Steel production in an induction furnace involves using an induction coil powered by electric current to melt metallic charges, such as scrap steel or iron. The process begins with loading the charge into the furnace, followed by energizing the induction coil to generate a magnetic field. This field induces eddy currents within the metal, causing it to heat up and melt. Once the molten steel reaches a temperature of approximately 1650°C, it is tapped into a steel ladle for further refining or casting. The use of advanced technologies like IGBT induction furnaces enhances efficiency and control in this process.
Key Points Explained:
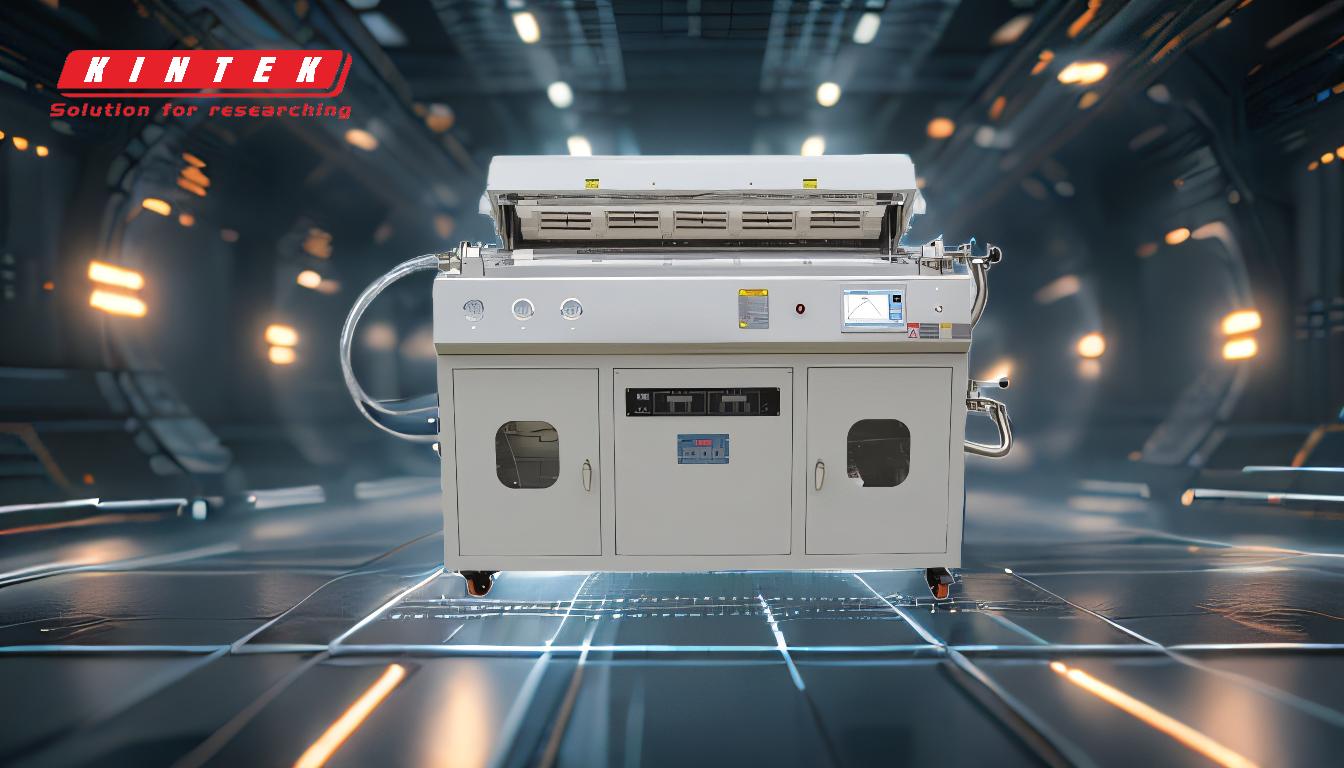
-
Induction Furnace Basics:
- An induction furnace is a type of electric furnace that uses electromagnetic induction to heat and melt metals.
- It consists of an induction coil, a crucible to hold the metallic charge, and a power supply system.
- The furnace is highly efficient and capable of producing high-quality steel with minimal impurities.
-
Role of the Induction Coil:
- The induction coil is powered by alternating current (AC), which generates a rapidly alternating magnetic field.
- This magnetic field induces eddy currents within the metallic charge, causing it to heat up due to electrical resistance.
- The heat generated is sufficient to melt the metal, creating a liquid bath.
-
Charging and Melting Process:
- The metallic charge, typically scrap steel or iron, is loaded into the furnace.
- The induction coil is energized, and the magnetic field begins to heat the charge.
- The melting process is rapid and energy-efficient, with temperatures reaching up to 1650°C.
-
Temperature Control and Tapping:
- Precise temperature control is crucial to ensure the molten steel has the desired properties.
- Once the molten steel reaches the required temperature, it is tapped into a steel ladle.
- The ladle is used for further refining, alloying, or casting into final products.
-
Advantages of IGBT Induction Furnaces:
- IGBT induction furnaces use insulated gate bipolar transistors (IGBTs) for power control, offering higher efficiency and better performance.
- These furnaces provide precise control over the melting process, reducing energy consumption and improving steel quality.
- They are also more compact and have a longer operational life compared to traditional induction furnaces.
-
Applications and Benefits:
- Induction furnaces are widely used in steel manufacturing due to their ability to produce high-quality steel with consistent properties.
- They are particularly suitable for small to medium-scale production and for recycling scrap metal.
- The process is environmentally friendly, with lower emissions and energy consumption compared to other steelmaking methods.
By understanding these key points, one can appreciate the efficiency and precision of steel production in an induction furnace, especially when enhanced by technologies like IGBT induction furnaces.
Summary Table:
Key Step | Description |
---|---|
Induction Furnace Basics | Uses electromagnetic induction to heat and melt metals, ensuring minimal impurities. |
Role of Induction Coil | Generates a magnetic field to induce eddy currents, heating the metal to 1650°C. |
Charging and Melting | Scrap steel or iron is loaded and melted rapidly, achieving energy efficiency. |
Temperature Control | Precise control ensures molten steel has desired properties before tapping. |
IGBT Advantages | IGBT furnaces offer higher efficiency, better control, and longer operational life. |
Applications | Ideal for small to medium-scale production and environmentally friendly recycling. |
Discover how induction furnaces can revolutionize your steel production—contact our experts today!