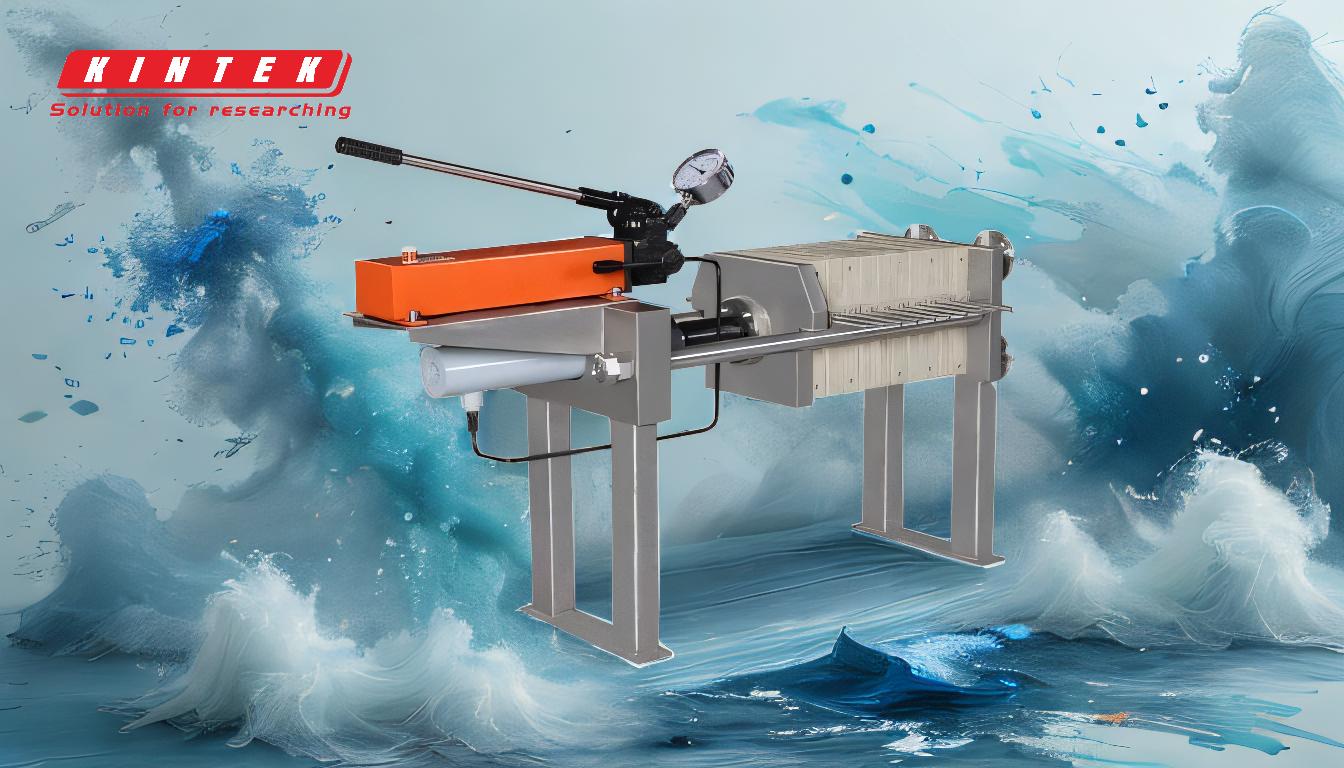
-
Understanding the Components of a Filter Press
- A filter press consists of four main components: the frame, filter plates, manifold (piping and valves), and filter cloth.
- The filter plates provide the surface area for filtration, while the filter cloth acts as the medium that captures solid particles.
- The manifold controls the flow of slurry and filtrate, ensuring efficient operation.
- These components collectively determine the overall capacity and performance of the filter press.
-
Determining Filtration Area
- The filtration area is a critical factor in calculating capacity. It is calculated by multiplying the area of one filter plate by the total number of plates.
- For example, if each plate has an area of 0.5 m² and there are 20 plates, the total filtration area is 10 m².
- A larger filtration area allows for higher throughput, making it essential for processing larger volumes of slurry.
-
Calculating Slurry Volume and Solid Content
- The volume of slurry to be processed and its solid content directly impact the filter press capacity.
- For instance, if you have 1000 liters of slurry with 10% solid content, the filter press must handle 100 liters of solids.
- This information helps in selecting the appropriate filter press size and estimating the number of cycles required.
-
Cycle Time and Throughput
- Cycle time includes filling, filtration, cake washing (if needed), cake drying, and discharge.
- Shorter cycle times increase throughput, while longer cycles may be necessary for more challenging filtration tasks.
- For example, a filter press with a cycle time of 2 hours can process 12 cycles per day, while one with a 1-hour cycle time can handle 24 cycles.
-
Practical Example of Capacity Calculation
- Suppose you have a slurry volume of 2000 liters with 15% solid content, and the filter press has a total filtration area of 15 m².
- The solid volume is 300 liters (2000 x 0.15).
- If each cycle processes 50 liters of solids, you would need 6 cycles to complete the task.
- With a cycle time of 1.5 hours, the total processing time would be 9 hours.
-
Optimizing Filter Press Performance
- Use high-quality filter cloths to maximize filtration efficiency and reduce clogging.
- Regularly inspect and maintain the filter plates and manifold to ensure smooth operation.
- Adjust operational parameters, such as pressure and flow rate, to achieve optimal results.
By carefully analyzing these factors, you can accurately calculate the capacity of a lab filter press and ensure it meets your specific filtration requirements. This approach not only enhances efficiency but also extends the lifespan of the equipment.
Summary Table:
Key Factor | Description | Example |
---|---|---|
Filtration Area | Total area of filter plates; calculated by multiplying plate area by plate count | 20 plates × 0.5 m² = 10 m² |
Slurry Volume | Total volume of slurry to be processed | 1000 liters with 10% solids = 100 liters of solids |
Cycle Time | Time for one complete filtration cycle (filling, filtration, drying, discharge) | 2-hour cycle = 12 cycles/day; 1-hour cycle = 24 cycles/day |
Solid Content | Percentage of solids in the slurry | 15% solids in 2000 liters = 300 liters of solids |
Throughput | Volume of solids processed per cycle | 50 liters of solids per cycle × 6 cycles = 300 liters in 9 hours |
Need help calculating your filter press capacity? Contact our experts today for tailored solutions!