The lifespan of PVD (Physical Vapor Deposition) coatings varies significantly depending on several factors, including the substrate material, coating thickness, bond strength, and environmental conditions. In general, PVD coatings are highly durable and can last anywhere from 10 years to hundreds of years. They are known for their superior resistance to corrosion, abrasion, and wear, making them ideal for demanding applications. In specific industries, such as jewelry, PVD coatings can last up to 10 years with proper application and maintenance. The durability of PVD coatings makes them a preferred choice over traditional finishes, ensuring long-term performance in various applications.
Key Points Explained:
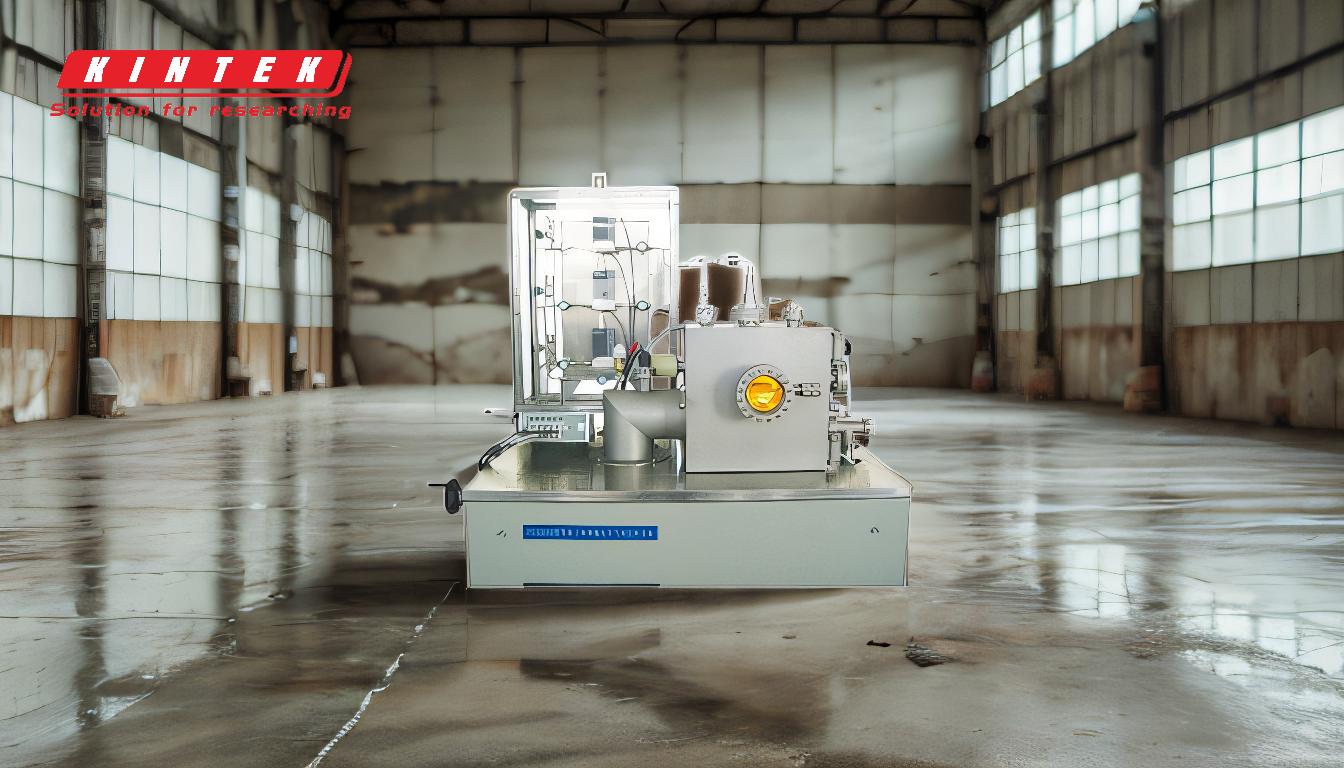
-
Durability of PVD Coatings:
- PVD coatings are renowned for their exceptional durability, often considered the most durable coatings available in the market.
- They are highly resistant to corrosion, abrasion, and wear, which contributes to their long lifespan.
- The superior quality of PVD coatings ensures they outlast traditional finishes, making them suitable for demanding applications.
-
Lifespan Range:
- The lifespan of PVD coatings can range from 10 years to hundreds of years.
- This wide range is due to the variability in application conditions, substrate materials, and coating thickness.
-
Factors Influencing Lifespan:
- Substrate Material: The type of material being coated plays a significant role in determining the longevity of the PVD coating.
- Coating Thickness: Thicker coatings generally offer better protection and longer lifespan.
- Bond Strength: The strength of the bond between the coating and the substrate affects the durability of the coating.
- Environmental Conditions: Exposure to high temperatures, wear, and other environmental factors can impact the lifespan of the coating.
-
Industry-Specific Lifespan:
- In the jewelry industry, PVD coatings can last up to 10 years if applied correctly and maintained properly.
- These coatings enhance the durability of jewelry, protecting it against corrosion and wear, which is crucial for maintaining the appearance and integrity of the pieces.
-
Applications and Performance:
- PVD coatings are used in a variety of demanding applications where durability is critical.
- Their robust temperature tolerance, impact strength, and excellent abrasion and corrosion resistance make them ideal for use in harsh environments.
-
Comparison with Traditional Finishes:
- PVD coatings are far more durable than traditional finishes, offering superior quality and longevity.
- This makes them a preferred choice for applications where long-term performance and protection are essential.
In summary, the lifespan of PVD coatings is influenced by multiple factors, but they are generally known for their exceptional durability and long-lasting performance. Whether in industrial applications or consumer products like jewelry, PVD coatings provide superior protection and longevity compared to traditional finishes.
Summary Table:
Key Factor | Impact on Lifespan |
---|---|
Substrate Material | Determines coating adhesion and durability. |
Coating Thickness | Thicker coatings offer better protection and longer lifespan. |
Bond Strength | Stronger bonds enhance durability and resistance to wear. |
Environmental Conditions | Exposure to wear, corrosion, and high temperatures can reduce lifespan. |
Industry-Specific Lifespan | Jewelry coatings last up to 10 years with proper application and maintenance. |
Want to learn more about PVD coatings and their benefits? Contact us today for expert advice!