The cost of a pyrolysis process depends on several factors, including the scale of the operation, the type of feedstock used, the technology employed, and the specific costs associated with installation, infrastructure, and operational expenses. For a pyrolysis installation converting dried sludge into bio-oil with a capacity of 2 t/h, the total investment cost is approximately €1.45 million, including €1 million for the installation, €250,000 for the fume gas purifier, and €200,000 for infrastructure. Annual operational costs are around €961,000, but these can be offset by revenue generated from selling heat, energy, and bio-oils. Smaller-scale pyrolysis plants can start at $30,500, while continuous pyrolysis machines can cost upwards of $688,900. Production costs for pyrolysis oil typically range between 75 and 300 EUR per ton, depending on feedstock costs and plant scale.
Key Points Explained:
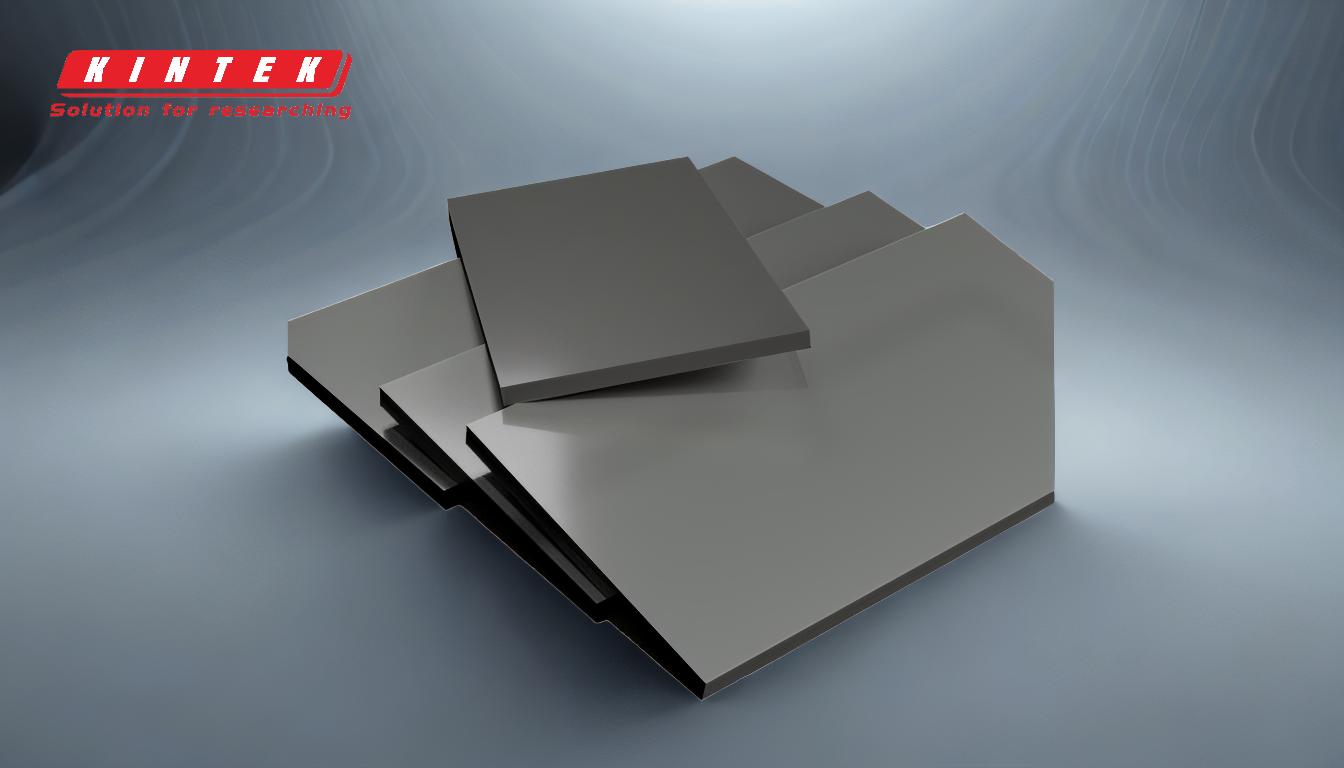
-
Investment Costs:
- Installation: For a 2 t/h pyrolysis plant converting dried sludge into bio-oil, the installation cost is approximately €1,000,000. This includes the core pyrolysis reactor and associated equipment.
- Fume Gas Purifier: An additional €250,000 is required for a fume gas purifier to ensure compliance with environmental regulations.
- Infrastructure: Infrastructure costs, such as site preparation and utilities, add another €200,000.
- Total Investment: The combined investment cost for a 2 t/h plant is €1,450,000.
-
Operational Costs:
- Annual Costs: The annual operational cost for the plant is €961,000. This includes labor, maintenance, feedstock processing, and other recurring expenses.
- Revenue Offsets: These costs can be partially or fully offset by profits from selling heat, energy, and bio-oils, depending on market conditions and product demand.
-
Cost Variability Based on Scale:
- Small-Scale Plants: A small-scale biomass pyrolysis plant can start at $30,500. These plants are energy-efficient and often use recycled combustible gas as fuel, reducing operational costs.
- Continuous Pyrolysis Machines: Larger, continuous pyrolysis machines start at $688,900, with costs increasing for higher-capacity units.
-
Production Costs of Pyrolysis Oil:
- Cost Range: The production cost of pyrolysis oil typically ranges between 75 and 300 EUR per ton (4 to 18 EUR/GJ).
- Factors Influencing Cost: These costs depend on feedstock costs (including pre-treatment), plant scale, and the type of technology used. Feedstock costs can range from 0 to 100 EUR per ton (0 to 1.9 EUR/GJ).
-
Economic Feasibility:
- Feedstock Availability: The economics of pyrolysis are heavily influenced by local feedstock availability and costs. Areas with reliable and low-cost feedstock sources are more economically viable for pyrolysis plants.
- Regulatory Environment: Restrictive landfill policies and incentives for reducing fossil carbon use can enhance the economic viability of pyrolysis projects.
- Revenue Streams: Revenue from selling pyrolysis products (bio-oil, heat, and energy) plays a critical role in offsetting operational costs and achieving profitability.
-
Factors Affecting Pyrolysis Costs:
- Feedstock Costs: The cost and availability of feedstock are significant determinants of overall pyrolysis economics. Cheaper and more abundant feedstocks improve profitability.
- Technology Type: Advanced pyrolysis technologies may have higher upfront costs but can offer better efficiency and product yields.
- Plant Scale: Larger plants benefit from economies of scale, reducing per-unit production costs.
- Local Support and Incentives: Government incentives, grants, or subsidies can significantly reduce the financial burden of setting up and operating pyrolysis plants.
By carefully considering these factors, stakeholders can better estimate the costs associated with pyrolysis processes and make informed decisions about investment and operation.
Summary Table:
Cost Component | Details |
---|---|
Investment Costs | - Installation: €1,000,000 (2 t/h plant) |
- Fume Gas Purifier: €250,000 | |
- Infrastructure: €200,000 | |
- Total Investment: €1,450,000 | |
Operational Costs | - Annual Costs: €961,000 |
- Revenue Offsets: Heat, energy, and bio-oil sales | |
Small-Scale Plants | Starting at $30,500 |
Continuous Pyrolysis | Starting at $688,900 |
Pyrolysis Oil Production | 75–300 EUR/ton (4–18 EUR/GJ) |
Key Factors | Feedstock costs, technology type, plant scale, local incentives |
Ready to explore pyrolysis solutions for your needs? Contact our experts today for a detailed consultation!