Sintering is a critical process in material manufacturing that involves applying heat and pressure to compact powders into solid materials without melting them. This process significantly influences the mechanical properties of the final product, such as strength, hardness, and durability, by altering the microstructure, including grain size, pore size, and grain boundary distribution. For instance, sintering can transform phases within a material, like converting α-SI3N4 to β-SI3N4, which enhances hardness. However, excessive sintering time can lead to defects due to abnormal grain growth. The sintering temperature also plays a crucial role; for example, ceramics sintered at 900°C exhibit higher compressive strength but may have less optimal shrinkage and porosity compared to those sintered at 800°C. Understanding these effects is essential for optimizing sintering conditions to achieve desired mechanical properties in materials.
Key Points Explained:
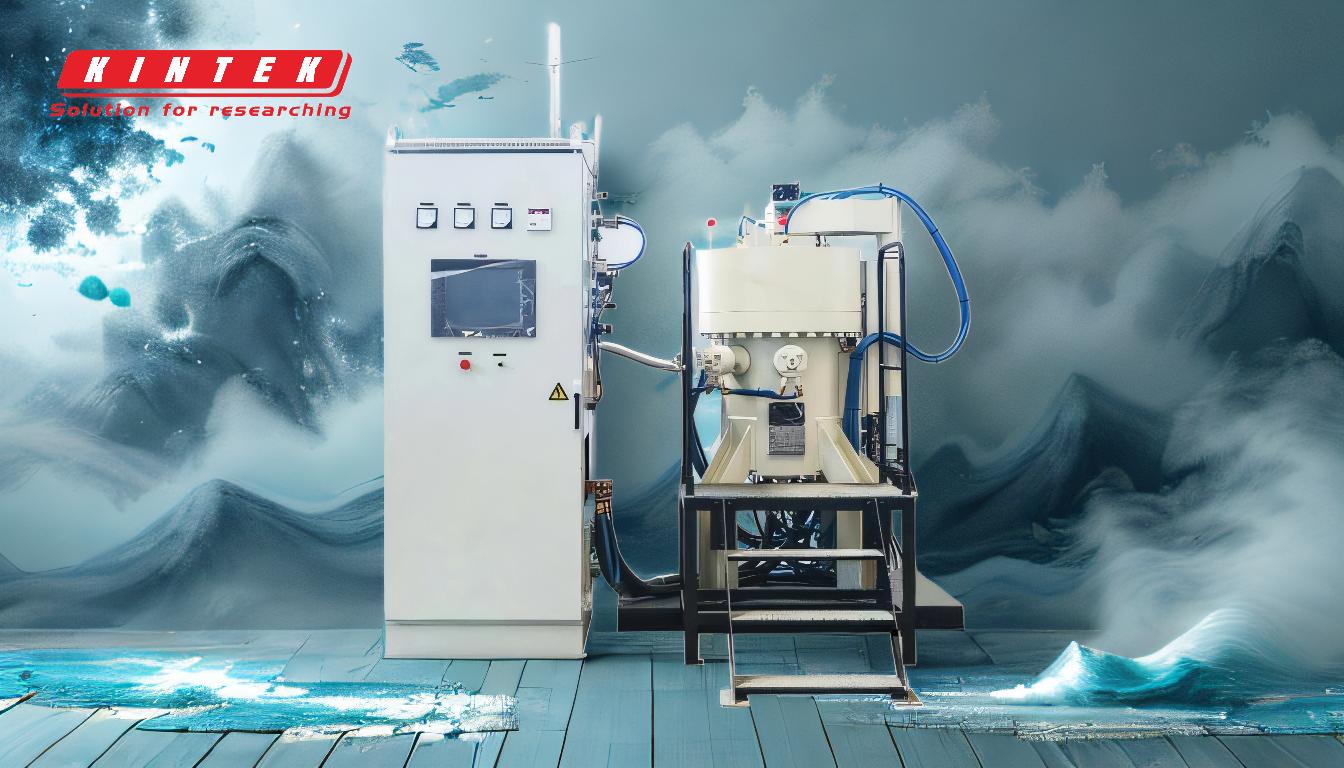
-
Microstructural Changes During Sintering:
- Sintering affects the grain size, pore size, and grain boundary distribution in the material's microstructure.
- These changes directly influence mechanical properties like strength and durability. For example, reducing porosity through sintering increases material density, enhancing its overall strength.
-
Phase Transformation and Hardness:
- Sintering can induce phase transformations, such as the conversion of α-SI3N4 to β-SI3N4, which increases hardness.
- However, prolonged sintering times can lead to abnormal grain growth, introducing defects and reducing hardness. For instance, extending sintering time from 8h to 12h decreased hardness from 1487 HV to 1321 HV.
-
Role of Sintering Temperature:
- The sintering temperature significantly impacts mechanical properties. For ceramics, a temperature of 900°C results in higher compressive strength (21.09 MPa) but may compromise shrinkage and porosity.
- Optimal sintering temperatures balance strength and structural integrity, as seen in ceramics sintered at 800°C, which exhibit better shrinkage and porosity values.
-
Importance of Controlled Cooling:
- Uncontrolled cooling during sintering, such as in Spark Plasma Sintering (SPS), can lead to the formation of undesirable phases (e.g., ω-phase), negatively affecting mechanical properties.
- Proper cooling protocols are essential to maintain the desired microstructure and mechanical performance.
-
Applications and Advantages of Sintering:
- Sintering is particularly useful for materials with high melting points or complex compositions, enabling the production of dense and strong components.
- It is a cost-effective and versatile method for manufacturing materials that are difficult to process through traditional melting and casting techniques.
By carefully controlling sintering parameters such as temperature, time, and cooling rates, manufacturers can optimize the mechanical properties of sintered materials, ensuring they meet specific application requirements. For more information on sintering equipment, visit sintering furnace.
Summary Table:
Key Factor | Impact on Mechanical Properties |
---|---|
Microstructural Changes | Alters grain size, pore size, and grain boundaries, enhancing strength and durability. |
Phase Transformation | Increases hardness (e.g., α-SI3N4 to β-SI3N4) but can cause defects with prolonged sintering time. |
Sintering Temperature | Higher temperatures (e.g., 900°C) increase compressive strength but may affect shrinkage and porosity. |
Controlled Cooling | Prevents undesirable phases (e.g., ω-phase) and maintains optimal microstructure. |
Applications | Ideal for high-melting-point materials, producing dense, strong, and cost-effective components. |
Optimize your sintering process for superior material performance—contact our experts today!