The duration of an induction heating cycle depends on several factors, including the material being heated, the desired temperature, the power of the induction heating system, and the size and shape of the workpiece. Generally, induction heating cycles are faster than traditional heating methods due to the direct and localized nature of the process. For example, small parts can be heated to high temperatures in seconds, while larger or more complex components may take minutes. The process is highly efficient, as it minimizes heat loss and allows for precise control over heating parameters.
Key Points Explained:
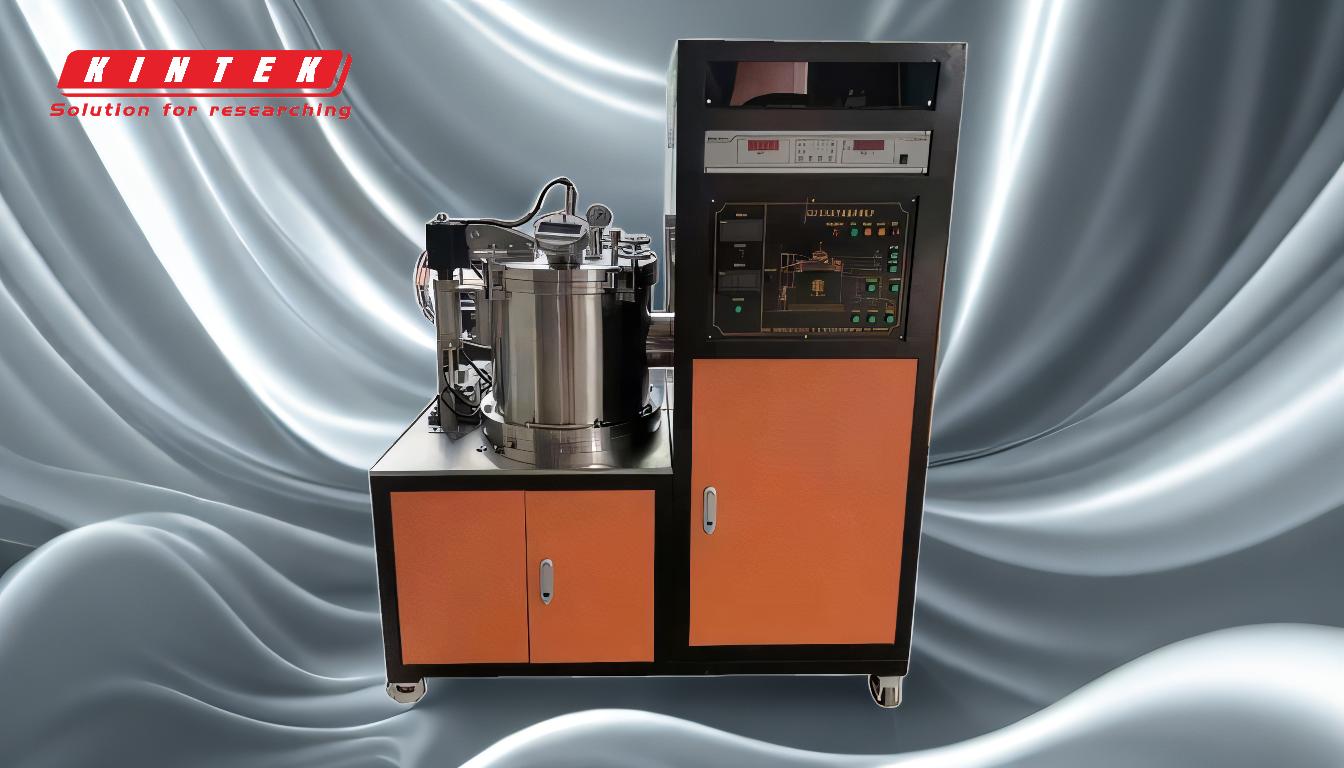
-
Factors Influencing Heating Cycle Duration:
- Material Properties: Different materials have varying electrical and thermal conductivities, which affect how quickly they heat up. For instance, metals like steel heat faster than materials with lower conductivity.
- Power of the Induction System: Higher power systems can deliver more energy in a shorter time, reducing the heating cycle duration.
- Workpiece Size and Shape: Larger or thicker workpieces require more time to heat uniformly, while complex shapes may need adjustments to ensure even heating.
- Desired Temperature: Higher target temperatures generally require longer heating times, especially if the material has a high specific heat capacity.
-
Typical Heating Times:
- Small Parts: Small components, such as fasteners or small gears, can be heated to high temperatures (e.g., 800°C to 1200°C) in just a few seconds.
- Medium-Sized Parts: For medium-sized components like shafts or rings, heating times typically range from 10 seconds to a few minutes, depending on the material and target temperature.
- Large or Complex Parts: Larger workpieces, such as large gears or plates, may take several minutes to heat uniformly, especially if the material is thick or has low thermal conductivity.
-
Efficiency and Precision:
- Induction heating is highly efficient because it directly heats the workpiece without heating the surrounding environment. This reduces energy waste and shortens cycle times.
- The process allows for precise control over temperature and heating patterns, which is crucial for applications like hardening, brazing, or annealing.
-
Applications and Examples:
- Hardening: Induction hardening cycles are often short, ranging from a few seconds to a minute, as only the surface layer needs to be heated.
- Brazing: Brazing cycles may take a few minutes, depending on the joint size and the materials involved.
- Annealing: Annealing processes typically require longer heating cycles, often several minutes, to ensure uniform heating and proper microstructure transformation.
-
Comparison with Traditional Heating Methods:
- Induction heating is significantly faster than methods like furnace heating, which can take hours to reach the desired temperature.
- The localized nature of induction heating reduces the risk of overheating or damaging adjacent areas, making it ideal for precision applications.
In summary, the duration of an induction heating cycle varies widely based on the application and workpiece characteristics. However, it is generally faster and more efficient than traditional heating methods, making it a preferred choice for many industrial processes.
Summary Table:
Factor | Impact on Heating Time |
---|---|
Material Properties | Metals like steel heat faster; lower conductivity materials take longer. |
Power of Induction | Higher power systems reduce cycle times by delivering more energy quickly. |
Workpiece Size/Shape | Larger or thicker parts require more time; complex shapes may need adjustments. |
Desired Temperature | Higher temperatures generally require longer heating times. |
Typical Heating Times | Small parts: seconds; medium parts: 10 seconds to minutes; large parts: several minutes. |
Want to optimize your induction heating process? Contact our experts today for tailored solutions!